THIS APPLICATION NOTE WILL
- Provide a basic understanding of USB 2.0 physical layer measurements and electrical compliance testing (electrical and high-speed tests)
- Describe automated testing with TekExpress-based USB 2.0 Compliance Testing software (option 5-CMUSB2), running on the 5 Series MSO mixed signal oscilloscope
- Provide information on the instruments required for each test
- List criteria for selection of equipment
For detailed specifications of the USB 2.0 bus and required testing, refer to the Universal Serial Bus Revision 2.0 Specification, available from the USB-IF at www.usb.org.
This application note uses the 5 Series MSO, equipped with Option 5-CMUSB, to illustrate USB 2.0 electrical testing techniques. However, several Tektronix oscilloscopes support USB 2.0 compliance testing. See "Serial Support for MSO/DPO/MDO Product Series"
The 5 Series MSO also supports automated protocol decoding and triggering on USB 2.0. For more information, refer to the application note "Troubleshooting USB 2.0 Problems with Your Oscilloscope"
Introduction
Engineers involved in the design, characterization and validation of Universal Serial Bus Revision 2.0 (USB 2.0) devices face pressure to speed new products to market. Tools are available to help them quickly and accurately perform electrical compliance tests recommended by the USB-Implementers Forum, Inc. (USBIF) and quickly debug their designs.
USB 2.0 is one of the most widely-used systems buses, due to its reliability, simple plug-and-play usability and cost-effectiveness.While it is not the fastest version of USB, with bit rates up to 480 Mb/s it covers a wide range of applications.
USB 2.0 device designers must properly characterize their designs and verify compliance to industry standards before they can affix the "certified" USB-IF logo to their packaging. Many designers also rely on the compliance tests to validate the performance of their devices,and to evaluate how much margin they have. An appropriate tool set is critical for performing the tests.
USB 2.0 Basics
Compliance testing is testing to determine the compliance of a system with a particular standard. This application note focuses on testing the electrical performance of the interface. Generally, this type of testing is specified as part of the standard and overseen by the standards body to ensure that devices that pass the certification process are 100% capable of interoperating with other certified devices. In this case, the standard is “Universal Serial Bus Specification, Rev 2.0” and it is administered by the USB Implementers Forum (www.usb. org).
USB 2.0 is a 4-wire serial bus:
- D+
- D-
- VBUS
- Ground
D- and D+ are responsible for carrying information through differential signaling, as well as some single-ended signal states. VBUS supplies a nominal 5V power supply to devices that derive their primary power from the host or hub.
From a testing perspective, it is important to understand a few elements of the bus:
- Host. USB 2.0 is a single-host bus. The “host” is a computer system in which the USB Host Controller is installed. This includes the host hardware platform (CPU, bus, etc.) and an operating system.
- Device. A device refers to a collection of hardware components that perform a particular function, such as a USB interface device.
- Hub. A Hub is a USB device that provides additional connections to the USB.
USB 2.0 superseded and incorporates the USB 1.1 specification which defined Low Speed (LS) and Full Speed (FS) data transfers. The USB 2.0 version adds High Speed (HS)data transfers.
DATA RATES | RISE TIMES | |
Low Speed (LS) | 1.5 Mb/s | 75 ns - 300 ns |
Full Speed (FS) | 12 Mb/s | 4 ns - 20 ns |
High Speed (HS) | 480 Mb/s | 100 ps |
USB 2.0 devices can be either self-powered (having their own power supply) or bus-powered (drawing power from the host). Hubs and Hosts can provide up to 500 mA currents and the power distribution is designed to support hot-plugging.
For USB 2.0 testing, Tektronix supports Standard A, Micro-B and Type-C connectors. For the latest Type-C testing, you must test with the recommended Type-C fixture available from USB-IF. The list of compliance measurements remains unchanged for all USB connector types.
For more information related to Type-C testing, please visit the following link from Tektronix: https://www.tek.com/wiredcommunications/consumer-standards-over-type-c
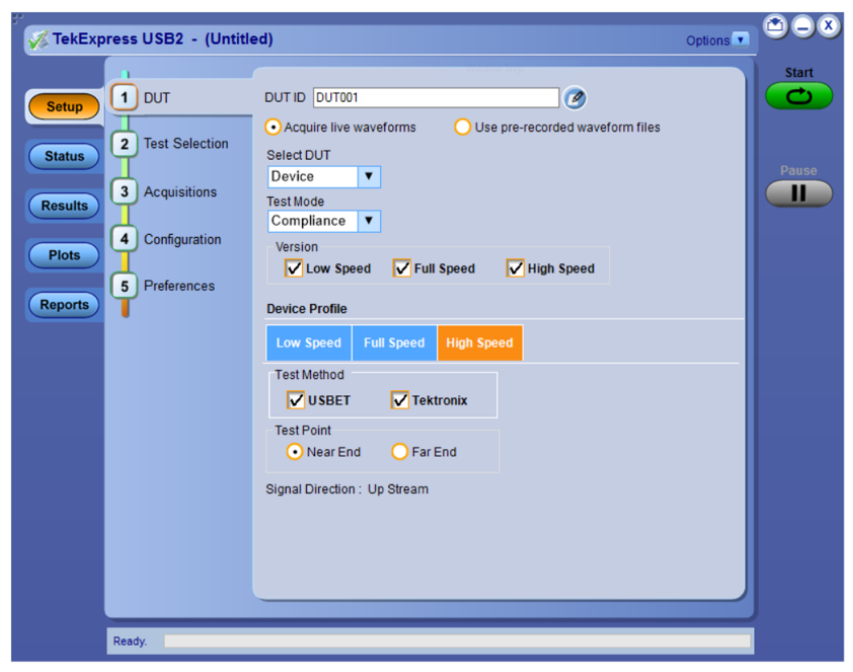
USB 2.0 Electrical Compliance Testing
Most of the electrical measurements specified by USB-IF require an oscilloscope, making it the heart of the test system. Along with the scope, testing requires appropriate probes, cables, and fixtures to route signals and provide access. Some tests require a signal source and DMM. Requirements for each test will be given later in this app note.
The USB-IF specifies compliance testing requirements and authorizes testing methods. The tests can be performed by hand, but configuration, evaluation and reporting requirements lend themselves to automation. TekExpress serial compliance software provides the engine for USB compliance testing on several Tektronix oscilloscope platforms, including the 5 Series MSO, MSO/DPO5000B Series, and DPO7000C Series.
Figure 1 shows the setup of the TekExpress USB2 (option 5-CMUSB2) compliance test package on a 5 Series MSO. This test package automates the test process, allowing designers to perform compliance tests quickly and easily. TekExpress USB2 integrates and automates the USB-IF USBET Electrical Analysis software thereby ensuring you get the same results as if you had run USBET software separately
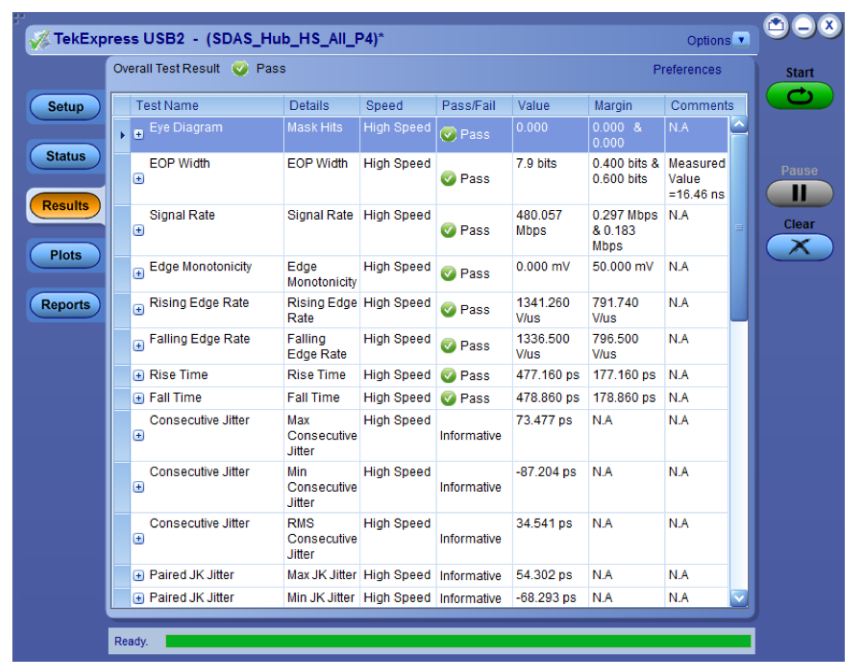
In general, you select the measurements to be performed for a particular signal speed (low, full or high speed). The application must then be configured based on tier (tier to which the DUT is connected), test point (test point of the DUT — near or far end), and direction of traffic (upstream or downstream testing), as shown in Figure 1. After completing these steps, you run the application. (For high speed testing, tier selection is not applicable and near end is the standard test point.) The test software eliminates the task of manual oscilloscope set-ups, cursor placement and comparison of test results with USB 2.0 specifications. The results are automatically displayed as a results summary with details, as illustrated in Figure 2.
USB 2.0 Electrical Tests
USB 2.0 electrical tests involve the following procedures and measurements:
LOW SPEED | FULL SPEED | HIGH SPEED | |
Signal Quality | X | X | X |
Inrush Current | X | X | X |
Drop | X | X | X |
Droop | X | X | X |
Receiver Sensitivity | X | ||
Chirp | X | ||
Monotonicity | X |
As shown in the table, the required tests vary depending upon the speed. Test requirements may also vary by the specific device under test. Each of the tests are described in more detail in the following sections.
SIGNAL QUALITY TEST
Maintenance of signal quality is one of the keys to ensure that a USB 2.0 device is compliant and will be awarded the USB 2.0 certified logo. Signal quality tests evaluate jitter and eye diagram measurements to determine the dynamic characteristics of the differential data lines.
The signal quality test includes:
- Eye Diagram testing
- Signal rate
- End of Packet (EOP) width
- Cross-over voltage range
- Paired JK Jitter
- Paired KJ Jitter
- Consecutive jitter
- Rise time
- Fall time
Along with the USBET eye-diagram test, the TekExpress package provides an additional eye-diagram plot with zoom and cursor facilities which can be used to get deeper insight into the eye profile.
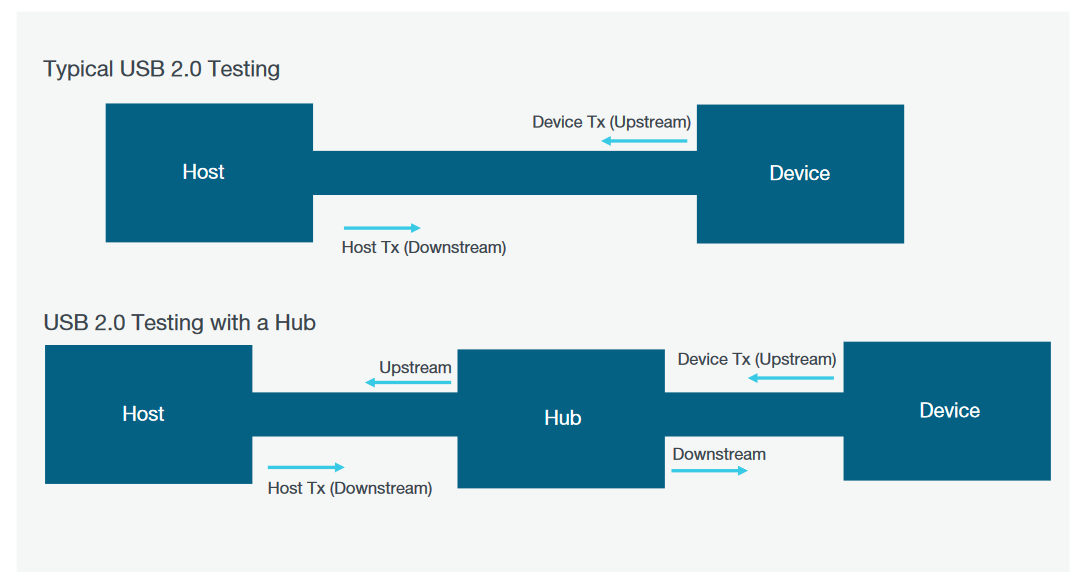
The test set-ups for signal quality testing vary for upstream and downstream testing. In the case of upstream testing, signals transmitted from the device to the host are captured, whereas in the case of downstream testing, signals transmitted from the host are captured for testing. Downstream testing is usually performed on ports of a hub.
Test Equipment
Signal quality testing requires:
- A real-time oscilloscope with a bandwidth of 2 GHz or higher for high speed USB signals, or an oscilloscope with a bandwidth of 350 MHz or higher for low and full speed USB signals.
- Single-ended probes like the TAP1500, TAP2500, TAP3500, and P6245*1 for low and full speed USB testing. Differential probes such as the TDP1500, TDP3500, and P6248*1 for high speed USB testing.
- Testing software (option 5-CMUSB2 compliance test package and USB-IF USBET)
- USB2SIGQUAL test fixture from USB-IF or TDSUSBF from Tektronix
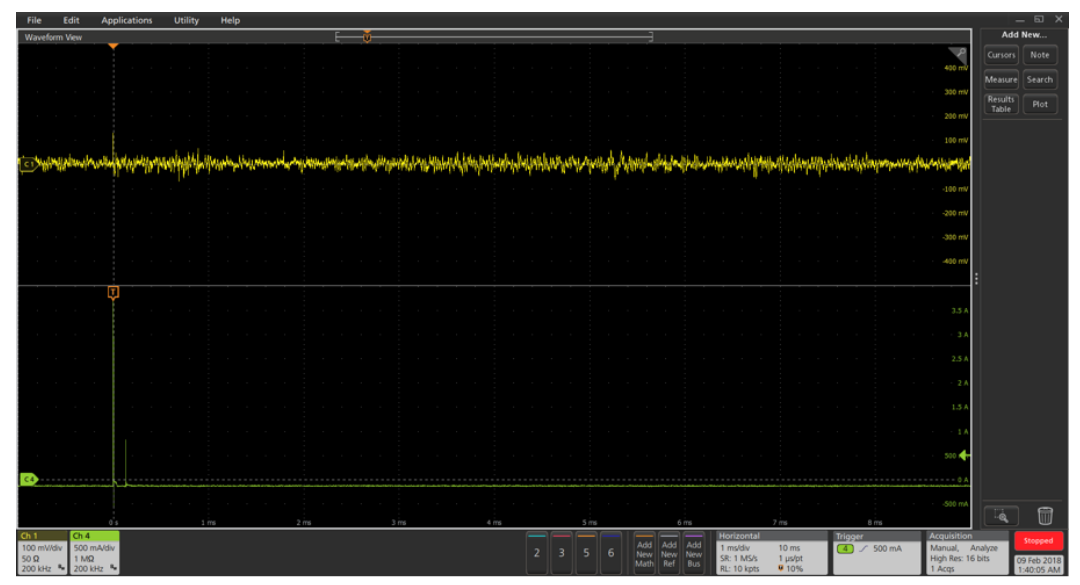
INRUSH CURRENT CHECK
Because USB 2.0 is a hot-pluggable technology, extreme care is required to ensure that the current drawn by a device does not exceed a specified limit. If the current drawn exceeds a specified value,the operation of other USB 2.0 devices connected to the bus may be impaired. The in-rush current check is performed for both self-powered and bus-powered devices to verify that the device-undertest (DUT) does not draw too much current when plugged into the port of a hub.
Typically, one expects a sharp intake of current when a device is plugged in. One may also observe small perturbations in the current trace when the device is reset. Mathematically, an in-rush current check involves the calculation of the integral of current over a certain period of time.
The USB 2.0 specification dictates that the total charge drawn by the device should be less than or equal to 52.5 uC for a VBUS value of 5.15 V. (The waiver limit for this test is less than 150 uC).

Test Equipment
The inrush current test requires
- Real-time oscilloscope
- Current probes, such as the TCP0030A.
- Test fixture TDSUSBF from Tektronix
The TekExpress USB2 test package can be used to automatically set up the oscilloscope for the inrush current check. This test package provides direct readout of Charge (uC) and an automatic indication of pass or fail.
DROP TEST
The USB 2.0 specification requires powered USB hub ports to provide a VBUS between 4.75 V and 5.25 V while bus-powered hubs maintain a VBUS at 4.4 V or greater. Drop testing evaluates VBUS under both no-load and full-load (100 mA or 500 mA, as appropriate) conditions.
Vdrop = Vupstream — Vdownstream
Vupstream = VBUS at the hub's upstream connection
Vdownstream = VBUS at one of the hub's downstream ports
Bus-powered hubs must have a Vdrop < =100 mV between their downstream and upstream ports when 100 mA loads are present on any downstream ports. The 4.75 V requirement for powered hubs ensures that the hubs will supply 4.4 V to a downstream device, allowing for 0.25 V cable drop and 0.1 V drop in the hub. Bus-powered devices with captive cables must have Vdrop <= 350 mV between the upstream connector and downstream port, including the drop through the cable.
Test Equipment
Drop tests require a multimeter. Since this is a DC test, and a digital multimeter with millivolt resolution can be used to confirm compliance.
DROOP TEST
Vdroop equals the difference in the VBUS voltage under no-load condition and when a 100 mA load is applied to the portunder-test (PUT) with all other ports fully loaded. The USB 2.0 specification allows a maximum droop of 330 mV. The droop test evaluates worst-case droop by alternately applying a 100 mA load and no-load condition to the port under test while all other ports are supplying maximum load. All VBUS measurements are relative to local ground.
Test Equipment
Droop tests require
- Real-time oscilloscope
- Single-ended active probe such as TAP1500, P6243*2 or P6245*2
- Test software (option 5-CMUSB2 compliance test package)
- USB2/3_DD USB-IF test fixture from USB-IF or TDSUSBF from Tektronix
This test is relatively easy to perform manually. However, the test package automatically sets up the oscilloscope for the desired test configuration, acquires the signal, provides the Vdroop measurement, and provides a pass or fail indication.
2 Requires a TPA-BNC adapter when used on a 5 Series MSO, MSO/DPO5000 or DPO7000 Series model.
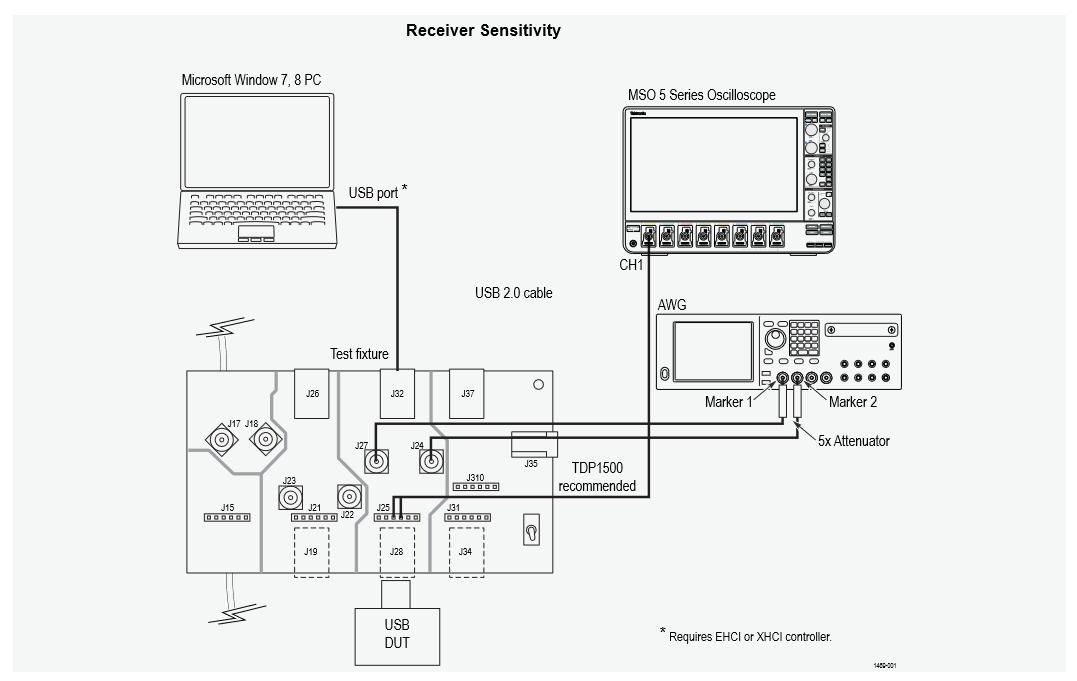
RECEIVER SENSITIVITY TEST
To promote robust operation in noisy environments, a high speed USB 2.0 high-speed device (or downstream port) must respond to IN tokens (transmitted data) with NAKs when the signal level equals or exceeds the specified level. (A detailed description of this process is covered in the USB 2.0 specifications.) The test requires placement of the DUT in Test_SE0_NAK mode. The host is then replaced by a signal generator which continues to transmit IN tokens. The signal amplitude is presented to the DUT at a level at or above 150 mV. At these levels, the DUT must be in the unsquelched mode, responding to IN packets with NAKs. The amplitude is then reduced to <100 mV and at this level, the DUT must be squelched and does not respond to IN tokens with NAKs.
Test Equipment
The receiver sensitivity test requires
- 2 GHz real-time oscilloscope or higher
- High speed data source that can transmit IN tokens of varying amplitude,(such as Tektronix AWG5000C or AWG7000C Series Arbitrary Waveform Generators)
- Differential probes (e.g. TDP1500, TDP3500, or P6248*3)
- Test software
- TDSUSBF test fixture
Figure 6 shows the set-up to perform this test using an oscilloscope and data generator. The option 5-CMUSB2 test package provides automated set-ups and the test patterns for the signal source, needed for receiver sensitivity testing.
3 Requires a TPA-BNC adapter when used on an MSO/DPO5000 or DPO7000 Series model.
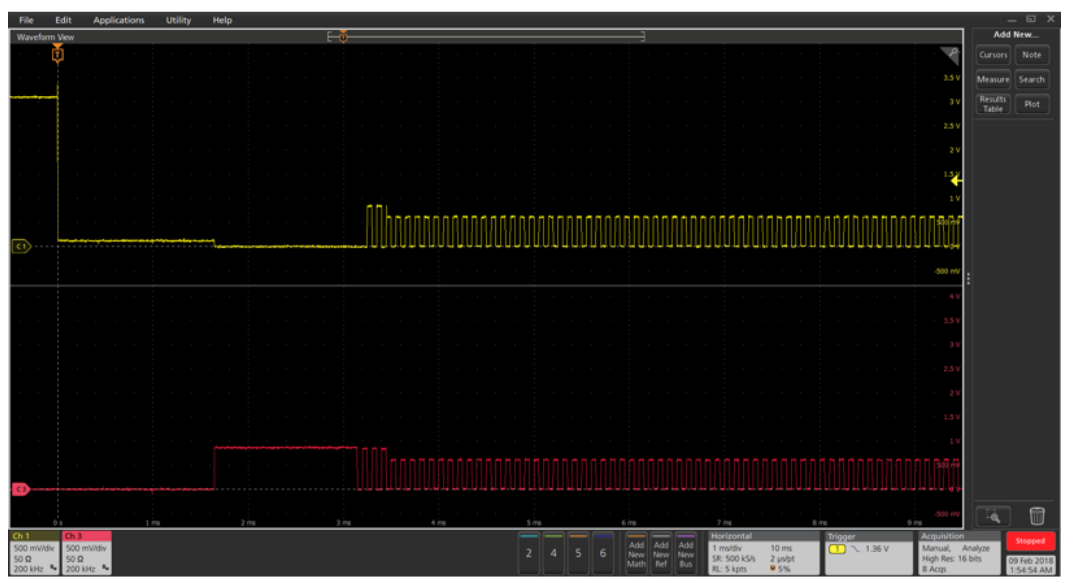
CHIRP TEST
The chirp test examines the basic timing and voltages of both upstream and downstream ports during the speed detection protocol. For a hub, the chirp test must be performed on both upstream and downstream ports.
To perform chirp testing, the DUT is hot-plugged and signaling is measured with singleended probes on both data lines. Data is analyzed for chirp K amplitude, chirp K duration, Reset duration, Number of KJ pairs before High Speed termination and delay after KJKJKJ before device-applied termination. Figure 7 illustrates the chirp test.
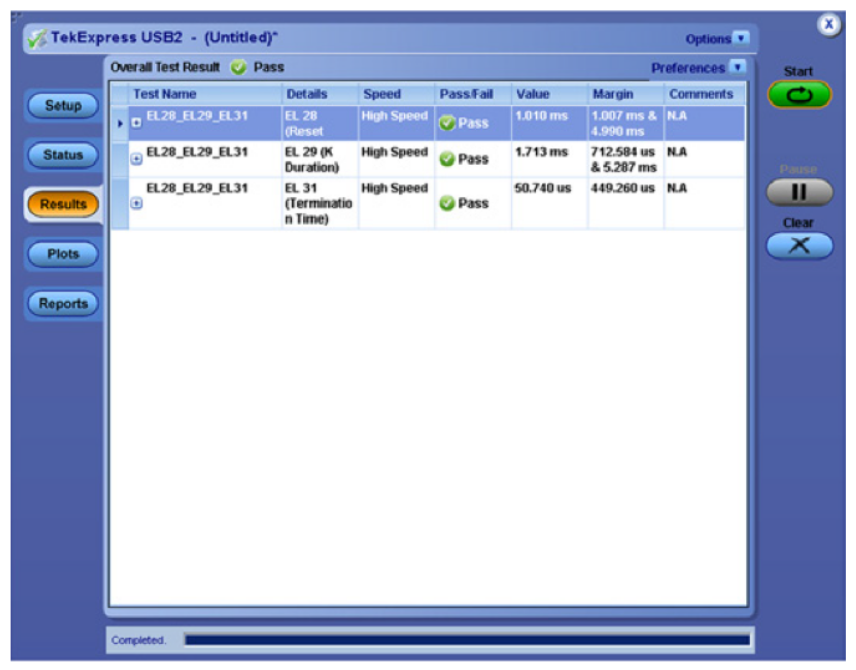
Test Equipment
The chirp test requires:
- A real-time oscilloscope with a bandwidth of 2 GHz or higher
- Single-ended probes such as TAP1500, TAP2500, TAP3500, P6243*3 or P6245*3
- Test software (option 5-CMUS2 compliance test package.)
- Signal quality test fixture (Tektronix TDSUSBF)
Manual analysis of the various chirp types and conditions is a time-consuming process. The 5-CMUS2 test package automates this process and automatically documents the results.
Requires a TPA-BNC adapter when used on an MSO/DPO5000 or DPO7000 Series model.
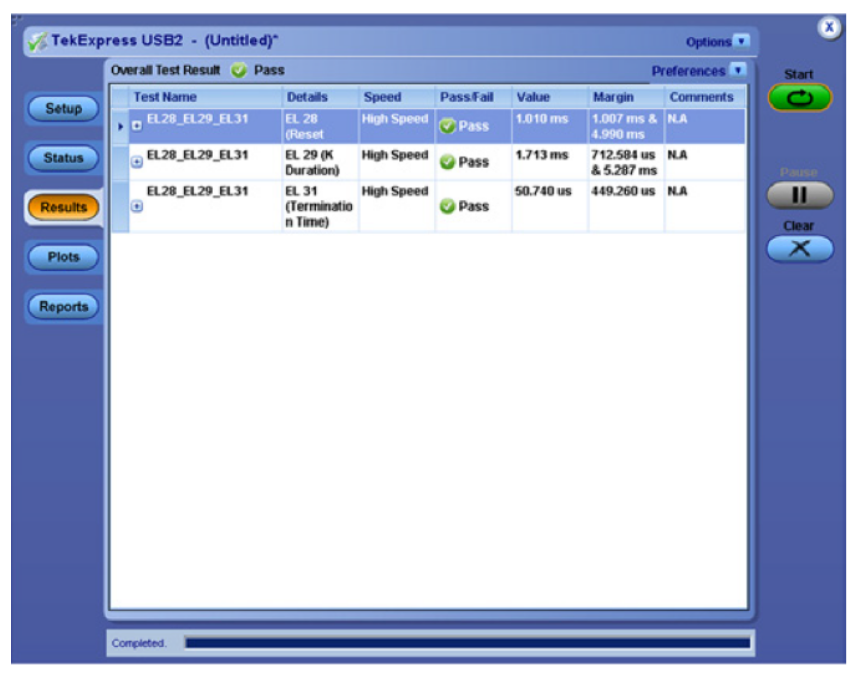
MONOTONICITY TEST
For USB 2.0 high-speed compliance, a developer needs to verify that the signal is monotonic. Monotonicity verifies that a transmitted signal smoothly increases or decreases in amplitude without deviation in the opposite direction. A non-monotonic signal behavior may be caused by metastability, high-frequency noise, or jitter. Figure 10 compares a monotonic signal with a non-monotonic signal using a USB 2.0 highspeed signal with a rise time of 500 ps.
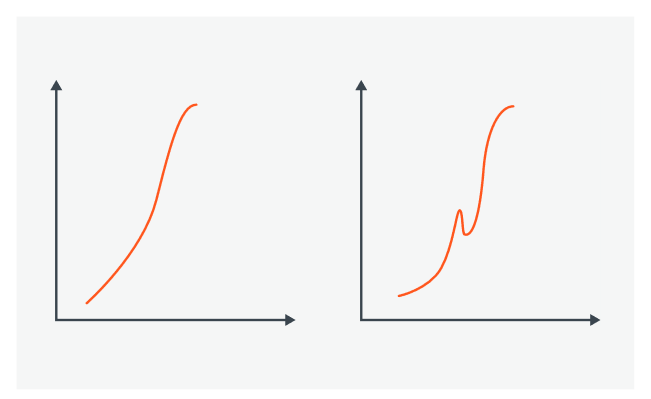
Test Equipment
The monotonicity test requires
- A real-time oscilloscope with a bandwidth of 2 GHz or higher. Sample rate should be high enough to capture as many sample points as possible on a rising or falling edge. In addition, the oscilloscope should have enough bandwidth to ensure that the high frequency non-monotonic transition is not attenuated. Hence, an oscilloscope with a sample rate of 6.25 GS/s and a recommended bandwidth of 2 GHz is ideal for monotonicity testing.
- Single-ended probes such as TAP1500, TAP2500, TAP3500, P6243*3 or P6245*3
- Test software (option 5-CMUS2 compliance test package.)
- Signal quality test fixture (Tektronix TDSUSBF)
The monotonicity test for a USB 2.0 device is verified during test packet examination. The option 5-CMUSB2 compliance test package automatically captures the test packet, examines and reports each rising and falling edge for monotonic behavior, as shown in Figure 9. The setup uses the highspeed signal quality test configuration, as illustrated in Figure 11.
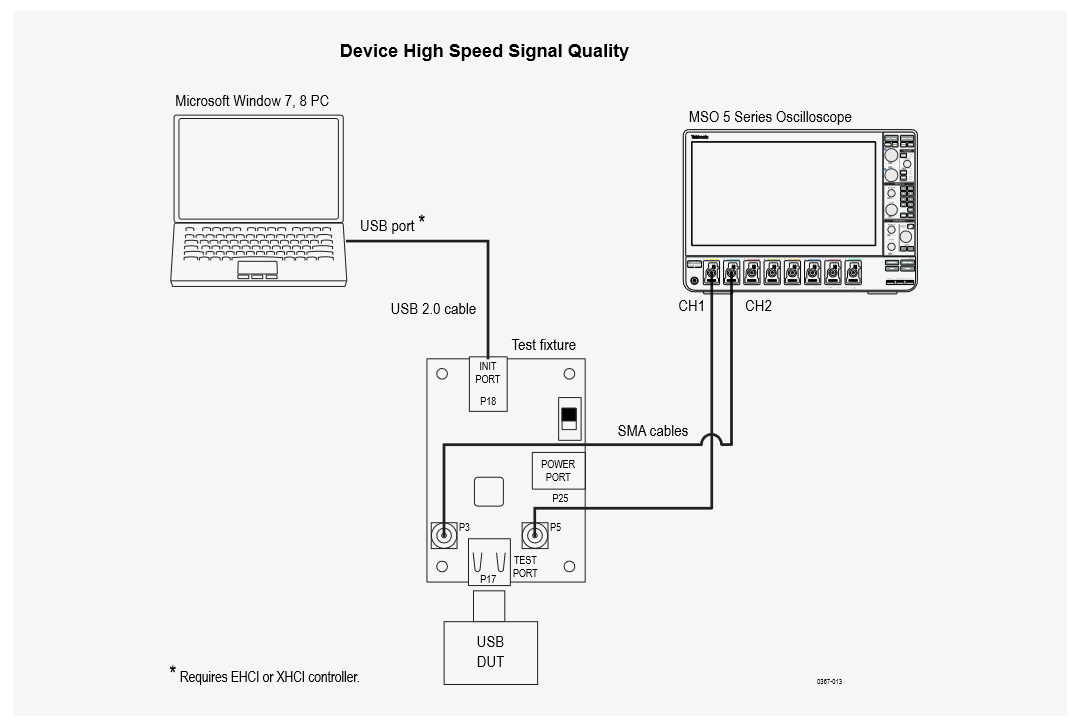
TEST EQUIPMENT | SIGNAL QUALITY | INRUSH CURRENT | DROP | DROOP | RECEIVER SENSITIVITY | CHIRP | MONOTONICITY |
Real-time Oscilloscope | X | X | X | X | X | X | |
Signal Generator | X | ||||||
Digital Multimeter | X | ||||||
Test Fixture | X | X | X | X | X | X | |
Test Software | X | X | X | X | X | X | |
Differential Probes | X | X | X | ||||
Single-ended Probes | X | X | X | ||||
Current Probe | X |
FIGURE 12. Note: All Non-signal quality tests can be performed by Tek fixture.
Instrumentation Requirements for USB 2.0 Physical Layer Testing
USB 2.0 physical layer validation and electrical compliance testing requires a variety of test equipment,as illustrated in the chart above.
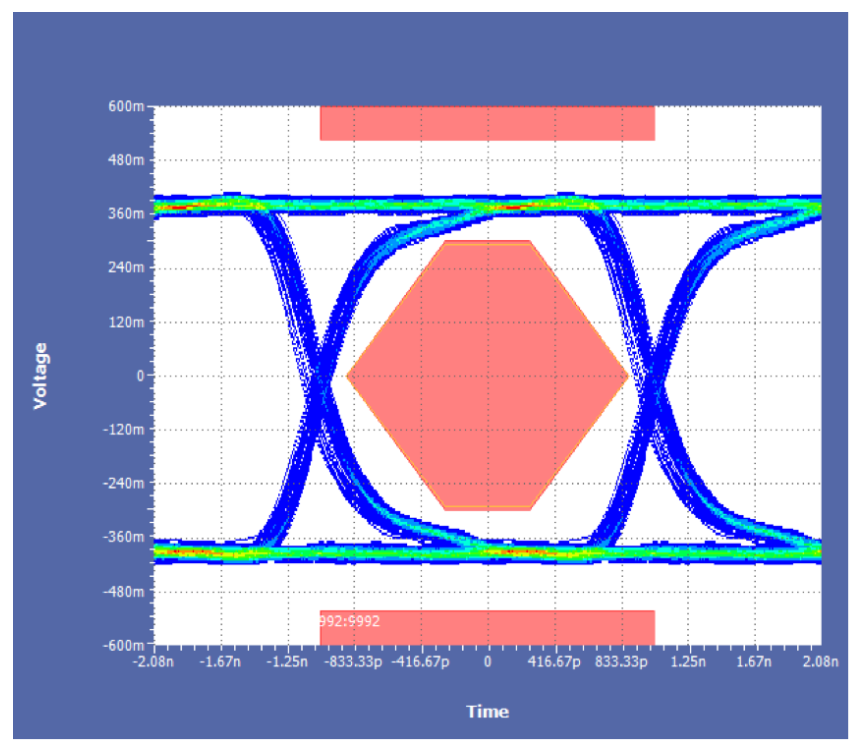
Real-time Oscilloscope
A real-time oscilloscope is the most crucial test instrument for USB 2.0 measurements. When selecting an oscilloscope for these measurements, it is important to consider the oscilloscopes’ rise time, bandwidth and sample rate.
EFFECT OF OSCILLOSCOPE BANDWIDTH/RISE TIME ON MEASUREMENT ACCURACY
Rise time requirements for the oscilloscope depend on the rise time or slew rate of the signals to be measured. The following empirical formula gives the relationship between measured rise time [RT(measured)], oscilloscope rise time [RT(oscilloscope)] and signal rise time [RT(signal)];

Typical edge rates of USB 2.0 silicon are in the 300 to 500 ps range and an oscilloscope with rise time performance faster than this is recommended. To measure a signal with a rise time of a typical USB 2.0 signal with less than 10-15% error, the oscilloscope used should ideally have a rise time of 100- 225 ps.
EFFECT OF OSCILLOSCOPE SAMPLE RATE ON TESTING
To capture information at edge speeds as fast as 300 to 500 ps, you need at least 5 to 10 sample points on an edge. This requirement becomes even more important when performing a monotonicity test, mandatory for highspeed testing.
Tektronix Real-time Oscilloscopes
The following chart lists various Tektronix real-time oscilloscopes along with their rise/fall time and sample rate specification.
SPECIFICATION | 5 SERIES MSO | MSO/DPO5204 | DPO7254C | DPO7354C | DPO70404C |
Rise/Fall Time | 225 ps | 175 ps | 160 ps | 115 ps | 98 ps |
Sample Rate (1 ch) | 25 GS/s | 10 GS/s | 40 GS/s | 40 GS/s | 25 GS/s |
Note: USB 2.0 can encounter edge rates as fast as 300 ps.

SIGNAL SOURCE
A signal source is required for the receiver sensitivity test. The Tektronix AWG5000 Series and AWG70000 Series are excellent signal sources for USB receiver sensitivity tests. The setup files required to perform USB 2.0 receiver sensitivity tests for these signal sources are available from Tektronix.
TEST FIXTURES
Test fixtures provide signal routing and access to the appropriate signals for each test, including the differential data lines (D+, D-) and VBUS.
For receiver sensitivity testing, SMA cables are needed to connect the signal source to data lines to stimulate the device.
For High-speed Signal Quality measurements and certification at USB test events, the USBSIGQUAL fixture set from USB-If is required, as shown in Figure 15. These fixtures are specifically designed for testing requirements, and the only fixture allowed for compliance certification, but they do not provide access for probing. Thus, they are not well-suited for troubleshooting.
The TDSUSBF fixture, from Tektronix is a comprehensive test fixture set,shown in Figure 16. It provides a signal quality fixture that provides probing access, which is helpful for troubleshooting. It also includes fixtures for inrush testing with current probe access, and droop/drop testing.
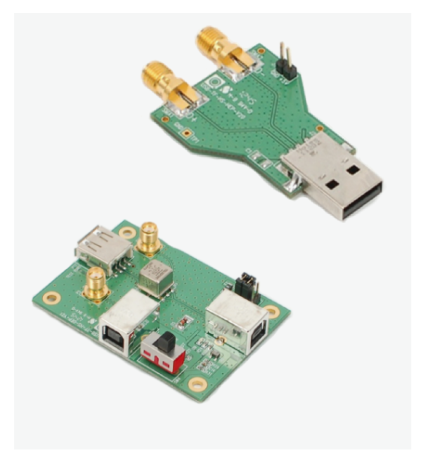
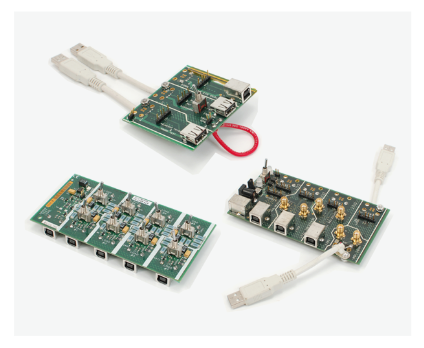
TEST SOFTWARE
There are two software tools available from USB-IF for USB 2.0 compliance testing. USBHSETT and USBET.
Compliance testing must be performed using USBET. The USBHSETT tool from the USB-IF is installed on a separate Windows PC and sets up the DUT into specific test modes so the signals can be acquired on the scope. However, this software does not control any test instruments.
5 SERIES MSO | MSO/DPO5XXX SERIES | DPO7000C SERIES | MSO/DPO70000C SERIES | |
Automated USB 2.0 Compliance Software | 5-CMUSB2 | USB2 | USB2 | USB2 |
Note: USB 2.0 can encounter edge rates as fast as 300 ps.
Automated test software, such as the Option 5-CMUSB2 or Option USB2 compliance test packages, substantially improves test efficiency by automating oscilloscope and generator set-ups, acquisitions, pass/fail evaluation, margin analysis, and reporting. Automation dramatically reduces test times and improves repeatability
PROBES
Probes are a critical component of the measurement system to tap the signals into an oscilloscope.For USB 2.0 testing, Tektronix offers differential (P6248*4, TDP1500, TDP3500), single-ended (P6245*4,TAP1500, TAP2500, TAP3500) and current (TCP202A*4, TCP0030A) probes that allow access to highdensity boards with fine-pitch, hard-to-reach components while maintaining maximum signal fidelity
TIME DOMAIN REFLECTOMETER
Because of the data rates of USB 2.0 High-Speed mode, impedance matching becomes critical. In some situations, you may need to measure trace, packaging, cable or connector impedances. If testing is required these impedances can be measured using a time domain reflectometer (TDR), such as the DSA8300 sampling oscilloscope with 80E04 TDR sampling module and IConnect analysis software.
4 Requires a TPA-BNC adapter when used on a 5-series MSO, MSO/DPO5000 or DPO7000 Series model.
Conclusion
USB 2.0 is widely used in embedded systems and peripherals. Its data rates, robustness, and cost effectiveness make it suitable for many applications. Tektronix offers comprehensive tool sets — sophisticated mixed-signal oscilloscopes, high-speed signal generators, industry-leading probes, USB 2.0 triggering and analysis applications, and a fully automated compliance test packages -- to enable USB 2.0 device designers to perform quick and accurate electrical compliance testing.
Tektronix maintains a complete library of updated resources for the USB device designer at www.tektronix.com/usb.