Introduction
Time Domain Reflectometry (TDR) has traditionally been used for locating faults in cables. Currently, high-performance TDR instruments, coupled with add-on analysis tools, are commonly used as the tool of choice for failure analysis and signal integrity characterization of board, package, socket, connector and cable interconnects at gigabit speeds.Based on the TDR impedance measurements, the designer can perform signal integrity analysis of the system interconnect, and the digital system performance can be predicted accurately. A failure analyst can use TDR impedance measurements to locate a fault in the interconnect more accurately and quickly, allowing the analyst to focus on understanding the physics of the failure at this failure location.
Single-ended TDR measurements
The TDR instrument is a very wide bandwidth equivalent sampling oscilloscope (18-20 Ghz) with an internal step generator. It is connected to the Device Under Test (DUT) via cables, probes and fixtures (Figure 1). Because of the wide bandwidth of the oscilloscope, and to ensure that this bandwidth and fast rise time can be delivered to the DUT, one must use high-quality cables, probes, and fixtures, since these cables, probes and fixtures can significantly degrade the rise time of the instrument, reduce the resolution, and decrease the impedance measurement accuracy. In a TDR probe, both a signal and a ground contact are normally required during the measurement.
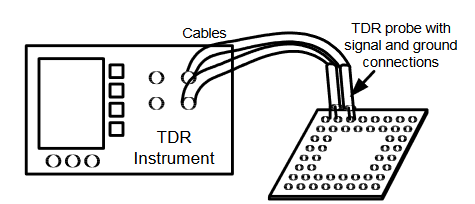
The extremely wide bandwidth and the internal source set the TDR in a class apart from any other oscilloscope, making it a high-frequency impedance and network1 characterization tool. The block diagram of the instrument is shown on the Figure below.
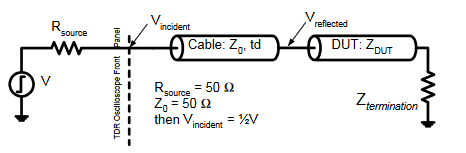
The oscilloscope step generator sends a step-like stimulus to the DUT. The signal is reflected from the DUT, and based on this reflection, we can look at the impedance, delay and other characteristics of the DUT ([1], [2]).
Equivalent resistance of the TDR source Rsource defines the characteristic impedance of the measurement system. Since the Rsource for highperformance TDR instruments available today is 50 Ohm, using non-50 Ohm cables and probes can produce confusing results. Unlike with a regular oscilloscope, no active probes or resistor divider probes are allowed for use with TDR.
The fact that the measurement system has to maintain 50 Ohm characteristic impedance does not mean that the DUT may not be non-50 Ohm. Non 50 Ohm impedances, such as 28 Ohm in case of Rambus, or 75 Ohm in case of cable TV, can be measured quite accurately.
Because of the resistor divider effect between the 50 Ohm resistance of the source and the 50 Ohm characteristic impedance of the cable, used to connect the instrument to the DUT, only ½ of the TDR source voltage V reaches the DUT initially (Figure 3).
Then, if nothing is connected to the cable (open circuit condition), after the delay equal to the round trip delay through the cable, the waveform will go up and reach the full incident voltage.
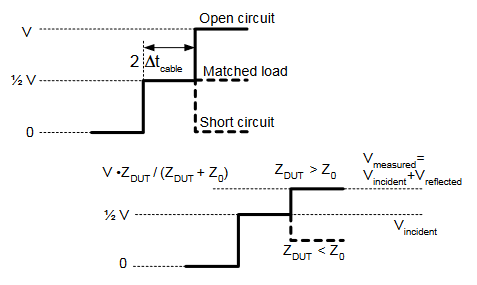
Note that everything in TDR is round trip delay. This applies not only to the cable interconnecting the TDR oscilloscope to the DUT, but also to all delay measurements on the DUT itself. In order to obtain accurate delay readout, the designer has to divide the measured delay by 2.
After the round trip delay of the cable, the voltage reflected from the DUT arrives back to the oscilloscope and is added to the incident voltage on the oscilloscope to produce the measured voltage value Vmeasured. Then, the TDR oscilloscope uses the following equations to convert the voltage, which the oscilloscope measures, to impedance and reflection coefficient:
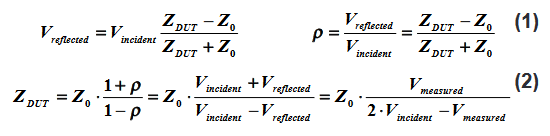
where ρ is the reflection coefficient, and the other notation used here have been described above. If you connect a shorting block to the cable, or short the signal of the TDR probe to ground, thus creating a short circuit condition, the waveform will go to 0 volts. If you connect a 50 Ohm termination ("matched load"), the waveform will stay at the Vincident level, equal to ½ V.
By observing Figure 3, the reader notices that we have better impedance measurement resolution between 0 and 50 Ohm, than between 50 Ohm and infinity. Moreover, any impedance over 1000 Ohm is infinitely high, equivalent to an open circuit condition.Since the characteristic impedance of the free space (which is what we are measuring with TDR) is only 377 Ohm, this fact does not create any issues - no practical trace in a board, package, connector or cable interconnect will have impedance which is much higher than the characteristic impedance of the free space. It is worth noting that this limitation is not TDR-specific - there is no high-frequency measurement instrumentation that can measure impedance over 1000 Ohm at high frequency with any level of accuracy.
TDR and lumped element analysis
Experienced TDR users can, without difficulty, recognize a "dip" in a TDR waveform as a shunt capacitance, and a "spike" as a series inductance. Any L and C combination can also be represented as shown on Figure 4 below
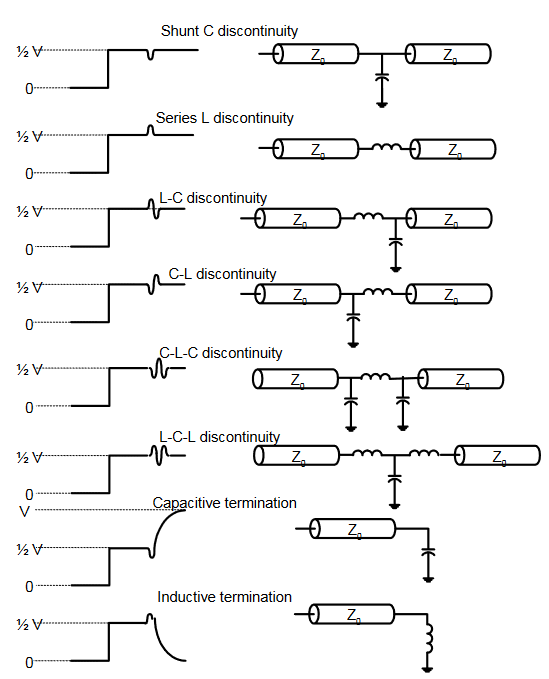
A series C or a shunt L, however, will represent a high-pass filter for the TDR signal, and the resulting reflection from the elements beyond such series C or shunt L can not be interpreted easily.
However, sometimes a DC blocking capacitor must be used in series with the TDR cable to protect the input of the TDR sampling head from the DC voltage on the line. This type of capacitor is a very wide band component (operating from DC to 15-25 Ghz), and presents a high-pass filter with characteristics that are determined by the capacitor value, its parasitics, and the 50 Ohm impedance of the cable on both sides of the capacitor. Since we know the characteristics of such filter well, we can still characterize the DUT accurately
TDR resolution and rise time
The issues of TDR resolution are often misunderstood or misrepresented, because the TDR resolution is believed to be completely governed by the following rule of thumb. Two small discontinuities,such as two vias in a PCB, can still be resolved as two separate ones, as long as they are separated by at least ½ the TDR rise time:
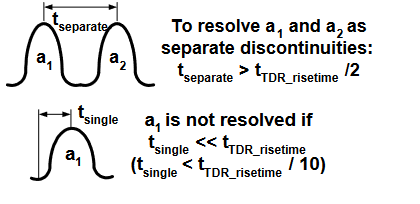
If these two vias are not separated by half the TDR rise time as it reaches the vias, they will be shown by TDR as a single discontinuity. Assuming we use good cables, probes, fixtures, and we can deliver the full 30-40ps rise time of the instrument to the discontinuities in question, the minimal physical separation between these vias will be 15-20ps. For FR4 board material with dielectric constant Er =4, this results in 2.5-3mm (0.1") resolution. Often this number (or other similar calculation) is quoted as the TDR resolution limit.
However, in real-life situation, the designer typically is looking to observe or characterize a single discontinuity, such as a single via, or a single bondwire in a package, rather than separate several of such vias or bondwires! In this case, the above rule is totally irrelevant, and TDR can allow the designer to observe discontinuities of 1/10 to 1/5 of the TDR rise time, bringing the numbers above to 5ps or less than 1mm (25milliinches) range (Figure 5b).
Furthermore, there are well developed relative TDR procedures for observing and characterizing even smaller discontinuities. For signal integrity modeling and lumped interconnect analysis, there are JEDEC standard procedures [3], [4] for package characterization, allowing the designer to measure sub millimeter capacitive and inductive elements in 100fF and 200-300pH range. For failure analysis applications, there are well-established procedures utilizing golden device comparisons [5], [6].
Taking this discussion further, practically all modern high-speed digital standards and applications - from Gigabit Ethernet to Infiniband - still have rise times which are slower than the 30-40ps rise times of the TDR. Since TDR waveforms show the designer how a certain discontinuity would exhibit itself in the signal path, then if the discontinuity does not cause a reflection of fast TDR signal, it will have even less effect on the slower real signal propagating through this discontinuity. Therefore, if the fast TDR rise time does not allow the designer to observe a certain discontinuity, then an even slower real signal will not show it either!
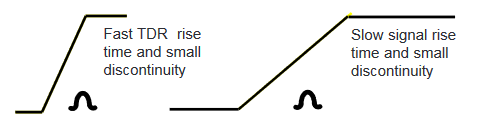
Differential TDR measurements
Differential TDR measurements are an important capability that the TDR instruments provide, since most of the modern signaling schemes and standards are differential - whether it is USB2.0 or Firewire, Infiniband or Rapid I/O, SCSI or FibreChannel, Gigabit Ethernet or Sonet - thus requiring differential impedance measurements. In addition, differential TDR is very useful for crosstalk characterization, whether it is crosstalk between two single-ended traces or crosstalk between differential pairs.
TDR instruments provide up to 8 single ended or 4 differential channels, allowing the designer to look at crosstalk between up to 4 differential pairs, and making TDR the most capable high-frequency differential instrument currently available.
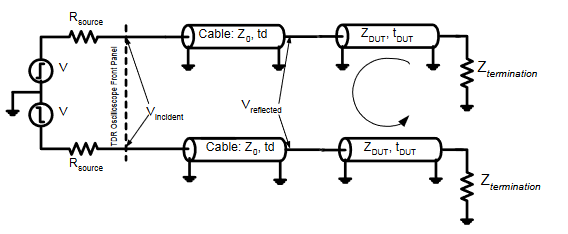
The TDR de-skew capability ensures that both signals in a differential pair reach the DUT traces at the same time, and allows to correct for delay differences between the cables, probes and fixtures. If the TDR is not properly de-skewed, the resulting skew can produce significant inaccuracies in differential impedance measurements and differential line modeling.
Differential TDR measurements are necessary only if we are looking to obtain differential impedance, or to characterize coupling between the lines. If there is no coupling or other differential interaction between the lines, single ended TDR measurement will provide us with all the information that we need.
Differential and odd, common and even mode impedances
Differential impedance is defined as the impedance between the two transmission lines when the two lines are driven differentially, whereas the odd mode impedance is impedance of one line in the differential pair under the same drive conditions. Common mode impedance is impedance between the two lines when the two lines are driven with a common mode signal, whereas the even mode impedance is the impedance of a single line in the differential pair under the same drive conditions [7], [8]. In case of mildly non-symmetric differential pair, the following equations will apply:
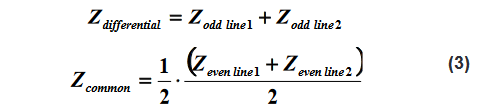
To measure the odd mode impedances of line 1 and 2 (Zodd line1 and Zodd line2), the designer would connect the two outputs of the TDR sampling head to the two transmission lines under test (not forgetting to connect the ground plane if such ground plane is present) with the TDR signals switching in the opposite direction (i.e., differential stimulus), and measure the impedance of each line in the differential pair. To measure the even mode impedance (Zeven line1 and Zeven line2), the designer would switch the TDR sources in the same direction (i.e., common mode stimulus), and measure the impedance of each line in the pair. Different TDR oscilloscopes will have different procedures for measuring the differential and common mode impedances, but the net results are the same. In case of a symmetrical differential pair, the following equations are true:

In presence of coupling between the lines, the odd mode impedance is always lower than the selfimpedance of a single line, which in turn is lower than the even mode impedance:

where Lself, Cself, Lm, and Cm are the self and mutual inductance and capacitance of the line pair per unit length, and Ctotal=Cself+Cm. Even though only the impedance of one of the lines in the line pair is measured to obtain odd, even and self impedance, the interaction between the lines will account for the difference between these impedance values.Differential mode and common mode impedances are the most useful parameters from a practical design standpoint, whereas odd mode and even mode impedances are very useful from interconnect modeling and simulation point of view [7].
Cables, connectors, and probes
TDR cables and probes will degrade the rise time of the signal measured on the TDR oscilloscope approximately as follows:

where tTDR is the rise time measured on the TDR scope with no cable connected, and f3dB is the 3dB bandwidth of the cable and probe. The factor of 2 in this equation is due to the fact that the signal has to take a roundtrip through the cable before it is observed and measured on the oscilloscope.Specifying a cable with a 3dB bandwidth (f3dB) of about 10 Ghz for the scope with its own rise time of 30ps, will result in the rise time at the cable end of about 58ps. Specifying 3dB bandwidth of 17.5 Ghz will give the rise time end of the cable of about 40ps.
In an application where the TDR cable length can be limited to under 2 ft, requesting a "lowest-loss" flexible cable from your favorite high quality low cost coaxial cable manufacturer would be sufficient. If you are working with a 3-4 ft cable, however, or require full resolution and rise time that the oscilloscope can offer, you will have to work with a high-end microwave cable manufacturer. Semi rigid cables can provide better performance than flexible ones, but are more difficult to use. SMA connector is commonly used in TDR cables, since it provides acceptable performance, and can be mated directly to the 3.5mm connector found on 20Ghz TDR sampling modules4.
When using a probe for taking TDR measurement on a board, package, or connector, the designer has to define a ground location near the signal location.
If such ground location is not available, or if the spacing from signal to ground varies widely across the PCB, the designer may have to use a probe which has a long ground wire, or a variable length wire. For a probe with a long ground wire, the parasitic inductance will be very large, and will not allow the designer to obtain a good quality TDR measurement.Variable length ground wires, and variable pitch (signal-to-ground spacing) probes do not provide sufficient measurement repeatability, and will not provide accurate impedance measurement results or signal integrity interconnect models.
In many cases, a simple, inexpensive and convenient TDR probe can be fabricated by using a 3 inch length of semi-rigid coaxial cable with an SMA connector, exposing the center conductor of such cable, and either using the sleeve of the semi-rigid coax as the ground contact, or attaching a ground wire. Using different diameter coax will result in different probe pitch, and making the center and ground conductors shorter or longer can provide the right trade-off between convenience of use and performance. A differential TDR probe can be fabricated by using two single ended probes of the same length, connecting the sleeves of two such coaxes together if possible, and attaching the appropriate ground leads as necessary (Figure 8).
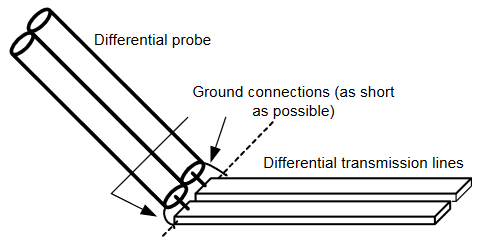
If your TDR measurements are sufficiently repeatable, you can sometimes de-embed your probe or cable parasitic inductance by either connecting your probe to a precision 50 Ohm resistor on a calibration substrate, and subtracting this measurement from your DUT measurement, or by following the calibration and normalization procedures in your TDR oscilloscope. These procedures, however, do not replace the true impedance profile de-embedding described below, as they only de-embed the probe and the cable, but do nothing about the "ghost" reflections inside the DUT itself, which are also discussed in the next section.
Multiple reflections and the true impedance profile
In case of single impedance interconnect, such as a test coupon on a PCB, or a controlled impedance cable, the TDR oscilloscope produces impedance readouts accurately. In other practical cases, however, such as a real trace on a board, which often has to travel through different layers with potentially different impedances, connected with vias, with connectors and packages mounted on the board, the situation is more complex, and we have to deal with an effect known as "multiple reflections."
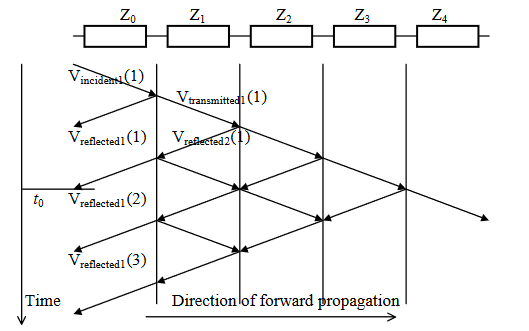
TDR oscilloscope uses equations (1) and (2) to compute reflection coefficient and impedance of the DUT. These equations assume that the oscilloscope knows exactly what the incident voltage was at the impedance discontinuity in question. In reality (Figure 9), as the TDR signal propagates through multi-impedance interconnect, the incident voltage at each discontinuity changes, since at each discontinuity portion of the signal energy is reflected back to the oscilloscope, and only a portion of the signal energy continues to propagate. Moreover, the signal traveling back to the oscilloscope is re-reflected back into the DUT. As a result, the signal begins to bounce back and forth within the DUT, creating the effect of multiple (or "ghost") reflections. The impedance measurement error in the oscilloscope quickly adds up, resulting in incorrect impedance readouts. The deeper into the DUT we are trying to measure impedance, the more multiple reflections we will accumulate, resulting in larger impedance measurement error. An impedance deconvolution algorithm, discussed in a number of publications (for example [9]-[11]), and implemented in IConnect TDR software, allows the designer to de-embed the multiple reflections and accurately compute the true impedance profile for the each segment in the multiimpedance DUT.
As an example, consider the following test vehicle, consisting of an outer board trace (microstrip) with impedance changing from 50 Ohm to 25 Ohm back to 50 Ohm, with the length of each 50 Ohm segment being approximately 1", and the 25 Ohm segment being approximately 5" long. As we can observe in the red (DUT.wfm) waveform, the multiple reflections exhibit themselves very strongly for this multi-segment interconnect, not only giving an incorrect impedance reading (about 44 Ohm) for the second 50-Ohm segment, but also showing some ghost reflections in the area where the waveform should have shown the open circuit signature. The true impedance profile, computed in IConnect, deembeds the multiple reflection effects and provides the accurate true impedance profile for the DUT.

In another example, we have looked at an open trace failure in a BGA package (Figure 11). In this example, the TDR waveform (reflection profile) provides a confusing indication about where the failure in the DUT occurred. Once the true impedance profile is computed, however, any confusion about the failure location is removed, and the failure location is clearly identified.
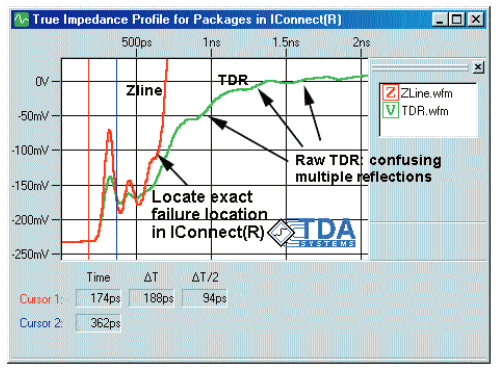
The TDR oscilloscope does not intentionally "confuse" the instrument user. It shows the user the reflection profile of the DUT, pointing out how a real signal will be distorted by the DUT impedance mismatches and discontinuities. When a designer aims to merely observe the signal distortion, reflection profile is what is needed. If the designer's goal is to accurately measure the impedance in a multi-segment interconnect, produce a SPICE or IBIS signal integrity model for the interconnect, or locate the failure, the impedance deconvolution algorithm is required to convert this reflection profile into the true impedance profile. In addition, when a designer attempts to zoom in on a portion of a multi-segment interconnect, and window out the rest of the data, such windowing is only possible with the true impedance profile, not with the TDR reflection profile otherwise the multiple reflections will remain in the windowed data and will distort the analysis results.Examples of such multi-segment interconnects are a transmission line on a real circuit board, changing layers and going through connectors and packages, or a cable-connector assembly attached to a circuit board, or a modern BGA or flip chip package - as opposed to, let's say, a test coupon on a circuit board, impedance of which can be read accurately without the use of the impedance deconvolution algorithm.
Other TDR measurement issues
Using good measurement practices
To obtain good quality impedance, signal integrity modeling, and failure analysis data, it is important to follow general good measurement practices when using a TDR oscilloscope. The instrument should be turned on and its internal temperature should be allowed to stabilize for 20-30 minutes before performing any measurements. Calibration, compensation and normalization for the instrument must be performed regularly, as specified by the instrument manufacturer. The internal instrument temperature must be within the specified range from the calibration points for the given instrument.To maximize the resolution of the scope, particularly in the time axis, it is important to zoom in on the DUT but at the same time to allow a window that is sufficiently long to include all the reflections related to the DUT. A window that is too short may prevent the designer from obtaining complete and accurate information about the DUT. When the designer intends to perform true impedance profile analysis, as implemented in IConnect TDR software, it is also important to window out the transition related to the sampling head to the cable interface, and focus on the DUT portion of the waveform, so as to ensure that the impedance deconvolution algorithm, discussed above, could perform correctly.
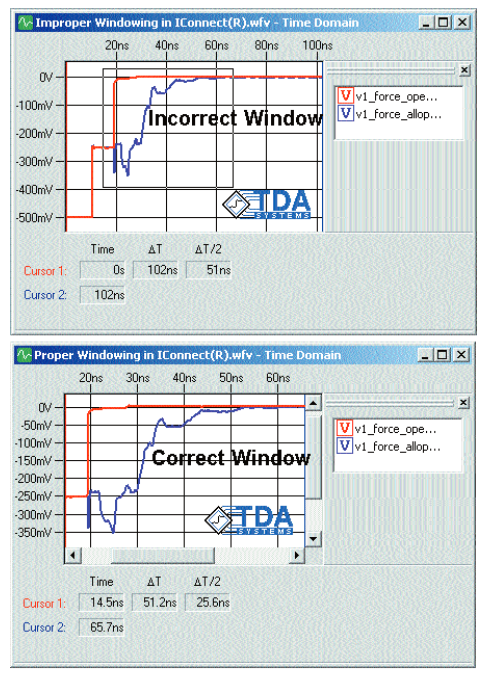
TDR measurements of "splits" and "stubs"
If the board trace under test splits into two or more directions, as is the case for address lines in a memory module, the TDR instrument shows the sum of all reflection from all the N legs in the split, but cannot separate which reflection came from which leg in the split. If the splits are of the same impedance and delay (as sometimes is the case in a "star" interconnect topologies), they can be simply represented by transmission lines running in parallel, and the impedance measured by the TDR oscilloscope equals Z1 / N, with the delay of each trace being equal to the delay measured by TDR (Figure 13).
In case of a stub (which often takes place in a daisy chain configuration), if the length of each stub on the main bus is much shorter than the rise time of the signal propagating through the bus, the stubs can be treated as lumped capacitances loading the main bus, thus simplifying the measurement problem.

Time Domain Transmission (TDT)
TDT stands for Time Domain Transmission. We can stimulate the DUT on one side, and using the remaining channels on the TDR instrument, measure the transmission through the DUT, whether in singleended or differential mode.
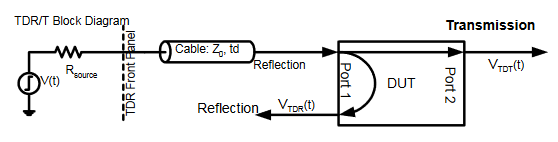
TDT is useful for demonstrating the effect that the interconnect impedance discontinuities will produce at the receiver, as well as for characterization of lossy transmission line parameters, such as rise time degradation, return loss, and skin effect and dielectric loss [12]. In addition, based on the TDT measurement, IConnect TDR software can predict the eye diagram degradation through the given interconnect.
The same de-skew capability, used to de-skew the TDR channels during the differential measurement, can be used in order to de-skew the TDR channels during the TDT measurements.
Frequency Domain and TDR
The fast rise time of the TDR instrument allows the designer to obtain a wide-band characterization of the interconnect, since the incident TDR step contains all the harmonics up to approximately the 3dB frequency of the TDR signal. The TDR measurement can be converted into the return loss (S11), and the TDT measurement into insertion loss (S21).
Differential TDR measurements can also be converted into corresponding differential and mixed mode Sparameters (Figure 15), [13].
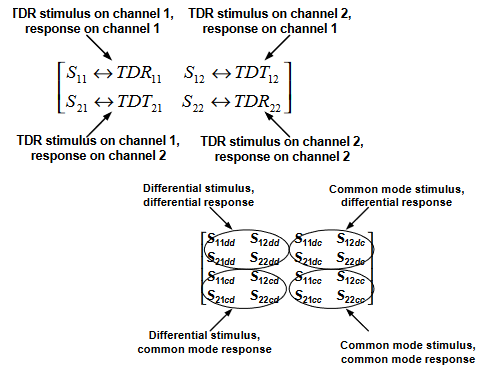
VNA and TDR
Some vector network analyzers (VNA) have time domain capability, converting the data from frequency into time domain. Such time domain option in a VNA can be used in lieu of a TDR measurement.However, the difficulty of use, extensive training required, and higher expense of a VNA instrument,compared to a TDR instrument with the same rise time, hardly justify use of VNAs as a TDR replacement in impedance measurement and other signal integrity applications, [13]. While VNA may be considered essential for some analog, RF and microwave applications, in high-speed digital signal integrity applications TDR is simpler and easier to interpret, less expensive, and perfectly suitable for characterization of circuit board, package, socket, connector, and cable interconnects.