Most of today’s electronic designs require many different supply voltages to function properly. In fact, many components within a given circuit require multiple voltages. This is especially true with highly-integrated system on chip and microprocessor designs in which multiple technologies interface together.
Performing DC power rail measurements is becoming increasingly difficult due to a number of factors like:
- Power efficiency features like power gating and dynamic voltage and frequency scaling or DVFS
- Dynamic loads with fast transients
- Increased crosstalk and coupling
- Switching regulators w/ faster rise times
This leads to an important question: With all these challenges, how does one ensure that each part of the system gets the correct power to meet its needs?
First let’s take a very high-level look at a power rail and some of its characteristics.
It is important to look at each DC line to see if the power supplied is within the tolerance band of a target system or device. This includes the nominal DC value of the line, as well as any AC noise or coupling present. The AC noise in a power rail signal can be broken down further into broad-band noise, periodic events, and transient events (Figure 1).
All three of these noise sources impact the quality of power that reaches a device, and it is important to reduce these noise sources to the point that the target device can operate correctly.
Before you can minimize these noise sources, you need to be able to see them and measure them accurately. But power rail measurements present several unique measurement challenges, so there are several things to consider:
- Bandwidth requirements
- System noise and additive probe noise
- Tradeoffs of AC or DC input coupling
- Loading challenges for power rails
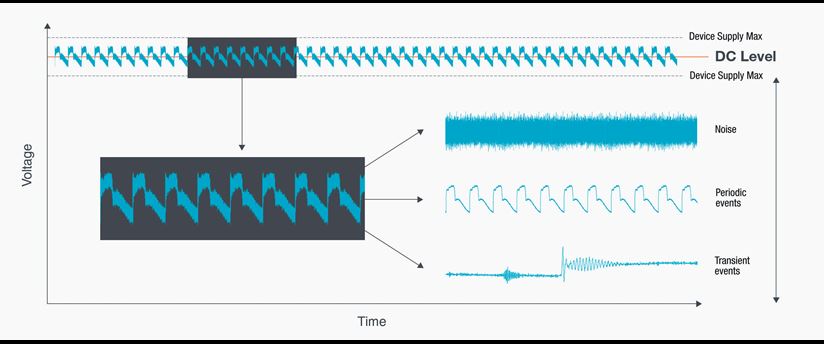
Bandwidth
Looking at many power delivery designs, it might seem that measurement system bandwidths of a few tens of MHz are enough. Most switching designs are switching in the hundreds of kHz up to perhaps a few MHz. Larger physical designs and devices that run off higher supply voltages, were less sensitive to noise. So, noise content above 20MHz was rarely a concern.
Now, as design sizes and supply voltages shrink, tolerances follow. Power distribution networks are analyzed more as transmission line environments, examining things like cross coupling, line impedances and resonant regions (Figure 2).
It is also important to remember that the fundamental switching frequency of power conversion devices may be relatively slow, but the edge speeds and rise times are typically much faster to help reduce switching loss. These edges and other interferers can excite the power distribution network in a way that generates noise and harmonics at much higher frequencies. Depending on the target device and the function of the circuit, these higher-order harmonics can interfere with operation. Choosing an oscilloscope and probe with enough bandwidth to see these events is crucial to diagnose problems related to high-frequency interference. Tektronix offers 1 GHz and 4 GHz power rail probes to directly address this need.
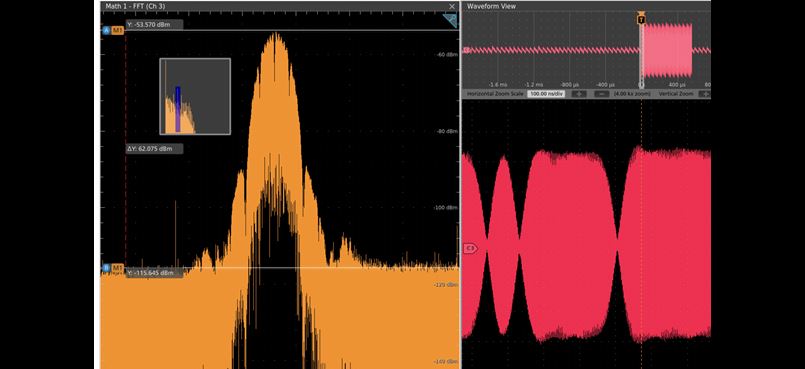
Choose the Right Connection for the Measurement Being Made
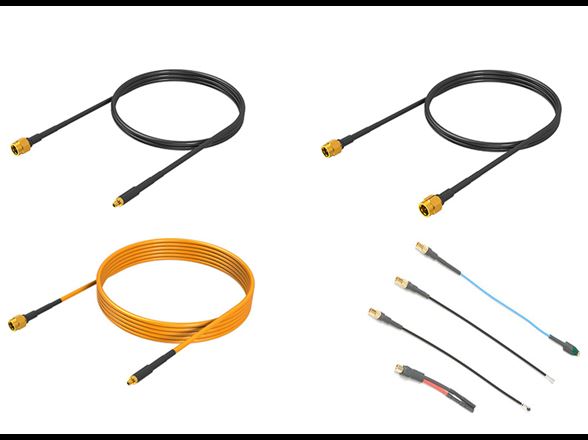
When evaluating a probing solution for power rails, it is important to remember that the connection to the DUT is the single biggest driving factor in getting quality measurements. Connections that offer low inductance paths to ground and have minimum effective capacitance will both reduce ringing and provide the most bandwidth. These connections are practically implemented through solder-in adapters and high-performance connectors. Micro coax and flex solder-in adapters offer a semi-permanent connection to devices under test when repeated tests need to be done on an unplanned test point (Figure 4).
Small form factor RF connectors like the MMCX cable offered with the Tektronix power rail probes gives repeatable and reliable access to signals when engineers can design for test. While these connections provide the best signal integrity, they are also not always convenient, as they require modifying the target device or planning for test points when designing the system. For quicker and more convenient probing, browsers and adapters can be used. Tektronix offers the TPRBRWSR1G for engineers to use when they need quick access to signals up to 1 GHz in bandwidth. Small component clips and a square pin adapter are included to help make attaching to test points easier.
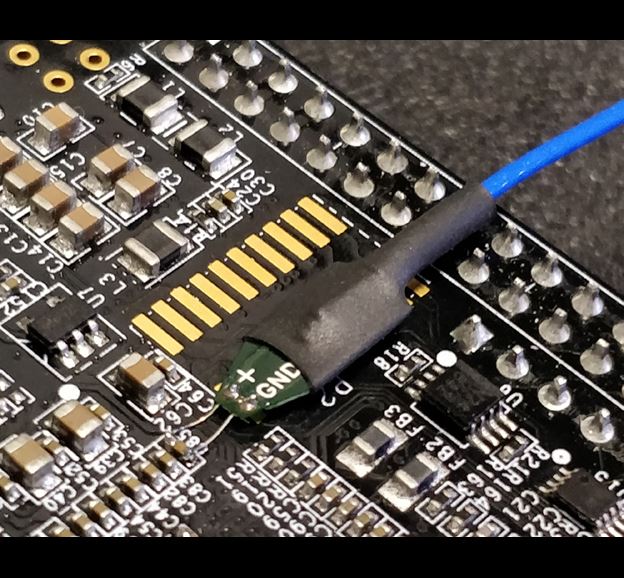
It is important to note that most browser accessories generally de-rate the bandwidth of the system. For instance, flying lead square pin adapters don’t usually have more than a couple hundred MHz of effective bandwidth. This is reduced more when clips and other connection aides are added.
The last thing to consider when choosing a connection methods is the environment that the test will be conducted in. Many system validation engineers need to test designs in extreme temperatures. Specially designed extreme temperature cables and solder in tips like those included in the TPR4KITHT can handle testing devices from -55 to +155C.
Managing Measurement System and Ambient Noise
Taking a baseline
As supply voltages become smaller, due to process geometry shrinkage, low noise measurements are required to see the small variations present on the DC supplies. Additionally, many designs are focusing more stringently on power integrity. One effect this has is tighter tolerances for each supply. To measure this, not only does the oscilloscope need to have extremely low noise to see these events, but any probe connected to the oscilloscope should contribute very little noise to the measurement. The less noise added by the measuring equipment the more confidence there can be that the signal being seen is the actual behavior of the device.
Taking a baseline noise measurement of both the instrument and any probes attached can give the user an idea of the total system noise performance. Simple measurements like peak-to-peak and RMS of the voltage present at the inputs when no signal is applied is a quick way to compare the additive noise of the probing system (Figure 5).
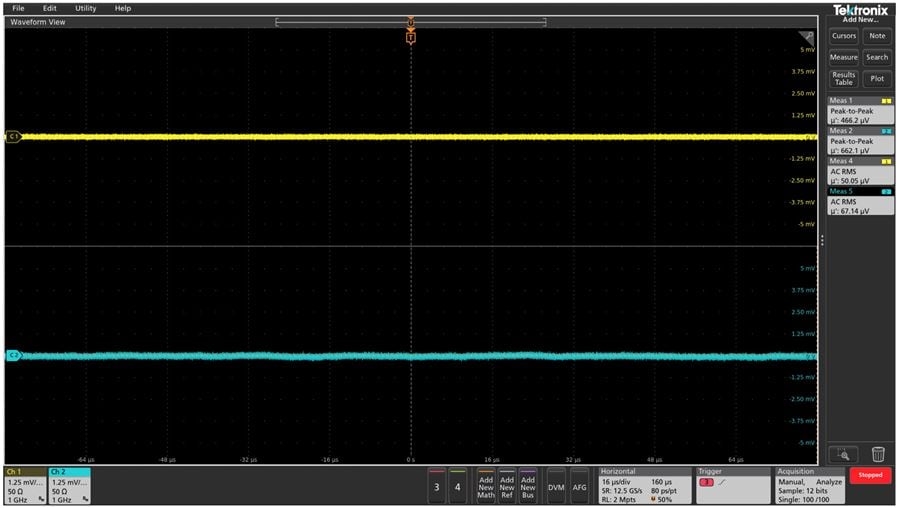
What’s wrong with using a 10x passive probe for power rail measurements?
High attenuation probes offer great dynamic range when looking at a wide variety of signals but due to the attenuation often introduce more measurement noise compared to low attenuation probes (Figure 6). This is because the signal is divided by the attenuation factor, driving it closer to the noise floor of the measurement system. This can be shown by calculating the signal-to-noise ratio (SNR).

For example, if we choose an input of 10 mV and a random noise specification of 200 μV (this specification can be found on the data sheet of your oscilloscope as random noise and is typically give in units of Vrms) then a 10x probe’s SNR would be
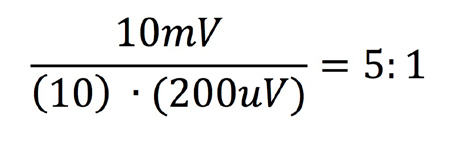
A low attenuation 1.25x probe on the other hand would have an SNR of
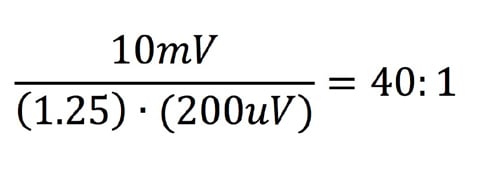
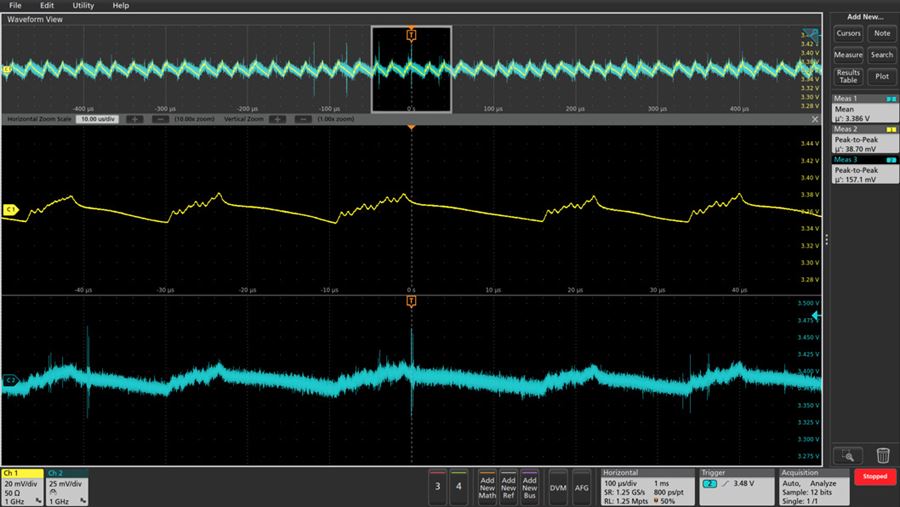
The impact of vertical scale setting on noise performance
Noise performance of an instrument scales with the vertical sensitivity setting, with higher sensitivity ranges offering better noise performances than lower sensitivity ranges. Maximizing the displayed signal on screen will provide more resolution and a more accurate representation of the signal by the instrument. Lower vertical sensitivity ranges can often make signals appear to have more peak noise on them than they really do (Figure 7).
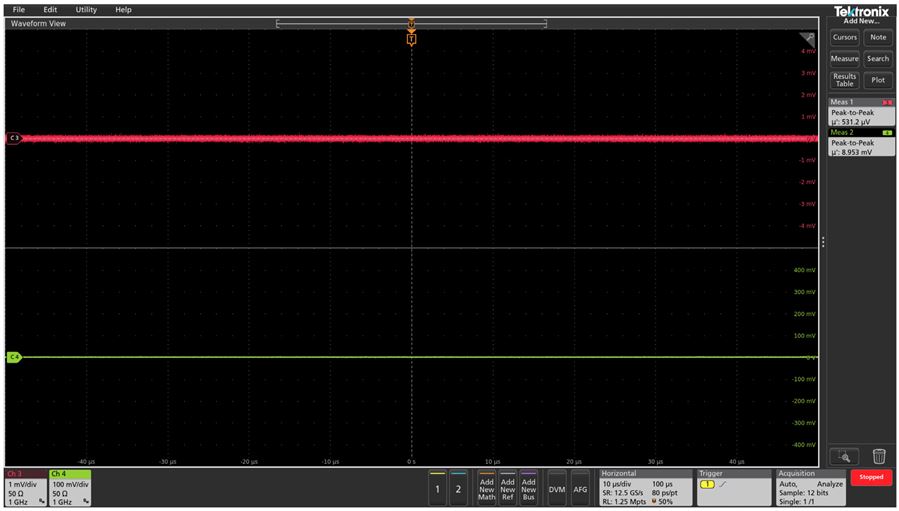
Other noise reduction methods
Functions like High Res on the Tektronix 4, 5 and 6 Series MSOs allow the user to further reduce noise by using excess sampling rate to produce higher resolution samples. It does this by applying unique finite impulse response (FIR) hardware filters based on the current sample rate. These FIR filters maintain the maximum bandwidth possible for a given sample rate while rejecting aliasing. High Res mode has the advantage of functioning in real time so transient events and single shot measurements can be made unlike other waveform averaging methods.
Choosing the Right Oscilloscope Input Coupling Setting
Why is DC offset a challenge for measuring Power rails?
Many designs have a bulk supply voltage that filters down through various DC/DC converters to the needed supply voltages required by the various ICs and systems. It is often the case that the bulk supply voltage is many times higher than the voltage needed by ICs. For example, vehicles convert 12 volts DC down to the sub 1-volt supply voltages needed to run the processors in the infotainment and safety systems (Figure 8).
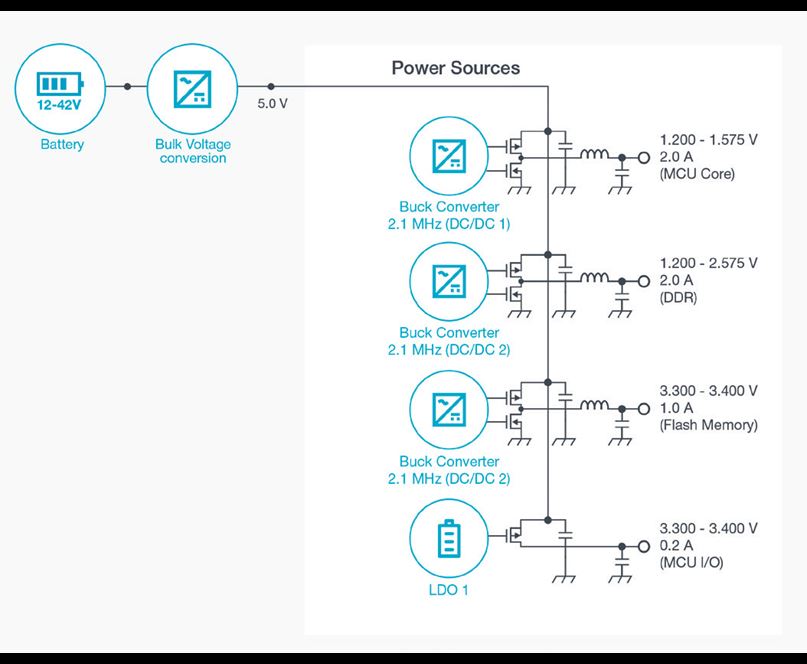
It is also not uncommon to see data centers supply power to servers via a 12, 24, or 48 V DC supply that then gets converted down to other supply voltages on the motherboard. Being able to look at every link in the chain from supply output to IC pin can help identify noise that is being transferred from other voltage domains (Figure 9).
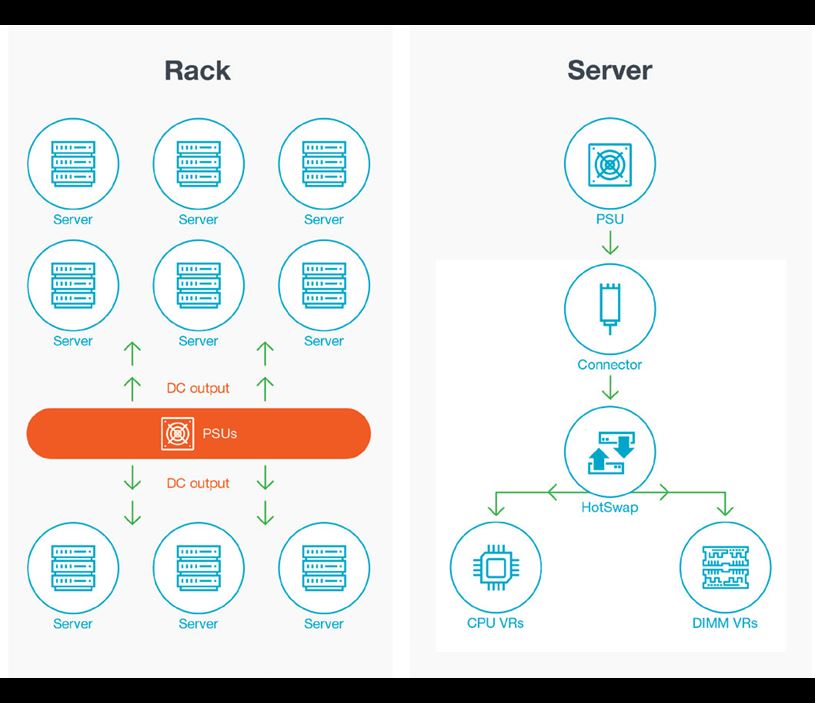
Because of this, it is important to choose a probe that offers enough offset to look at all the rails being tested in a power delivery network. This is difficult because many oscilloscope front ends limit the available offset depending on the vertical sensitivity selected. So, at lower volts per division-settings the instrument will have less offset. (In the previous section it was shown that choosing the correct vertical sensitivity range can have significant impact on measurement results.) High attenuation probes usually have more offset capability but, as shown above, typically have more noise than low attenuation probes.
Dealing with DC offset can be avoided by using the AC coupling of the scope, which removes the DC component of the signal, but this also obscures any low frequency events that may be happening, such as voltage droop.
Use DC coupling mode to see low frequency events
Provided enough DC offset can be added to the input signal, DC coupling offers a more complete picture of a device’s behavior, because AC coupling hides low frequency information like voltage line droop or creep as the load changes (Figure 10). Power rail probes are specifically designed to add enough offset range to the oscilloscope/probe system to support DC coupling on most power rails. The TPR4000 and TPR1000 have +/- 60V of DC offset to cover the most common standards in automotive, industrial, and data center applications.
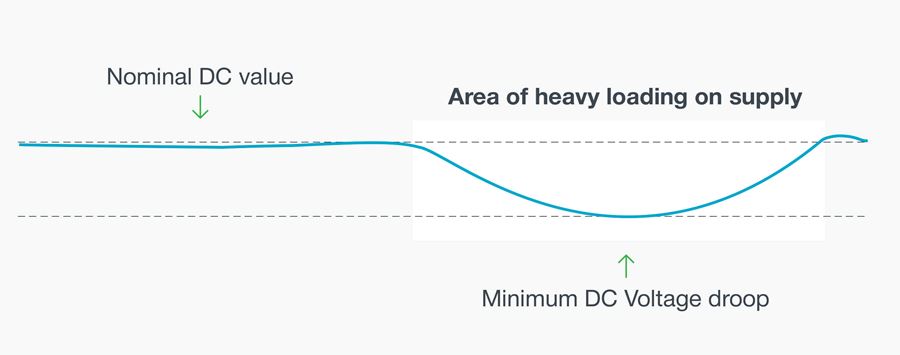
Some microprocessors and power management IC’s employ power saving features, such as dynamic frequency and voltage scaling, that change the DC supply voltage based upon the work load. These features are difficult to analyze with the instrument in AC coupled mode as the low frequency information is not shown by the instrument (Figure 11).
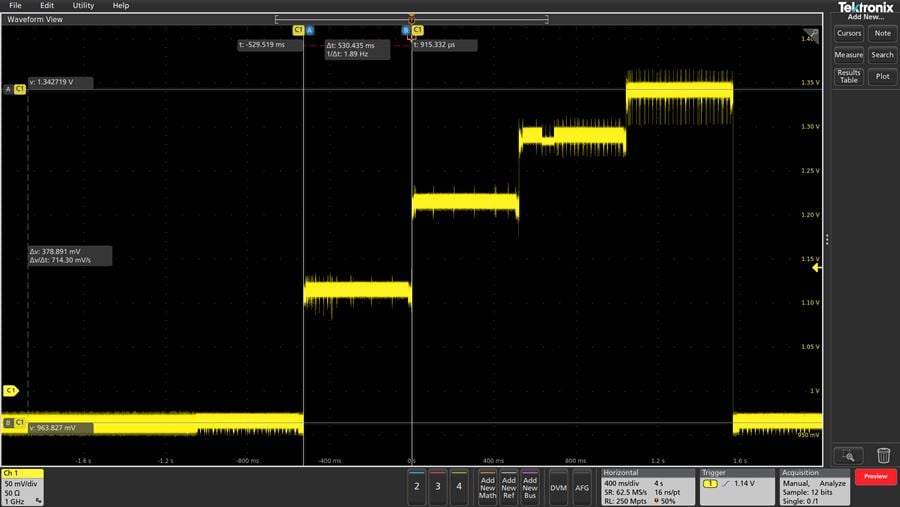
Minimizing Loading
How probe impedance affects power rail measurements
The challenge with probing power rails for the sake of making power integrity measurements is choosing a probing method to see the high frequency AC content on the DC supply, while also taking care to not load the DC portion of the signal so much that is inaccurate or interferes with device operation. High impedance probes offer the best loading for DC situations but often have excessive noise or don’t have the bandwidth necessary to see the high frequency events that are of interest while also DC coupling the signal. A 50 Ω transmission line offers excellent loading for high frequency signals on a power rail but acts as a low impedance voltage divider for DC signals.
The ideal probe for making power rail measurements would supply very high resistance at DC and a 50 Ω transmission line at AC. The Tektronix TPR4000 and TPR1000 Power Rail Probes offer a high 50 kΩ DC resistance and transition to 50 Ω at higher frequencies. This offers the best of both worlds and avoids the limitations of other probing options.
Summary
Power rail analysis will continue to be an important tool for engineers as the need for power integrity continues to rise. The Tektronix TPR4000 and TPR1000 have been specially-designed to meet the unique measurement and connectivity challenges faced when looking at DC supplies. When paired with the capture and measurement capabilities of Tektronix oscilloscopes, they make excellent power rail analysis tools for any engineer.