Свяжитесь с нами
Живой чат с представителями Tektronix. С 9:00 до 17:00 CET
Позвоните нам
С 9:00 до 17:00 CET
Загрузить
Загрузить руководства, технические описания, программное обеспечение и т. д.:
Обратная связь
Electric Vehicle Battery Testing – A New World of Challenges
Electric vehicle battery cell, module, and pack production systems rely on precision electrical instruments to reliably identify variation. Manufacturers depend on affordable test equipment to:
- Consistently detect tiny electrical anomalies
- Integrate into complex and diverse automated systems
- Adapt as testing requirements evolve
- Deliver zero downtime
Test engineers are working closely with R&D engineers to bring new battery technologies to reality. And engineers trust Keithley electric vehicle testing equipment to help them to push the boundaries.
Learn how to:
- Efficiently work with full battery systems
- Save test power and return it to the grid
- Optimize battery reprocessing and recycling
- Battery Grading with Open Circuit Voltage Testing
- Battery Tab and Busbar Weld Checking with Resistance Measurements
- Environmental and Safety Testing using Temperature Datalogging
- Quantifying Battery Self-Discharge with Open Circuit Voltage Testing
- Formation, Aging and Battery Cycling
- Ensuring Battery Quality with DC Internal Resistance
- Check Electrode Contact Quality with Low Resistance Measurements
- Keep Batteries Isolated by Measuring Insulation Resistance
EV Battery Technology and Critical Production Tests
Efficiently Work with Full Battery Systems
Battery technology is becoming increasingly sophisticated, as batteries get smaller and become increasingly efficient. To keep up with these changes in battery technology, your battery test equipment must also be advanced, flexible and responsive.
The EA 10000 Series bidirectional supplies can seamlessly switch between charging batteries under test and discharging them in a controlled manner. Battery charge, static discharge and dynamic test functions are included with Bidirectional Power Supply (PSB), Power Supply (PSI), and Regenerative Electronic Load (ELR) product series, or you can program the PSB to perform custom charge and discharge cycles if you have special requirements. In either case, EA supplies can help build a robust system that will effectively and safely test your product’s batteries.
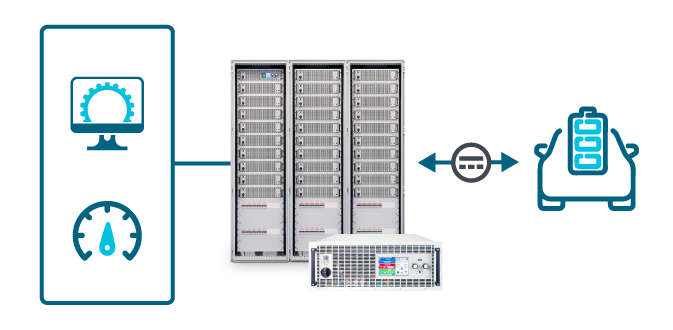
Bidirectional power supplies can be made into modular rack systems for testing battery systems up to 3.84MW.
Learn More:

EA Elektro-Automatik regenerative loads facilitate sinking DC power and returning it to the grid to be used again.
Learn More:
EA ELR Series Regenerative Electronic Loads Overview
EA-10000 Series Bidirectional Regenerative DC Power Supplies and Loads
Save Test Power and Return it to the Grid
Testing of battery packs requires something to be done with the power coming out of them. Traditionally, this power would be sunk using resistive loads that turn all the power into heat, or sunk using traditional electronic loads, that also turn the sunk power into heat.
Bidirectional power supplies and regenerative electronic loads from EA Elektro-Automatik can recover sunk energy at up to 96% efficiency. In an industrial setting, this recovery efficiency results in huge cost savings compared to using resistive loads. For example, assuming an average kilowatt-hour price of $0.10 and a monthly usage of 48,000 kWh, recovering 96% of sunk energy from battery testing could result in >$55,000 in energy savings, without accounting for savings in cooling and ventilation costs.
Optimize Battery Reprocessing and Recycling
To make electromobility sustainable, second-life concepts and efficient recycling of lithium-ion batteries and lithium-ion polymer batteries will play a key role. The potential uses of second-life batteries from electric vehicles range from home storage, emergency power supplies and power buffers, to energy storage for solar power or wind energy. After the second-life cycle, the rechargeable batteries are subjected to final recycling. Before the batteries are disassembled into their individual parts, they must be fully discharged to avoid the risk of contact-hazardous voltage or fire and to use the residual energy still stored in the battery.
Bidirectional power supplies like the EA-BT 20000 Series are ideal for reprocessing for second-life applications, where batteries must be cycled multiple times to determine capacity (SOC), state of aging (SOH), and other parameters needed to determine a fitting second application. In recycling, Regenerative electronic loads like the EA 10000 Series are used to safely capture as much residual energy as possible. Both of these supplies recovery energy and return it to the grid with an efficiency of up to 96%.
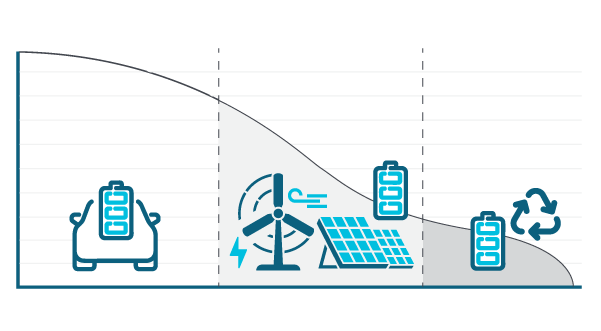
Batteries lose their capacity gradually over time. Less demanding applications like energy storage can re-use batteries after they've been used in something like an EV.
Learn More:
EA PSB Bidirectional Power Supply – Enabling EV Battery Recycling

Measuring open circuit voltage on a battery cell.
Learn More:
Measuring Battery Cell Open Circuit Voltage with the Keithley DMM7510 Digital Multimeter
Measuring the Open Circuit Voltage of a Battery Cell with a Keithley DMM7510
Battery Grading with Open Circuit Voltage Testing (OCV)
Battery grading is a critical step in any battery production environment where battery performance is key. Open circuit voltage (OCV) measurements are used to bin the batteries into the following grades:
- Grade A batteries have the longest lifespans, lower internal impedance and better overall performance. Used in high power applications like electric vehicles.
- Grade B batteries have lesser performance and shorter lifespans. Used for energy storage applications
- Grade C batteries are the lowest performing. Used for single cell portable applications
Manufacturers need to separate the highest quality batteries from the batteries that may have internal defects such as microshorts or contaminants. The OCV of the battery can be monitored over time to observe discharge trends and characterize performance. This process can take weeks to observe changes in the OCV in tens to hundreds of microvolts.
Keithley’s DMM7510 is a perfect solution for OCV testing in the production environment. Its 7.5 digit measurement resolution and superior accuracy means measuring smaller changes in voltage and getting results sooner. For higher volume applications, the Keithley 3706A System Switch and Multimeter allows for up to 576 two-wire channels in one mainframe, expanding your testing capabilities without sacrificing test rack or bench space.
Battery Tab and Busbar Weld Checking with Resistance Measurements
Welding is common practice in automated production systems to connect the cell tabs to the electrodes as well as connecting completed cells together to form a battery pack. Large battery packs can have tens to hundreds of welds, or joints, connecting cells to busbars.
A good quality weld joint contributes little resistance to the circuit, typically only microohms. Bad welds or joints can measure in the milliohm range which leads to performance issues and excess heat generation that can cause a severe thermal runaway event. It is nearly impossible to visually identify a bad weld.
However, weld imperfections can be quickly identified in a production environment with a resistance measurement using a precision DMM such as the Keithley 3706A System Switch and Multimeter and a current source such as a Keithley 2460 SMU. The SMU can provide precision current up to 7 A while the DMM measures the resistance of the joint down to microohms. The high density built in switching in the 3706A enables more weld checks with less rewiring.
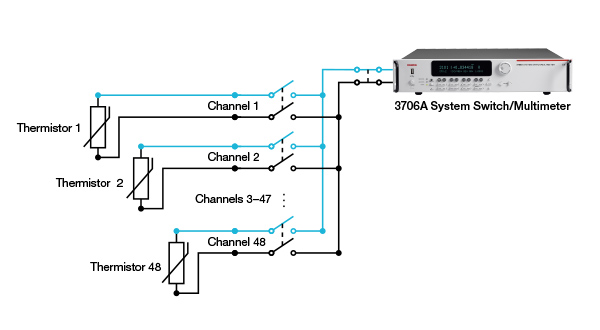
Multipoint temperature measurements made with a multichannel DMM like the 3706A.
Learn More:
Monitoring Battery Cell Temperature with a Keithley 3706A System Switch and Multimeter
Environmental and Safety Testing using Temperature Datalogging
Environmental testing is extremely important to ensure batteries will withstand and perform under extreme environmental conditions. Thermal testing is also an important part of safety qualifications. Although temperature testing varies widely depending on the test sequence, battery type, and physical constraints, common temperature measurements on a battery include:
- Internal temperature of a cell or module using an embedded sensor
- External temperature of a cell or module
- Monitoring the ambient temperature around the pack to understand heat dissipation or to verify the environmental conditions.
Because battery performance is temperature dependent, engineers measure, document, and in some cases characterize and program the batteries into the EV when installed. Temperature is also an indicator of cell failure and thermal runaway.
The Keithley 3706A System Switch and Multimeter is a high density switching system with up to 576 2-wire channels per mainframe. The customizable switching configuration can be configured for density for more monitoring points or for speed for quick temperature checks.
Quantifying Battery Self-Discharge with Open Circuit Voltage Testing (OCV)
Batteries tend to discharge over time when they are not connected, as the chemical reaction slowly reverses itself internally. Ideally, this internal self-discharging current is extremely small so the battery can hold a charge longer. Batteries with internal defects such as microshorts, pinholes in the separator and contaminants, discharge faster over time than their higher quality counterparts.
This could cause poor performance and balancing issues in a pack or cause the cell to be stressed. The open circuit voltage (OCV) of the battery can be used to monitor the self-discharge behavior as the open circuit voltage decreases when the battery discharges. Separating the good batteries from the defective batteries before they are placed in a pack can require weeks of monitoring as OCV changes may only be tens to hundreds of microvolts.
Keithley’s DMM7510 is a perfect solution for OCV monitoring to measure self-discharge. The 7.5 digit resolution and superior accuracy means measuring smaller changes in voltage and viewing trends sooner. For higher volume applications, the Keithley 3706A System Switch and Multimeter allows for up to 576 two-wire channels in one mainframe, expanding your testing capabilities without sacrificing test rack or bench space.
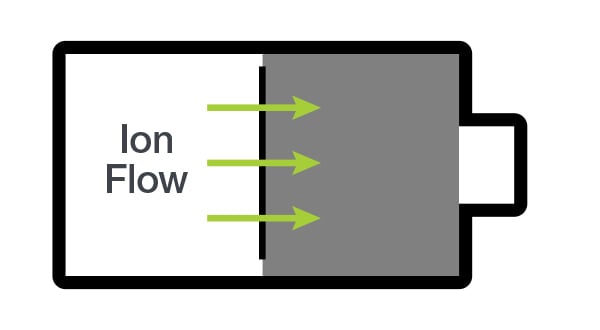
Self-discharge means ions flow internally even when the battery is disconnected.
Formation, Aging and Battery Cycling
The most important part in the battery cell manufacturing process is the formation and aging stage, where critical chemistry mechanisms are established in the battery. The results of this process directly affect the battery’s performance later in life and post-formation testing is conducted to identify batteries that failed to form correctly.
Formation and aging require the battery to be repeatedly charged and discharged at varying rates. Cycling the batteries is a crucial component in many other tests, including modeling and thermal characterization.
Test procedures vary widely depending on battery chemistry, construction and the test profiles. And many other tests require the batteries to be cycled, so test solutions must be flexible.
Keithley source measure units or SMUs provide a convenient single box solution for charging and discharging. The 2400 Series Graphical Touchscreen SMUs can accurately source currents up to 7 A DC. These SMUs offer TSP® Scripting Technology to make production automation simple and efficient.
Ensuring Battery Quality with DC Internal Resistance
Batteries with high internal resistance have lower performance and higher risk of failures like thermal runaway. Internal resistance is an indicator of an incorrectly formed solid electrolyte interphase (SEI) layer and may also be used as a metric for battery quality.
Keithley source measure units (SMUs) provide a single box solution for DC internal resistance testing. The 2400 Series Graphical Touchscreen SMUs can source an accurate low current and measure the corresponding voltage to calculate the internal resistance.
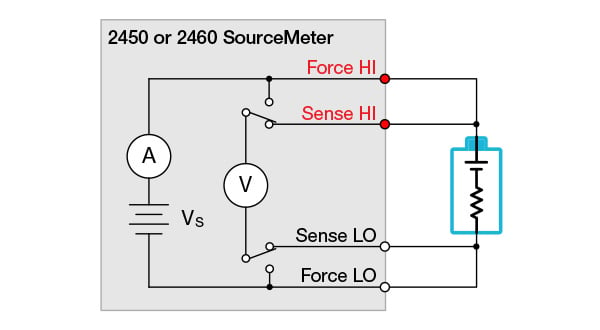
Meauring the DC internal resistance of a battery cell using an SMU.
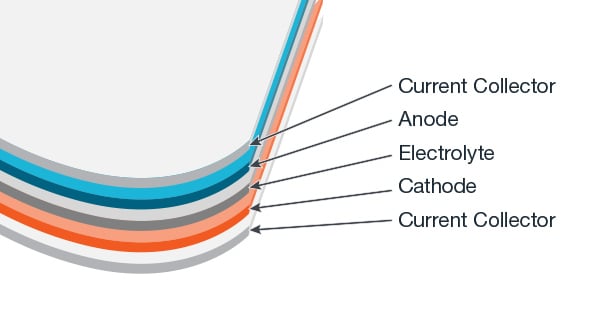
Layers in a battery cell. Contact resistance is measured between the electrode material and the current collector.
Check Electrode Contact Quality with Low Resistance Measurements
Poor connection between the current collector and the electrode material that is rolled onto the collector increases the internal resistance of the battery. Identifying poor electrodes early on saves time and resources later in the manufacturing process.
The Keithley 6200 Series Sensitive Current Sources paired with the 2182A Nanovoltmeter makes the perfect combination for sensitive low resistance measurements on electrodes. This low resistance combination measures as low as tens of nano-ohms for the best confidence in the quality of the electrode.
Keep Batteries Isolated by Measuring Insulation Resistance
Shorted batteries means risk of dangerous failures. Shorts can occur internally, but there is also risk of external shorts when insulation fails, or a battery is incorrectly connected to the pack. Verifying the isolation of the cell electrodes from ground and the insulation quality of any materials exposed to current can prevent a serious failure later.
The Keithley 2470 High Voltage Source Measure Unit (SMU) provides a simple, single-box solution to measure the resistance of materials. The SMU can source voltage up to 1 kV and calculate the corresponding resistance of the material.
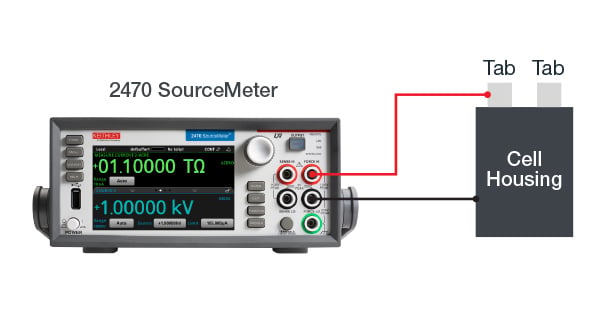
Measuring the insulation resistance. The tab of the battery should be electrically isolated from the chassis.
Electric Vehicle Battery Testing Equipment
Frequently Asked Questions
What is EV battery testing?
EV battery testing encompasses many methods to verify a battery’s performance and safety. Testing occurs at all stages of the battery lifecycle, from the design labs to the manufacturing floor to the final end user.
How are Electric Vehicle batteries tested?
EV Batteries undergo a wide variety of tests including chemical, mechanical, thermal and electrical testing. Electrical testing includes measuring battery voltage, internal impedance, resistance of components and charge/discharge profiles. Electrical test equipment can be measurement-only like a DMM or require accurate sourcing and measurement in the form of power supplies and source measure units (SMUs).
What is the standard for EV battery testing?
There are many standards available for EV battery testing. Standards encompass safety and performance for batteries starting at the cell level, all the way to the pack level. Standards are also dependent on end use application. For example, standards for consumer electric vehicles may differ from standards for industrial electrical vehicles or small transportation such as E-bikes and E-scooters.
Why is EV battery testing important?
Thorough testing ensures that the batteries are not only safe, but meet the performance specifications set by the manufacturer. Low quality batteries can have compounding effects on the whole pack, so it’s crucial to identify those batteries before they make it to the end user. Testing in the research and development phase is also key to validating new and improved designs.
What are the requirements for EV batteries?
Battery specifications can be complex, with ratings on voltage, current, impedance, capacity and lifespan. Ratings vary depending on the battery chemistry and construction. Electrical testing is necessary to verify these ratings for the end user.