Programmable DC Power Supplies
DC power supplies provide a regulated DC output to power a component, a module, or a device. A power supply must deliver voltage and current that is stable and precise, with minimal noise to any type of load: resistive, inductive, low impedance, high impedance, steady-state, or variable. How well the power supply fulfills this mission and where it reaches its limits are defined in its specifications.
Power supplies have two main settings, the output voltage and the current limit. How they are set in combination with the load determines how the power supply will operate.
Most DC power supplies have two modes of operation. In Constant Voltage (CV) mode, the power supply controls the output voltage based on the user settings. In Constant Current (CC) mode, the power supply regulates the current. Whether the power supply is in CV or CC mode depends on both the user settings and the resistance of the load.
- CV mode is the typical operating state of a power supply. It controls voltage. The output voltage is constant and is determined by the user’s voltage setting. The output current is determined by the impedance of the load.
- CC mode is typically considered a safety mode, but can be used in other ways. In CC mode, the output current is constant and is determined by the user’s current limit setting. The voltage is determined by the impedance of the load. If the power supply is in CV mode and its current exceeds the user’s current limit setting, then the power supply will automatically switch to CC mode. The power supply can also revert back to CV mode if the load current falls below the current limit setting.
The most important parameters for any application are the maximum voltage, maximum current, and maximum power that the power supply can generate. It is essential to ensure that the power supply can deliver the power at the required voltage and current levels. These three parameters are the first specifications that must be investigated.
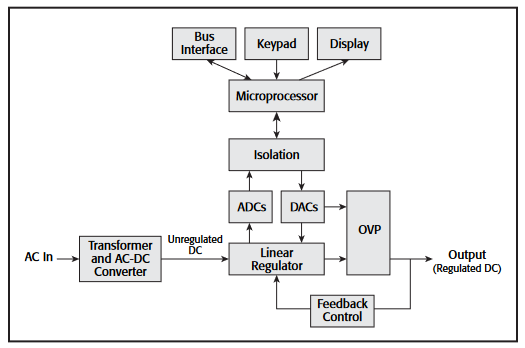
Accuracy and Resolution
Historically, the DC power supply user turned potentiometers to set output voltage or current. Today, microprocessors receive input from the user interface or from a remote interface. A digital-to-analog converter (DAC) takes the digital setting and translates this into an analog value, which is used as the reference for the analog regulator. The setting resolution and accuracy values are determined by the quality of this conversion and regulation process.
Voltage and current settings (sometimes called limits or programmed values) each have resolution and accuracy specifications associated with them. The resolution of these settings determines the minimum increment in which the output can be adjusted, and the accuracy describes the extent to which the value of the output matches international standards. In addition to output settings, there are measurement or readback specifications that are independent of the output specifications.
Most programmable DC power supplies provide built-in measurement circuits for measuring both voltage and current. These circuits measure the voltage and current being delivered by the power supply output. Since the circuits read the voltage and current that is fed back into the power supply, the measurements produced by the circuits are often called readback values. Most professional power supplies incorporate circuits that use analog-to-digital converters, and for these internal instruments the specifications are similar to those of a digital multimeter. The power supply displays measured values on its front panel and can also transmit them over its remote interface, if it is equipped with one.
Setting Accuracy
Setting accuracy determines how close the regulated parameter is to its theoretical value as defined by an international standard. Output uncertainty in a power supply is largely due to error terms in the DAC, including quantization error. Setting accuracy is tested by measuring the regulated variable with a traceable, precision measurement system connected to the output of the power supply. Setting accuracy is given as:
±(% of setting + offset)
For example, consider a power supply with a voltage setting accuracy specification of ±(0.03% + 3mV). When it is set to deliver 5V, the uncertainty in the output value is (5V)(0.0003 + 3mV), or 4.5mV. Current setting accuracy is specified and calculated similarly.
Setting Resolution and Programming Resolution
Setting resolution is the smallest change in voltage or current settings that can be selected on the power supply. This parameter is sometimes called programming resolution if operating over an interface bus such as GPIB.
Readback Accuracy and Resolution
Readback accuracy is sometimes called meter accuracy. It determines how close the internally measured values are to the theoretical value of the output voltage (after setting accuracy is applied). Like a digital multimeter, this is tested using a traceable reference standard. Readback accuracy is expressed as:
±(% of measured value + offset)
Readback resolution is the smallest change in internally measured output voltage or current that a power supply can discern.
Load Regulation (Voltage and Current)
Load regulation is a measure of the ability of the output voltage or output current to remain constant during changes in the load. It is expressed as:
±(% of setting + offset)
Line Regulation (Voltage and Current)
Line regulation is a measure of the ability of the power supply to maintain its output voltage or output current while its AC line input voltage and frequency vary over the full allowable range. It is expressed as:
±(% of setting + offset)
Ripple and Noise
Spurious AC components on the output of a DC supply are called ripple and noise, or periodic and random deviation (PARD). PARD specifications must be specified with a bandwidth and should be specified for both current and voltage. Current PARD is relevant when using a power supply in CC mode, and it is often specified as an RMS value. Because the shape of PARD is indeterminate, voltage PARD is usually expressed both as a root mean square voltage, which can provide a sense of the noise power, and also as a peak-to-peak voltage, which can be relevant when driving high impedance loads.
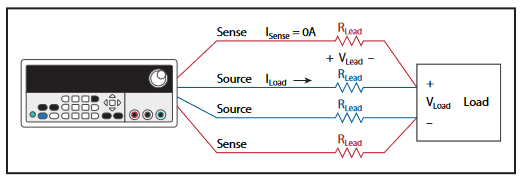
Regardless of the accuracy of your power supply, you cannot guarantee that the programmed output voltage is the same as the voltage at the DUT’s load. This is because a power supply with two source output terminals regulates its output only at its output terminals. However, the voltage you want regulated is at the DUT’s load, not at the power supply’s output terminals. The power supply and the load are separated by lead wires that have a resistance, RLead, which is determined by the length of the lead, the conductivity of the conductor material, and the geometry of the conductor. The voltage at the load is:
VLoad = VProgrammed - 2 * VLead = VProgrammed - 2 * ILoad * RLead
If the load requires high current, then ILoad is high and VLead can easily be a few tenths of a volt, especially if the power supply leads are long, as can be the case in an automated test rack. A voltage at the load could be 80mV to 160mV lower than the desired voltage (with 2A to 4A flowing through a 16-gauge wire).
The remote sensing technique solves the problem of the voltage drop in the test lead wires. Two sense lines are connected between the DUT’s load and the high impedance voltage measuring circuit in the power supply. Since this is a high input impedance circuit, the voltage drop in the sense leads is negligible and becomes the feedback control loop for the power supply.
Fast Transient Response Power Supplies
The Keithley Series 2300 special-purpose power supplies are designed to maintain a stable output voltage under the most difficult loading conditions, such as the large, instantaneous load changes generated by cellular phones, cordless phones, mobile radios, wireless modems, and other portable, wireless communication devices. These devices typically transition from standby current levels of 100–200mA to 800mA–1.5A, which represents load changes of 800% and higher. A conventional power supply typically specifies a transient recovery to a 50% load change. The Keithley Series 2300 power supplies specify transient response to 1000% load changes.
Stable During Fast Load Changes
When the mobile communication device transitions to a full power transmit state, the output voltage of a conventional power supply drops substantially until its control circuitry can respond to the transient. Conventional power supplies trade off stability for all kinds of loads against transient response. As a result, the large voltage drop and long recovery time of a conventional power supply can cause the output voltage to fall below the low battery voltage threshold of the device under test (DUT). The DUT could turn off during testing and register a false failure, affecting yield and production costs.
Series 2300 fast transient response power supplies have transient voltage droops of less than 200mV under large load changes, even with the added impedance of long wire runs between the power supply and the DUT. Thus, the Series 2300 power supplies will keep the DUT powered under all test conditions and prevent false failures. See Figure 3.
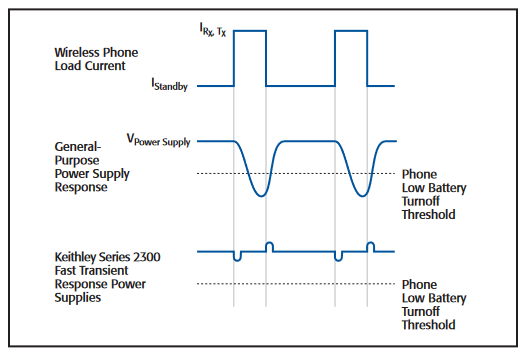
Accurate Four-Wire Measurements
To maintain an accurate voltage at the DUT load, the Series 2300 power supplies use a four-wire source circuit in which two outputs provide the power and the other two lines sense the voltage directly at the DUT load. Sensing the voltage at the load compensates for any voltage drops in long test lead runs between the power supply and the load. Furthermore, the power supplies use a wide band output stage to obtain the low voltage transient droop and the fast transient recovery time. See Figure 4.
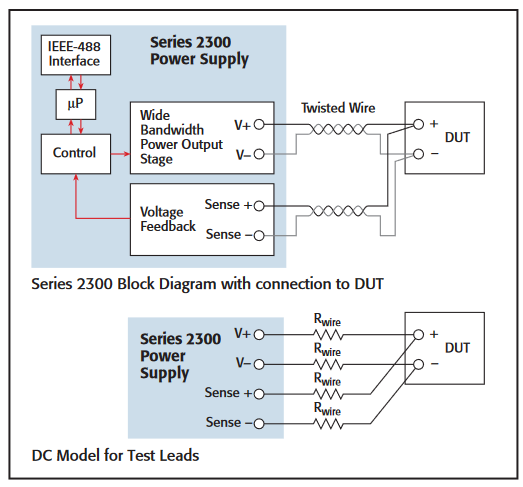
These types of power supplies often incorporate techniques for detecting if a sense lead is open or broken. An open sense lead interrupts the feedback control to the power supply, and uncontrolled, unstable output can provide improper voltages to a DUT. Series 2300 supplies either revert to internal local sensing or indicate an error condition and turn the output off.
Battery Emulation with Variable Output Resistance
Mobile communication devices are powered by batteries, so the Models 2302 and 2306 power supplies are designed to emulate the performance of a battery accurately. These supplies incorporate a variable output resistance feature, which enables a test engineer to test his DUT under actual operating conditions.
Furthermore, these supplies can sink current to simulate the battery in the discharged state. Thus, test engineers can use one instrument both to source the DUT and to act as a load for testing the charging control circuitry of the DUT and its charger.
The Models 2302 and 2306 have the ability to vary their output impedance. This allows them to simulate the internal impedance of a battery. Thus, the voltage response of a battery that must support pulsed current loads from portable products such as mobile phones can be simulated. This enables manufacturers of portable devices to test their devices under the most realistic conditions.
With a pulse-like increase in load current, the battery output voltage will drop by the product of the current change and the battery’s internal resistance. The battery voltage could fall (for the length of the pulse) below the low battery voltage threshold level of the device, and the device could turn off. Since the internal impedance increases as a battery discharges, the low voltage threshold level can be reached earlier than expected due to the combination of a lower battery voltage due to discharge time and the voltage drop across the internal resistance of the battery. Therefore, a device’s battery life could be shorter than the desired specification.Battery impedance must be considered when evaluating mobile phone handset talk time and standby performance, because voltage levels below the operating threshold of a handset’s circuitry for periods as short as 100 to 200µs are enough to shut off the handset. This phenomenon is common in TDMA (Time Division Multiple Access) phones such as GSM mobile phones where the magnitude of the high and low current levels during an RF transmission pulse vary by as much as a factor of 7 to 10. Designers need to simulate the actual performance of a battery to define an appropriate low battery threshold level. Test engineers need to simulate actual battery performance to test that the low voltage threshold level is reached with the specified battery voltage and not at a higher voltage level.
The battery simulating characteristics of the Models 2302 and 2306 can be used to test components as well as end products. For example, the power consumption characteristics of an RF power amplifier designed for use in portable products can be characterized for operation from a battery power source. As a battery discharges, its voltage decreases and its internal impedance increases. The RF amplifier draws a constant amount of power to maintain the required output. Thus, as the battery voltage falls and the internal resistance increases, the RF amplifier draws increasing amounts of current from the battery. Both peak current and average current rise significantly with increases in battery internal impedance. See Figure 5. The RF power amplifier must specify power consumption. The portable device designer must be aware of how the RF power amplifier performs as the battery discharges so that the designer can select an appropriate battery pack to ensure both that an adequate current supply is available and that the battery supplies suitable operating time between replacement or charges.

The mathematics of this effect is provided below (also see Figures 6a and 6b). They show that the voltage drop produced by pulsed current loads can have a significant effect on battery output voltage.
Vcell = An ideal voltage source
Ri(t) = The internal impedance
Rinterconnec = Resistance of cables and interconnections to the DUT
1) If Rinterconnect is small compared to Ri(t), and if
2) Ri(t) is assumed to be relatively constant during the length of the pulse, Ri(t) ≈ Ri, then
3) The voltage across the DUT can be expressed as:
V(t) ≈ Vcell - I(t)Ri(t) ≈ Vcell - I(t)Ri
where I(t) is the time varying current through the battery.
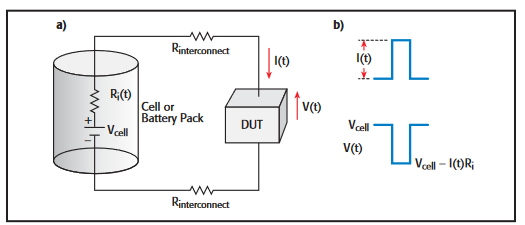
Figure 6b. Resulting output voltage with a pulsed load current.
Pulse Current and Low Current Measurements
Using a conventional (slow transient response) power supply for testing wireless devices requires that a large capacitor be placed in the circuit to stabilize the voltage during a load transition. As a result, load current measurements require using a sense resistor and a DMM to monitor load currents. The sense resistor adds resistance to the line, which further aggravates the load droop problem. The Keithley fast transient response power supplies eliminate the need for the capacitor and enable the power supply current readback circuitry to measure the load currents. See Figure 7. Keithley low current expertise enables the measurement of sleep currents with 0.1µA resolution. These supplies can also measure load current pulses from digital transmission devices. Current pulses as short as 60µs can be captured.
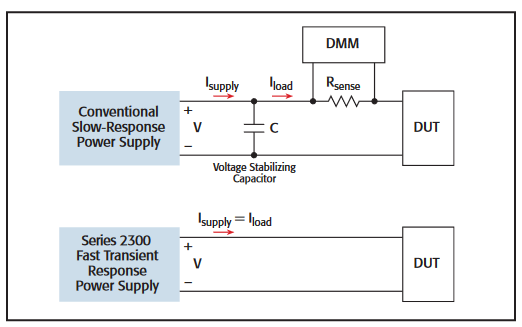
Find more valuable resources at TEK.COM
Copyright © Tektronix. All rights reserved. Tektronix products are covered by U.S. and foreign patents, issued and pending. Information in this publication supersedes that in all previously published material. Specification and price change privileges reserved. TEKTRONIX and TEK are registered trademarks of Tektronix, Inc. All other trade names referenced are the service marks, trademarks or registered trademarks of their respective companies.