When comparing past, present and future automobiles, one trend is clear: cars have become data centers on wheels. Within each vehicle, the volume of data from safety systems, onboard sensors, navigation systems, and so on and the reliance on that data—continues to grow rapidly.
This has major implications for in-vehicle networks (IVNs) in terms of speed, capacity and reliability. One consequence: In high-speed, low-latency applications, purpose-built buses such as Controller Area Network (CAN), FlexRay, Local Interconnect Network (LIN), Media-Oriented Systems Transport (MOST), and Single Edge Nibble Transmission (SENT) lack the required bandwidth. As a result, these legacy standards are gradually giving way to previously proven technologies from the world of information technology (IT).
Today’s key example is Automotive Ethernet, which spans four standards under the aegis of the Institute of Electrical and Electronic Engineers (IEEE). For now, Automotive Ethernet will coexist with multiple buses spanning numerous systems and subsystems. Consequently, different approaches to testing are necessary in the design, validation, debugging, troubleshooting, maintenance and servicing of vehicles and IVNs.
This primer provides an overview of the trends, challenges and solutions associated with the expected future evolution of IVNs.1 Our goal is not to make you an expert on the topic. Rather, our aim is to help you build a foundation for a deeper dive into the testing of IVNs. The result: you and your team will be able to accelerate new designs to production, streamline validation testing, enhance conformance testing, optimize production testing, and simplify service and postrepair testing.
Trends: Coping with More Data, Ethernet, Standardization and the Lifecycle
Today, many automobiles contain more than 80 electronic control units (ECUs). To date, CAN, LIN, FlexRay, MOST, and SENT have carried information between those ECUs and a variety of onboard systems: engine, powertrain, transmission, brakes, body, suspension, infotainment, and more (Table 1). In addition, cellular and non-cellular wireless technologies (e.g., Bluetooth®, WLAN and GNSS) are delivering external data streams to infotainment, navigation and trafficinformation systems.
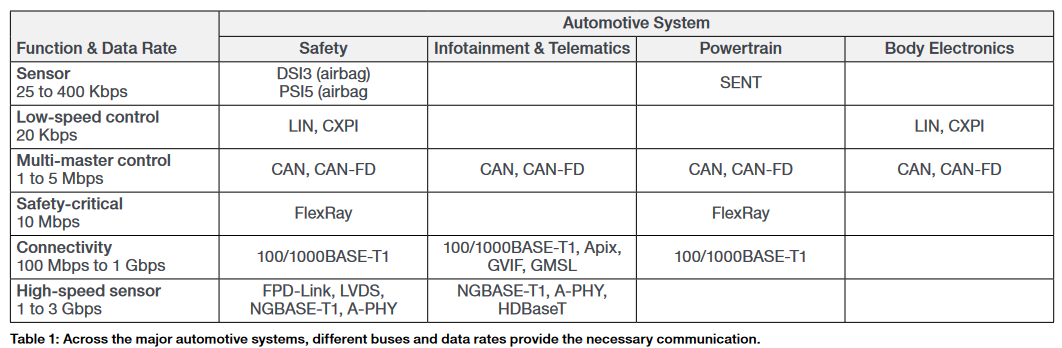
Dealing with More Data
In the years to come, we expect to see more than 100 ECUs per vehicle, with the connected in-car networks carrying many terabytes of data per day. We anticipate automobiles will continue to utilize CAN, CAN-FD, LIN, FlexRay, SENT and MOST; however, the current top-end data rates are 10 Mbps with FlexRay and 150 Mbps with MOST. To add perspective, the desire to simply “go faster” is easier said than done: the pervasive CAN bus would require a massive redesign to provide the necessary speed, security and backward compatibility.
As sensors become more numerous and more sensitive, they will generate tremendous amounts of data: imagine 10 to 20 cameras, providing a 360-degree view, all sending 1080p (now) or 4K (future) HD streams, and with pixel depth increasing from 16 to 20 to even 24 bits. The numbers add up very quickly: a single 4K camera with 24-bit pixel depth would produce 199 Mb per frame at a rate of 10 to 30 frames per second.2 Although 1 Gbps rates may be sufficient now, 10 Gbps will soon be mandatory (Figure 1).
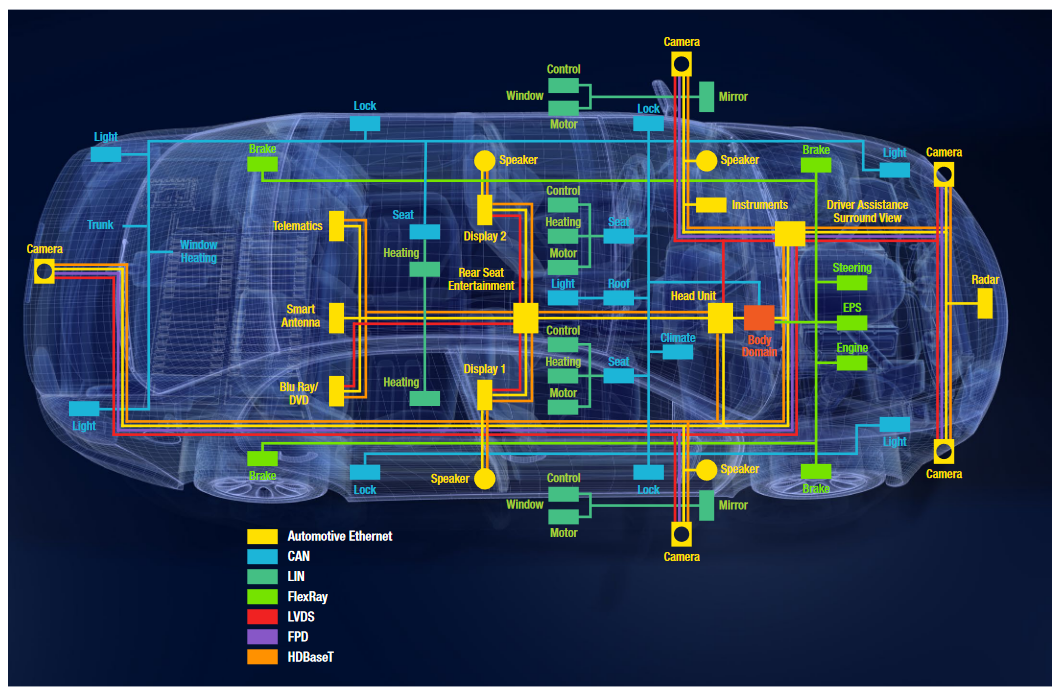
Currently, IVNs use preprocessing hardware to perform data reduction (i.e., compression) at the sensor. Unfortunately, this introduces latency, affecting response time, while also reducing picture quality, thereby limiting the useful detection distance. One emerging solution is the streaming of raw data at 2 to 8 Gbps to centralized systems on a chip (SoCs) or general processing units (GPUs) that can crunch the incoming real-time data. IVNs are moving from a flat architecture to a domain-controller architecture in which sensors stream raw data to the central processing unit.
The necessary communication flows are expanding and evolving with vehicle-to-infrastructure (V2I), vehicle-tovehicle (V2V), and vehicle-to-everything (V2X). All will play a significant role in vehicle operation and human interaction.
Shifting to Automotive Ethernet
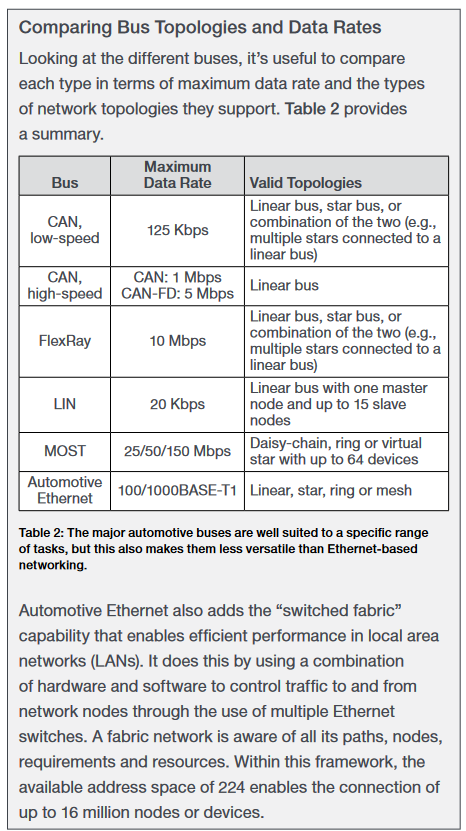
In automotive applications, optimal utilization of data requires faster throughput, lower latency, greater reliability, and higher quality of service (QoS) to ensure safe, reliable operation of the vehicle. With speeds that reach up to 10 Gbps, Automotive Ethernet will play a growing role in carrying high-speed data communications: IEEE 802.3cg, 10BASE-T1, 10 Mbps; IEEE 802.3bw, 100BASE-T1, 100 Mbps; IEEE 802.3bp, 1000BASE-T1, 1 Gbps; and IEEE 802.3ch, 10GBASE-T1, 2.5/5/10 Gbps.
Given the available data rates and the growing need for such performance, as well as the desire to reduce cabling weight, many industry watchers have issued optimistic forecasts about the uptake of Automotive Ethernet and the number of connected in-vehicle nodes.
Standardization: Gaining a New Business Advantage
Throughout the history of the auto industry, one longestablished best practice has not changed: standardization. This idea will endure because it delivers important benefits such as heightened competition among vendors, reduced component cost, and ensured interoperability.
In the realm of new-generation IVNs, examples of standardization include Automotive Ethernet, MIPI A-PHY and HDBaseT Automotive. By leveraging proven technologies from the IT world, the auto industry will gain significant new business advantages as future vehicles become data centers on wheels.
Lifecycle: Testing from Development to Maintenance
As vehicles achieve higher levels of autonomy, the potential ramifications of a system failure become more severe. To help ensure safe and reliable operation of such systems, the testing of in-vehicle networks is taking on greater importance throughout the entire lifecycle of the vehicle (Figure 2). Consequently, careful selection of system design tools and IVN test solutions that meet the needs of all of the different phases of an automobile’s lifecycle will provide far-reaching benefits to Tier 1 suppliers, automotive OEMs, and vehicle end-users.
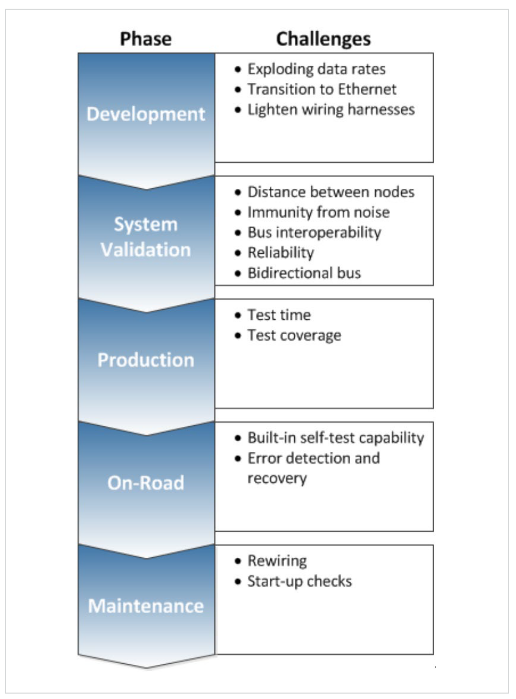
Challenges: Testing Multiple Buses Operating Side by Side
Today, vehicles incorporate a variety of communication buses operating simultaneously. Because of this, system optimization and debugging are difficult and time-consuming. Using all of these technologies in parallel, and in the restricted space of a vehicle, can lead to electromagnetic interference (EMI), poor signal quality and, potentially, critical system failure.
Testing in-vehicle networks requires reliability checks within and across the entire vehicle: interoperability, noise immunity, crosstalk, and sources of interference. Verifying operational functionality and communication reliability will span every ECU-managed and bus-connected system inside the vehicle (Figure 3). As vehicles become more data-intensive, testing will be essential to ensuring safe and reliable operation across all phases of the lifecycle: development, validation, production, maintenance, and service.
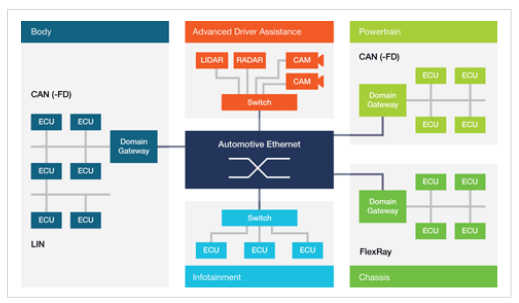
Test challenge #1: Debugging bus issues
CAN, LIN and FlexRay are relatively mature bus protocols and are designed to be robust and easy to integrate. Even so, in-vehicle communication can be affected by noise, board layout, and power-up/power-down timing. Problems can include excessive bus errors and lock-ups.
With CAN, LIN and FlexRay, common issues include troubleshooting of signal faults, debugging the decoded protocol, and making sense of multiple channels, sensors and actuators. With SENT, it is difficult to first configure an oscilloscope to decode fast- and slow-channel SENT messages and then trigger on decoded information.
As noted above, multiple buses operating simultaneously within the close confines of a vehicle can create EMI that leads to poor signal quality. Precompliance testing can help you isolate and identify the cause of signal-quality problems and bus-performance issues. It will also improve your ability to pass formal testing of EMI and electromagnetic compatibility (EMC) versus relevant standards such as CISPR 12, CISPR 25, EN 55013, EN 55022 (superseded by EN 55032), and CFR Title 47, Part 15.
Test challenge #2: Verifying electrical compliance
Ensuring reliable, low-latency data flows to, from and within the vehicle is essential to safe operation of the entire system. Unlike CAN, LIN and the others, Automotive Ethernet has a complex suite of conformance tests defined by IEEE and OPEN Alliance that includes electrical requirements to ensure compliance with the standard. These tests are often performed during design, validation and production.
With Automotive Ethernet, physical (PHY) layer electrical testing covers several key attributes of transmitter/receiver (transceiver) performance, as shown in Table 3. The specific goal is to test the compliance of physical media attachment (PMA) relative to various electrical parameters.

Figure 4 shows an example of a master transmitter timingjitter test.3 Master and slave jitter measurements can be particularly challenging given the tight compliance limits and the need to eliminate any possible sources of random or deterministic jitter.
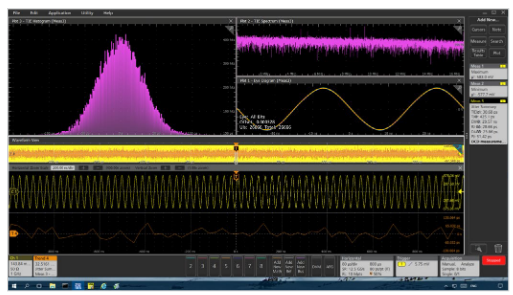
Test challenge #3: Validating protocol conformance and system performance
The common mental image for a digital signal is a simple square wave-like pulse train that has two levels, indicating "one" or "zero." In reality, most digital communication networks use multiple levels to encode more information per unit of time. One common approach is called pulse-amplitude modulation or PAM.
Automotive Ethernet uses a technique called three-level PAM or PAM3 to achieve greater data rates at the same clock frequency. In PAM3, each level must operate at a specific voltage level and within relatively tight tolerances.
These signals can be quite complicated, but an oscilloscopebased measurement called an eye diagram is a visually efficient way to determine signal performance relative to signal-encoding requirements (i.e., protocol testing). The key dimensions of an eye diagram are its height, width, linearity and thickness (Figure 5). Collectively, these provide useful information about how dependably the signal can correctly deliver the encoded information.
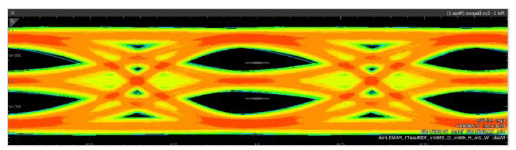
It is also important to note: Automotive Ethernet utilizes full-duplex operation, meaning the two linked devices can send and receive data simultaneously. This provides three related advantages compared to conventional shared networks. First, both devices can send and receive at once rather than needing to take turns. Second, the system has greater aggregate bandwidth. And third, full-duplex enables simultaneous conversations between different pairs of devices (e.g., Master and Slave).
Within this complexity, automotive engineers face another challenge: full-duplex communication with PAM3 signaling makes it difficult to visualize Automotive Ethernet traffic and then fully characterize signal integrity. To perform signal integrity analysis over the link, and also decode protocol in a real system environment (using an oscilloscope), designers need to look at each link separately—and this requires separation of the signals before performing any sort of analysis. This is illustrated in Figures 6 and 7, and Figure 7 utilizes Tektronix’ innovative non-intrusive Signal Separation solution.
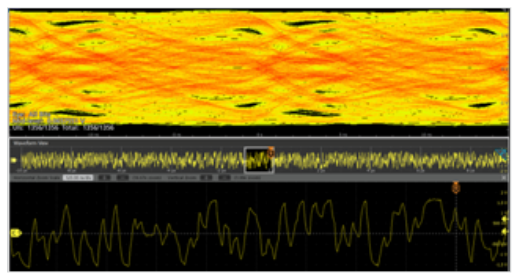
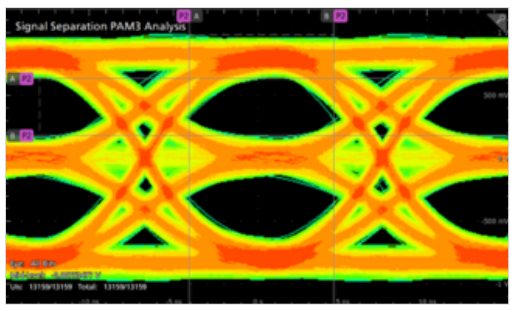
Reliable communication between nodes is critical to the automobile’s operation. That’s why we strongly recommend testing of signal integrity and protocol at the system level under various environmental conditions with different cable lengths, injected noise, etc.
Test challenge #4: Gaining insights for troubleshooting and debugging
Whether the issue is bus performance, EMI, electrical compliance or protocol conformance, two fundamental attributes determine signal quality and therefore data performance: amplitude and timing. Precise operation in both dimensions is necessary to ensure successful transmission of digital information across the bus. This becomes more difficult at faster bus rates and with increasingly complex signal-modulation techniques (e.g., PAM3).
As a starting point for debugging, six issues are especially common, and they have some well-known root causes:
- Amplitude problems: ringing, droop, runt pulses
- Edge aberrations: board layout issues, improper termination, circuit problems
- Reflections: board layout issues, improper termination
- Crosstalk: signal coupling, EMI
- Ground bounce: excessive current draw, resistance in power supply and ground-return paths
- Jitter: noise, crosstalk, timing instability
An automotive oscilloscope is the preferred measurement tool, but without sufficient frequency coverage, channel count, accessories, or on-screen analysis capabilities, troubleshooting and debugging can become tedious and time-consuming.
Solutions: Leveraging the Power of Standardization
As noted earlier, standardization is a long-established best practice in the auto industry. Stepping back to gain a wider view, this same concept can apply to the selection of solutions for the testing of IVNs. Standardization through a unified approach to testing will help you manage the cost of test. For example, choosing a test platform that can easily adapt to higher speeds will enable more efficient spending on test and measurement solutions.
In the real world, we need to consider the organizational separation of responsibilities across the lifespan of a vehicle and its onboard systems. Without a unifying strategy, common practice would lead to the gradual accumulation of random pieces of test hardware and software among separate groups. Unfortunately, a piecemeal approach to solution creation will not be sufficient for valid end-to-end testing of integrated systems or subsystems. The likely results are inconsistent measurement results, either within a development team or across activities (e.g., development, validation, production, and service) and increased test times.
Let’s take a closer look at the general and specific attributes of solutions that will help you reduce the cost of test while ensuring consistent results across the vehicle lifecycle.
Outlining the general attributes of solutions
Across all types of IVNs, the test solution must enable you to view raw real-time signals and decoded bus traffic. With mature standards such as CAN, FlexRay, LIN and SENT, an oscilloscope with protocol decoding can be used to view and assess signal quality as well as decoded bus traffic. These capabilities help you see conformance violations that are adversely affecting system performance.
Specific to Automotive Ethernet, the ability to pass conformance testing is a mandatory hurdle for semiconductor manufacturers and Tier 1 suppliers. Performing detailed signal qualification in advance of formal compliance testing will increase the likelihood of passing the required tests.
The necessary automotive bus measurements can be performed using an oscilloscope that covers the required frequency bandwidth, and is supported with appropriate probes, fixtures, signal source, and software (e.g., protocol decode and analysis). For example, the CAN bus is a differential signal. Although the oscilloscope can acquire and decode the bus using single-ended probing, differential probing will improve signal fidelity and noise immunity.
The typical test process is to subject the design to a variety of operating conditions, including stress tests, and characterize its performance. Key measurements include voltage and timing measurements, jitter analysis, and eyediagram analysis (e.g., PAM3 signaling). If or when needed, it should be easy to correlate results relative to individual compliance tests and, more valuable, correlate across the supply chain: semiconductor manufacturers, Tier 1 suppliers, and the OEM.
Exploring Tektronix solutions
Working directly with auto-industry engineers, third-party solution providers, and standards bodies, Tektronix has created an array of innovative solutions for the validation, troubleshooting, and compliance of in-vehicle networks. Tektronix solutions include industry-leading oscilloscopes, probes, signal sources, spectrum analyzers and software. With application-optimized software solutions, these solutions can be configured to address CAN, CAN-FD, FlexRay, LIN, SENT, Automotive Ethernet, and more. Tektronix software applications provide advanced analysis capabilities and also save time with automation of procedures, measurements and reporting.
Table 4 provides an overview of Tektronix solutions that address testing and analysis in three key areas: signal quality, PMA transmitter compliance, and purpose-built buses. More information is available online at www.tek.com/automotive and on the respective product pages for each family of oscilloscopes (Series 3, 4, 5, 6 and 70000).
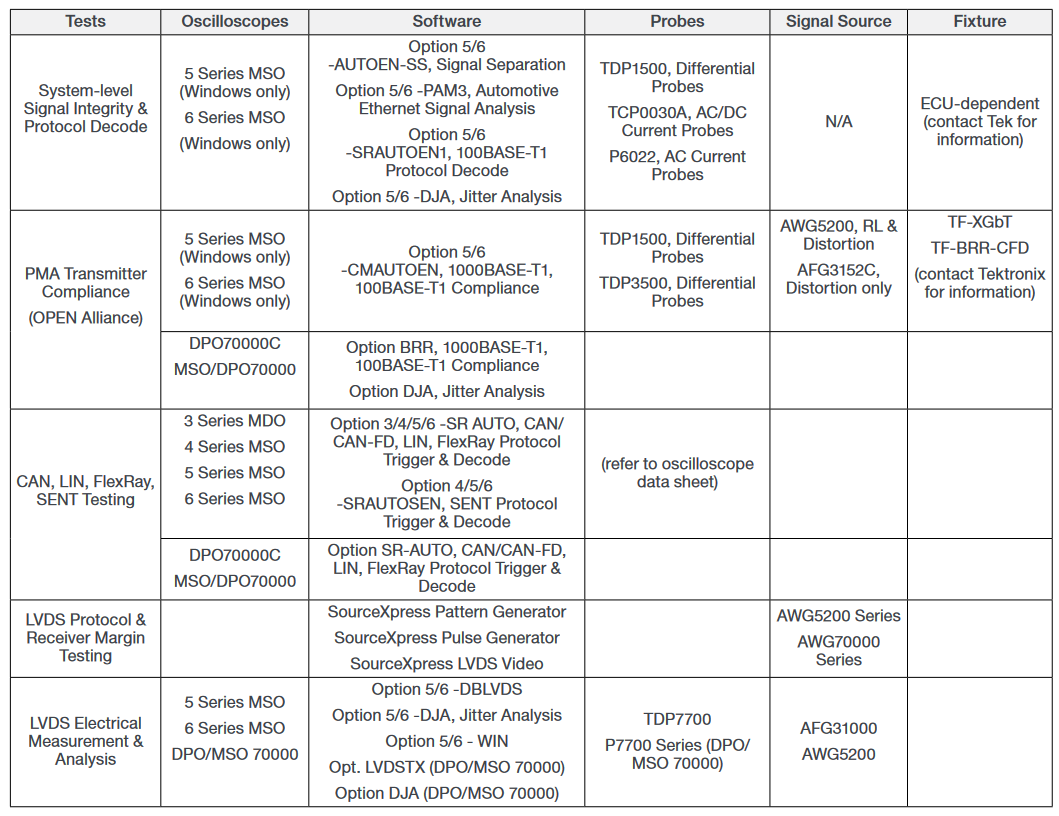
Conclusion
Ensuring reliable, low-latency data flows to, from and within a modern vehicle is essential to the safe and reliable operation of the entire system. Achieving this goal is becoming more difficult given the number of buses being used in present and future vehicle designs
In the absence of careful forethought, common practice would lead to the gradual accumulation of random pieces of test hardware and software among separate groups across the typical multi-year development timeline for a vehicle, system or subsystem. Unfortunately, a piecemeal approach to solution creation will not be sufficient for valid end-to-end testing of integrated systems or subsystems. The likely results are inefficient spending on test solutions and, equally concerning, inconsistent measurement results within a development team, across departments, or along the supply chain.
This is why Tektronix and its solution partners have created a unified approach to the testing of in-vehicle networks. Across all the major IVNs, and across the vehicle lifecycle, we can help you and your team move new designs to production faster, accelerate validation testing, enhance conformance testing, optimize production testing, and simplify service and post-repair testing. The ultimate result is a greatly enhanced ability to meet your program goals for cost and schedule.
We hope this primer has provided a foundation for a deeper dive into the testing of in-vehicle networks in general and Automotive Ethernet in particular. For more information, please contact your local Tek representative or visit the automotive section of our website.