When automating voltage measurements, is it better to go with a programmable Digital Multimeter (DMM) or a computerized data acquisition (DAQ) card? With high-end DAQ cards costing about the same as an entry-level programmable DMM, it's a natural question, especially now that PCs are such a common fixture in business, industry, and academia. An effective choice between a DAQ card and a general-purpose, programmable DMM hinges on many criteria which can relate as much to user skills, operating convenience and the application as they do instrument performance.
This discussion compares, in a general way, the DMM and DAQ card in terms of accuracy, resolution, noise, and programming. DMM and DAQ products priced around $1000 were reviewed because this price point seems to represent the best intersection of comparable measurement capabilities and performance.
Trade-Offs in Measurement Capabilities
To be realistic, a PC-based data acquisition card will not replace the DMM in every application. The typical maximum input to a DAQ card is a nominal ±10VDC because these cards are powered by the PC expansion slot which supplies ±12 to ±15 VDC. The DAQ input can only come within a couple of volts of the power supply rails before amplifiers on the card saturate. Some electrical measurements, such as high voltage, AC, current and resistance, are easier and more direct with a DMM. On the other hand, DAQ cards usually offer multiple channels of analog input, plus other analog and digital I/O capabilities which can be more useful than resistance or current measurements in some applications.
Unipolar vs. Bipolar Measurements
For DC measurements with a DMM, there is nothing the user needs to do concerning measurement polarity. The typical DMM display is bipolar, and automatically indicates positive or negative levels. Likewise, most DAQ cards enable you to select between bipolar and unipolar measurement configurations. Bipolar mode most resembles the DMM, with the DAQ input able to accommodate positive or negative levels. A reading at the input range's negative limit corresponds to 0 counts from the card's A/D converter, while a maximum positive input results in the full number of A/D counts.
Most DAQ cards can also be configured for single-ended mode where the card's lower measurement limit is 0 volts, corresponding to 0 A/D counts. Available A/D counts are divided over half the voltage range, as compared to bipolar measurement. As a result, the resolution of the measurement improves by a factor of two. For example, a 12-bit converter set up for a ±5V bipolar input provides a resolution of 10V total/4096 bits, or approximately 2.44mV/bit. For unipolar mode, resolution becomes 1.22mV/bit.
A minor concern with unipolar mode is that a signal of 0V cannot consistently produce readings of 0 A/D counts (or 0V). The typical random jitter in the A/D's least significant bit (LSB) results in the average measurement being somewhere between 0 and 1 count.This situation is of limited importance in most practical applications, and does not apply to bipolar mode - a good reason to simply go with a bipolar configuration.
Resolution
An important consideration in making any digitized measurement is resolution. However, the resolutions of DMMs and DAQ cards are expressed differently, complicating (but not preventing) a direct comparison.
The resolution of a DMM is usually expressed as a number of digits. Better bench instrument displays have 5½ digits (199999 counts) or more. Typical DMM displays are 3½ digits (1999 counts) or 4½ digits (19999 counts). The use of a polarity sign effectively doubles the number of counts to about 4000 counts (-1999 to +1999) for a 3½ digit display, or 40,000 counts for a 4½ digit display.
Data acquisition cards usually specify A/D converter resolution as a number of bits, with 12-bit and 16-bit A/D converters being most common. These resolutions correspond to 4096 and 65536 A/D counts, respectively. Thus, for bipolar measurements, a 12-bit A/D is comparable to a 3½ digit DMM display, while a 16-bit A/D provides resolution slightly better than 4½ digits. Unipolar measurement mode does not appreciably change the equivalent number of DMM digits.
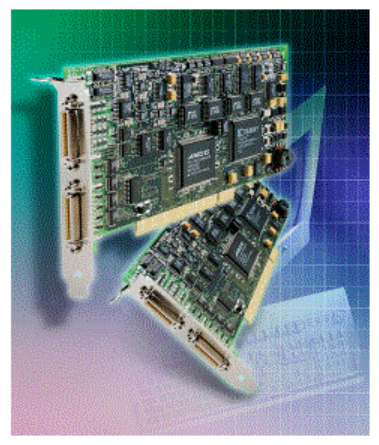
Accuracy and Drift
Accuracy is an important specification, both for discrete instruments and computer-bound data acquisition cards. Calibration at the time of manufacture can provide the specified accuracy, but the quality of design and components will largely determine how well the product holds to these specifications once it is removed from the calibration environment.
The two components of a typical accuracy specification are gain and offset. These criteria may be expressed differently for DAQ cards and DMMs, but the figure can usually be reworked to yield some percentage of reading plus some number of A/D or display counts. A full analysis of digital measurement accuracy is outside the intent of this article. However, a typical accuracy spec for products reviewed for this article is 0.01% to 0.05% of reading (gain) ±1 to 2 A/D counts (offset). Again, there was not a substantial difference between DMM and DAQ figures.
What is perhaps more important to accurate measurement is the selected measurement range. As a general rule, optimum measurements result when the signal of interest falls in the upper third of the selected range. Measuring "down in the mud" robs any instrument of its best performance, and can overwhelm intrinsic accuracy. The usual jitter in the least significant bit of a digitized measurement can result in substantial uncertainty when a measurement consists of only a few A/D counts to begin with - a concept applicable to both DMMs and DAQ cards.
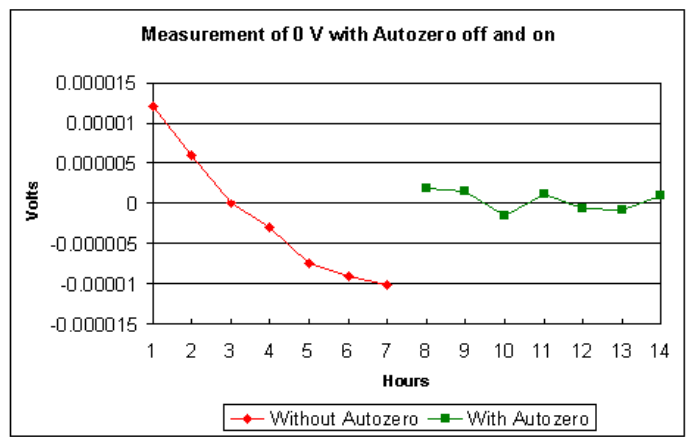
Figure 2 demonstrates the effect of an "autozero" adjustment on the drift (offset) stability of the KPCI-3108 card shown in Figure 1. This card's autozero feature automatically disconnects the signal, shorts the card's input, and readjusts amplifier zero between successive measurements.
Measurement Range
Virtually all DMMs offer multiple ranges, and the same is true of most DAQ cards. The usual ranging scheme on DMMs is decade-based, e.g. 0.2V, 2V, 20V, 200V, etc.Conversely, DAQ cards normally feature several, more closely spaced hardware and software gain selections, and are sometimes further classified as "low gain" or "high gain." The difference has to do with the amount of gain applied to the input signal by the card's instrumentation amplifier, before the signal is digitized. A typical low-gain card might provide gains of 1', 2', 4', and 8', corresponding to measurement ranges of ±10, ±5, ±2.5, and ±1.25 VDC. A high-gain card offers additional sensitive ranges which can extend the measurement capability to sub-millivolt levels. Therefore, a DAQ card will permit you to more closely tailor the input range to the voltage level being measured.Beyond 10VDC, a voltage divider can permit the DAQ card to measure higher voltages, and other types of user-supplied external circuitry can make the DAQ card more suitable for AC or resistance measurements. Ultimately, the DMM will prove to be a simpler, more direct method.
Noise Management and Differential Mode
First-time DAQ users experienced with benchtop instruments can sometimes become confused when reviewing results from a DAQ card. There are significant differences between how the two types of instruments operate. These differences can mislead the user into assuming the DAQ card is excessively noisy.
DMMs tend to make average or integrated measurements, and may use filters or other techniques to improve measurement consistency at the expense of speed (typically, a few readings per second). Conversely, even entry-level data acquisition cards make instantaneous measurements which can be repeated every few microseconds for highspeed scans. Instantaneous readings can show significant sample-to-sample variation caused by noise in the test environment. The relatively noisy environment inside a PC can also add to measurement uncertainty. These factors can limit the ability of a plug-in DAQ card to make sensitive, single-reading measurements on the same order as bench instruments. Once you understand that the DAQ card's behavior is a natural outcome of high-speed capability, and not a defect, you can take steps to achieve measurement stability comparable to the DMM.
First, differential measurement mode can be used with most DAQ cards achieve better noise immunity. This is especially important in systems that take data from a number of different devices, or which are located a long distance from the actual input sensor.Differential mode measures the voltage difference between "channel high" and "channel low" inputs, neither of which is at ground potential. The DAQ card's instrumentation amplifier will reject any signal common to both inputs. Since noise should equally affect channel high and channel low leads, it will be stripped from the signal of interest.
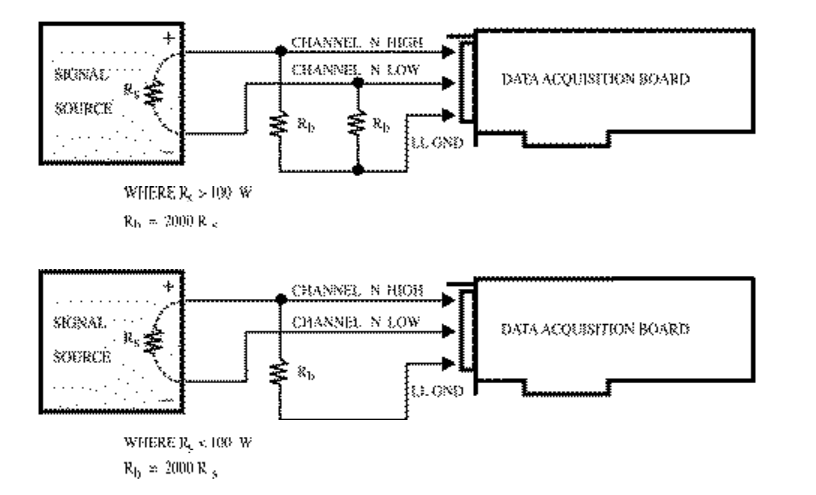
Figure 3 shows two schemes for wiring a signal source to a data acquisition differential input channel. These circuits require the addition of resistors to provide a bias current return. You can determine the value of the bias return resistors (Rb ) from the value of the source resistance (Rs), using the following relationships:
* When Rs is greater that 100W, use the connections in the upper circuit. The resistance Rb of each of the two bias return resistors must equal 2000 ' Rs .
* When Rs is less that 100W, use the connections in the lower circuit. The resistance of the bias return resistor Rb must be greater than 1000 Rs.
For applications that involve monitoring signals in noisy environments, a DAQ system with integrating conversion technique will minimize the effects of 60 Hz noise. This will require you to check specifications and features until you find a suitable board. Finally, the acquisition software can simply acquire a series of measurements at high speed and average them. This process should require only milliseconds to perform.
Software
A legitimate question concerning PC-based reading of DMMs and data acquisition systems is "How much programming is involved?" At one time, users had two choices for developing test programs: the easy but somewhat restrictive closed software package, or a more time-consuming but far more flexible open programming language. The simplicity that Windows® now brings to PC operation has filtered into data acquisition and instrument control software as well. A treatise on software development is beyond the scope of this article. However, the short answer is that the overall programming effort is similar for DMMs and DAQ systems. The most user-friendly data acquisition boards and instruments include the same types of drivers, tools, and other applications designed to simplify programming. Some can deposit measurement data directly into spreadsheets or other applications.
Conclusion
Despite the apparent physical differences between DMMs and data acquisition cards, the two measurement solutions can share a surprising degree of performance at a given price in the categories of accuracy, resolution, and programming. Many applications exist where the typical DAQ card's ability to measure up to ±10 VDC is a perfect fit. Some applications, such as measurement of voltages over ±10V, very low-level DC signals, AC, and resistance remain the stronghold of the DMM. Other considerations, such as high speed, multichannel measurements, analog and digital control, data analysis, and graphic display of results can make the data acquisition system more desirable. In the end, channel count or range may be the deciding factor in choosing one or the other solution.
Interestingly, size and portability may not be much of a concern in choosing between a DMM and a PC-based measurement system. The footprints of the common mini-tower desktop PC chassis, laptop computers, and DMMs are similar. A desktop PC may impose no sacrifice at all in desktop real estate if you are already using the PC for other tasks.
Development of data acquisition software has followed the general trend set by the now common Windows® operating system. Many tools exist to enable data collection using popular application programs and languages, frequently with very little actual program development on the part of the user. Software products even exist to create virtual DMMs and other instruments on the PC monitor - just the thing when you just can't give up that familiar DMM front panel but want multiple channels and other features of the DAQ card.