Working as a design engineer or electronic technician is difficult. The products we build MUST be higher performance than those that they replace, or why bother? These complicated, high performance products require powerful design tools if they’re to be finished on time and on budget. How else could we design a more capable and complicated product in the same timeframe it once took to design a simple product?
COMPONENT VENDORS have come through with amazing time saving tools to help engineers design more complex products in less time. In the digital domain, machine code moved to assembly code followed by all of the higher level languages like "C". Eventually, engineers began to leverage real time operating systems (RTOS) and powerful library modules. In the analog domain, tubes went to transistors to operational amplifiers to special purpose, application-specific integrated circuits.
A similar transformation has quietly been taking place on your test bench, too. If a new instrument can help you quickly and safely find all of the subtle problems that were overlooked during the design phase as well as the manufacturing problems, then why not use it?
There's a powerful tool—the SourceMeter SMU Instrument—that can help you do all these things and should be within easy reach beside your oscilloscope and a good digital multimeter (DMM) (Figure 2). But don't confuse the SourceMeter SMU Instrument with the many older products often designed for the production environment that were referred to as source measure units.SourceMeter SMU instruments are much easier to use on the bench.
It's important to first point out a few differences between a SMU instrument and its forefathers, the DMM and the power supply. Then, after you have a good idea of what a SMU can do for you, I'd like to entertain you with a narrative describing two fictional characters, Dave and Karen, each using a SourceMeter instrument to help them save time on the test bench. Let's get started!
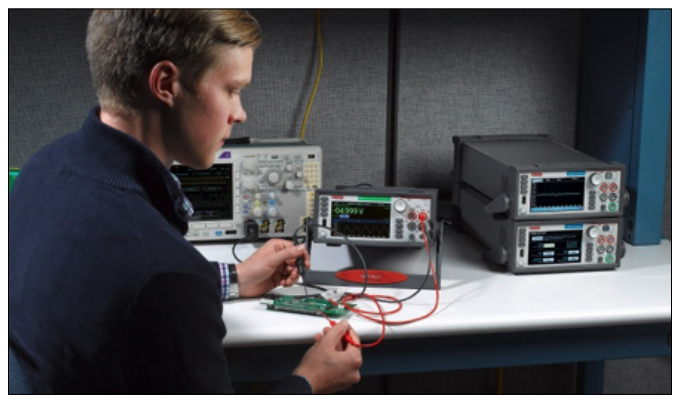
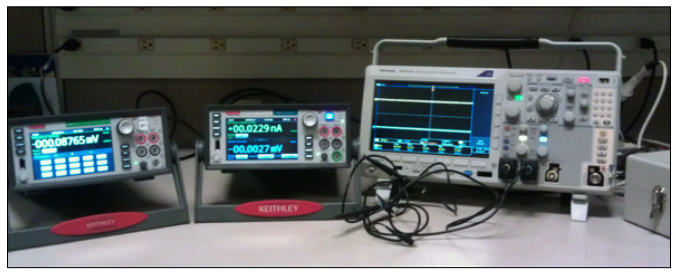
What is an SMU or SouceMeter instrument?
Perhaps you know a bit about SMU instruments and may even be considering buying one. You may already have a power supply and a DMM on your bench and are wondering how an SMU or SourceMeter instrument can make you more productive. A closer look at the SourceMeter instrument may help you convince your manager that you need one! So what is this instrument that everyone is talking about? Is it a power supply? A DMM? It can take measurements and plot them against time (Figure 4), so is it like an oscilloscope.
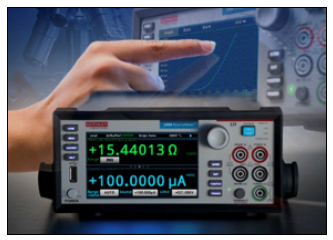
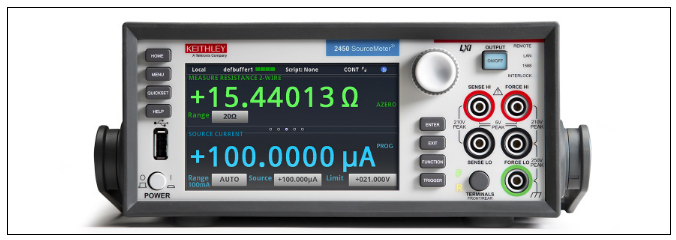
In a general sense, the SMU and SourceMeter instrument can be either a voltage source (with a programmable current limit) or a current source (with a programmable voltage limit). Both the source and limit functions can be programmed with 16-bit resolution, and both quantities can be measured with the precision of a high resolution DMM. Comparing and contrasting the finer points with the more familiar power supply or DMM may help clarify the differences:
- The SourceMeter instrument is a fast power supply. Many power supplies are designed to limit current in a DC sense, but the SourceMeter instrument has a much higher bandwidth. The speed of the source and limit function depends on load, but in some cases can source or limit, to a settled current or voltage value in as little as 50ms. In most cases the SourceMeter current limit is fast enough to protect components and entire circuits from over current conditions which is not true of a low cost power supply. The SourceMeter Instrument also allows you to apply voltage or current in pulses to limit device power
- The SourceMeter Instrument has an exceptional dynamic range. Most power supplies only have a few ranges, and many have only one. Depending on the model, the large dynamic range allows you to measure currents from as low as a few hundred femto-amps all the way up to 50A. The lower current ranges are great for component characterization, finding components that are slightly damaged, and debugging very low power applications.
- Like a DMM, the SourceMeter Instrument has a high resolution, 22-bit measure function for both voltage and current.
- The SourceMeter Instrument can be programmed to pulse voltage or current or to program any unique sequence of voltage or current. The built-in programming language is so powerful that you can think of it as an arbitrary waveform generator (ARB) that can source both voltage and current.
- Unlike a DMM, the SourceMeter Instrument maintains high input impedance up to the voltage capability of the instrument. All DMMs use resistive dividers to measure high voltages (and oscilloscopes, too).
- The SourceMeter Instrument can source positive and negative current at either positive or negative output voltage, so its output amplifier covers all four source quadrants and, it can be used as an electronic load. Most power supplies cannot handle all four quadrants.
You're probably beginning to imagine how you might use a SourceMeter Instrument on your own test bench. But, in case you still have reservations, let's take a look at some interesting ways in which others have found to use a SourceMeter Instrument or two. I think you'll find that combining and integrating useful features from DMMs, power supplies, arbitrary waveform generators, and oscilloscopes creates a test instrument even more useful than the individual instruments are alone.Please allow me to introduce Dave and Karen
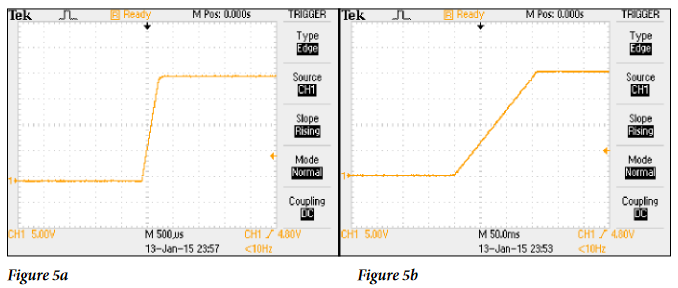
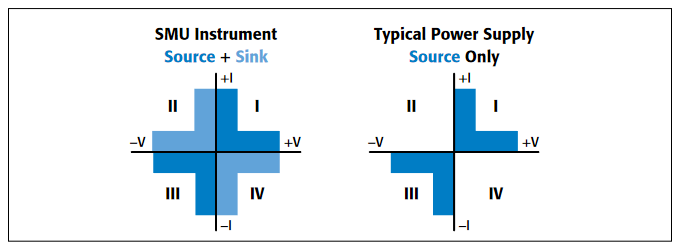
Dave: The Power Supply Design Engineer
Dave is a design engineer for a company designing power supplies. This week Dave is nervous. One hundred pieces of his new power supply board just arrived on the dock and his confidence level is low. The schedule was just too tight, and the specifications were changing right up to ordering the boards. To make matters even worse, this supply is not a simple design. It's a feature–rich, softwarecontrolled power supply with many different operating modes for use in different applications. Some of the power supply features include programmable supply voltage, step response, efficiency, etc. It was designed with a power factor correction (PFC) off line (mains) supply followed by several push-pull forward converters with lots of secondary outputs. This supply has many other software-controlled features, not all of which are finished. Just thinking about how much damage bad software could do to this power supply made Dave break out into a cold sweat.
Before sending the boards off to be built, he took one to his test bench. Using his brand new SourceMeter Instrument, he applied the rated supply output voltage to each of the output supply printed circuit board traces (PCBT), as well as to the line (mains) voltage circuits. When the supply is running, it's going to have to operate at the rated voltages anyway, so why not try them out with a safe 10µA current limit first? The line voltage (and safety spacings) looked okay, as did all of the low voltage supplies, but the 700V high voltage output hit the 10µA current limit right away. Something was very wrong. The SourceMeter Instrument reported the limit voltage at 350V, a clear indicator of a voltage breakdown issue rather than a short, and the breakdown occurred at 350V.
After some digging, this problem was easily solved by milling a slot at a location between the high voltage net (high voltage traces on the PC board) and a short ground track on the PC board. It turns out that voltage spacing rules for this net were never enforced by the computer aided design (CAD) tool. The engineer was maintaining spacing as he ran the traces, but must have forgotten one. Note to self Build all voltage spacing into the CAD tool, not just the safety related spacings. Finding this mistake early allowed the slot to be deviated before the boards were populated. Correcting the breakdown problem after all the parts were on the board would have been much more difficult.
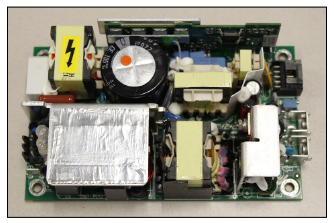
A week later, a dozen boards appeared on Dave's desk completely populated. Dave removed the jumper between the mains supply and the DC-DC converter so each could be powered up separately. The off-line supply powered up normally running from the SourceMeter Instrument. The current limit for the SourceMeter Instrument was set by looking at the quiescent current (the current drawn by a circuit when it is not amplifying a signal or driving a load) of a similar, but older design. The DC-DC converter did not fare as well. With the SourceMeter Instrument once again in current limit, Dave continued to find each and every mistake safely. Dave knew that he had to set the current limit correctly for a "working" but unloaded power supply. If he had brought up a broken DC-DC converter with an unlimited power supply, it may have resulted in damage. Power supplies simply do not limit current fast enough to protect electronic circuits. One by one, Dave found and corrected all of the design and manufacturing problems using his oscilloscope, DMM, and a second SourceMeter Instrument. The second SourceMeter Instrument came in handy (the first one was busy powering the supply) measuring two- and three-terminal devices, as well as making measurements inside the operating supply possible only because SourceMeter instruments always float the LO terminal. Buyer beware not all SMU instruments float their LO terminals. Quite often, some SMU instruments connect the LO terminal right to ground by default.
Some other testing that can be performed on discrete component devices may include:
- Zener diodes by sourcing a small current through the diode at a limit voltage just higher than the actual zener voltage. This can even be done in the circuit with the power supply powered up or down!
- Transistor Hfe (current gain) by using one SourceMeter Instrument to source current into the base-emitter junction while measuring the collector current with a second SourceMeter Instrument forcing voltage across the transistor emittercollector terminals. This measurement can be done in either pulse mode or DC.See Figure 8.
- MOSFET gm (trans conductance) by using two SourceMeter instruments, one to source voltage across the gate-source terminals, and another to source voltage across the transistor drain-source terminals while measuring the drain current.This measurement can also be done in either pulse mode or DC.
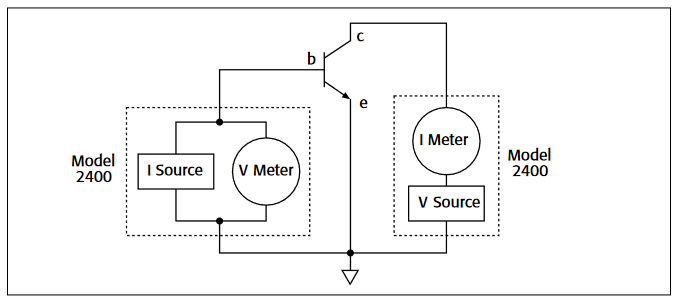
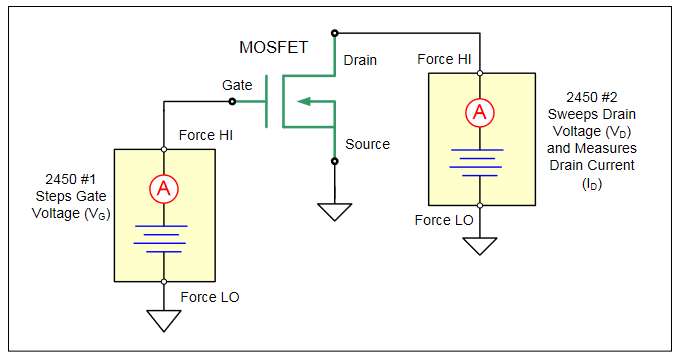
With all the apparent problems corrected, Dave thought it was time to see if the supply would run on its own. Dave re-installed the jumper separating the offline supply from the DC-DC converter and let it run. While measuring the voltage ripple on each output with his scope, the supply stopped working and a loud pop was heard on the board. Something had failed, but curiously not right away, hours later in fact. Dave knew that the parts were all in correctly, or it would not have run for so long.
Dave set his SourceMeter Instrument to source current and measure voltage, with a 1.5V limit. His aim was to test all of the power devices in the supply. With the new power supply board powered down, Dave sourced current from the source to drain, and from the drain to source of each MOSFET in the design, modifying the source current value to match the device rating. The 1.5V volt limit was chosen so that no other component on the net would power on while checking each of the MOSFET’s channel resistance. Over current conditions often render the channel conductive in both directions without a gate enhancement voltage. Checking the gates for leakage would have been the next test but there was no need for that. One of the push-pull MOSFETs measured only a few millivolts when sourcing current using this technique. A good part would have reached the voltage limit in one direction, and showed the parasitic diode voltage (0.6V) in the other direction. What could be wrong now?
Retrospectively, Dave should have continued to use the SourceMeter Instrument to power the unit rather than using the offline supply. Setting the burned up board aside, Dave grabbed a new board and set his SourceMeter Instrument up to provide line voltage by executing an AC line voltage test script that he wrote and uploaded into the SourceMeter Instrument. The script programmed the output to a 50Hz sinusoid with the correct limit current for the quiescent current of the unloaded supply. The new board powered up fine with all supply voltages within specifications. If this board worked like the first one, Dave had only a few hours to find the issue before the problem surfaced again, this time with the safe current limit enabled. Using an oscilloscope, Dave looked at the voltage across each rectifier capturing an entire power supply switching cycle.
As show in Figure 10, this change in voltage across the rectifier diode is a reflection of the load current defined by the log amp I/V curve that can be found with a SourceMeter Instrument as described below. If these traces (top trace no load, bottom trace full load) do not look like a simple shift or if the shift is not correct, there may be a problem in the secondary circuits following the rectifier.
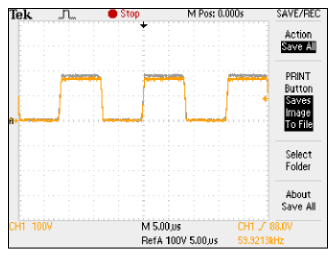
Each voltage on each rectifier of each output looked correct. If the rectifier current was too high for any reason, the rectifier voltage (essentially a log amp), would have shown this increase in current over time. Dave knew what the voltages should be by using a second SourceMeter Instrument to measure the I-V characteristics of each diode by programming and sweeping voltage and measuring current. While looking for his scope probes, Dave noticed the SourceMeter Instrument powering his new board was in current limit. Whatever was wrong only took a half hour on this board to fail. This time, however, nothing failed and the board did not burn up. All Dave had to do was to turn off the output of the SourceMeter Instrument to program the instrument to zero volts and restart the AC line voltage script. Running again, Dave used his oscilloscope to measure the primary currents of each push-pull supply (Figure 11).
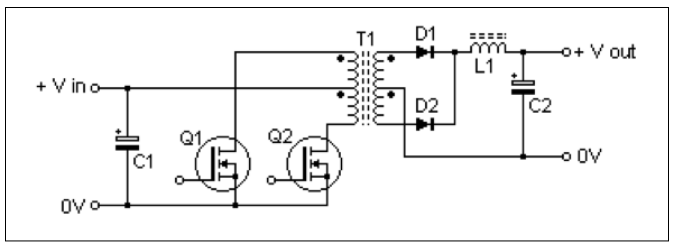
Since noone thought to put a resistor here, Dave had to measure the primary current by measuring the small voltage drop across a one-inch PCB trace. This test, normally done with a floating oscilloscope, could also be made with a high resolution digitizing DMM (Figure 12).
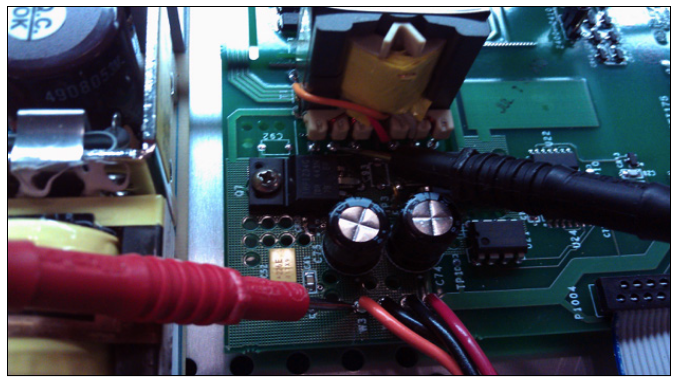
This measurement proved enlightening. After only five minutes, Dave noticed that the magnitude of the current was increasing! Since Dave knew that the secondaries were fine (his first test), that left one of two possible problems. Either the transformer was incorrectly designed or manufactured, OR the micro controller defining the push-pull ON time for each half cycle of the pushpull MOSFETs were unequal, a condition known as flux imbalance. It took Dave the rest of the day and all of the next day to find the problem.
The problem was in the controller code. Apparently, an interrupt executing ONLY during half of the push-pull sequence, and always on the same switch, was changing the ON time enough to cause a flux imbalance problem in the transformer. Dave's transformer design was particularly sensitive to this issue since this design had very little magnetizing inductance. While his first two attempts only helped, extending the fault from an hour or so to a day or so, it took an entire week to finally fix the problem.
On this project, the SourceMeter Instrument saved Dave a lot of time and rework. Dave would have had to repair the boards if the SourceMeter Instrument had not been available to power these units safely. He still had to repair the first board, which nobody wanted now. Dave had to remove and reapply power from his SourceMeter Instrument a dozen times over the days looking for the problem.
For most power supply applications, the SourceMeter Instrument is just as useful in the product design audit as it is during the power supply design. Because SourceMeter instruments can sink current just as accurately as they source current, a useful feature that most power supplies cannot accomplish, the engineering audit team at Dave’s company loves to use their SourceMeter Instrument as an electronic load. This fact in addition to the fact that they are faster than most electronic loads differentiates the SourceMeter Instrument from the electronic load and makes the SourceMeter Instrument much more useful.
The SourceMeter Instrument can even be used as a solar panel simulator when designing MMPT (maximum power point tracking) switching supplies. For this application, solar cells look like a current source where the sourced current depends on the applied voltage and the illumination. For a given illumination, the SourceMeter Instrument can be programmed to change the sourced current as the measured voltage changes. The overall limit voltage is set to the open circuit voltage of the cell.
Karen in the next story used her SourceMeter Instrument to look like a very "tiny" low current solar cell.
Karen: A Design Engineer Working on a SuperSecret Project
Karen's job could not be more different from Dave's. Whereas Dave has to deal with hundreds of watts, Karen’s job never takes her beyond a few nanowatts. Karen is working on a secret government contract (not really, remember this is just a story) to develop a watch to be worn by soldiers. Although it does have a battery, it never needs to be charged—it’s the ultimate energy scavenger. It tells the soldiers when anyone NOT wearing a watch comes close. It relays vital signs to central command. It tells the new recruit soldier where he is allowed to go and where he is not allowed to go. And, of course, the time and date are perfectly synchronized to the second with every other watch. Sometimes it communicates key information to the soldiers by passive LCD, sometimes by flashing lights, and sometimes from a mild electric shock that nobody else can hear, see, or detect. This high-tech piece of technology scavenges power from body heat, light, and movement. It has dozens of operating modes, each consuming a different quiescent current.
Karen is also nervous. One hundred raw printed circuit boards for the secret watch have just arrived on her desk. The remainder of the watches (the watch housing and wrist strap) was still waiting to be shipped. Unlike in Dave's case, Karen was not concerned about the damage that hundreds of watts could do. Her concern was that she and her software team would have trouble keeping the total super-secret watch current consumption under the magic threshold of 1nA, the lowest guaranteed current delivered by the combined energy harvesting techniques used in the watch. If the watch current ever exceeds 1nA for any amount of time, the watch MUST reduce its load for a period of time to "make up" for the extra load. The current consumption of the watch not only depends on which of the watch features are active, but iit's also a function of which microprocessor peripherals are enabled and even how the code is written!
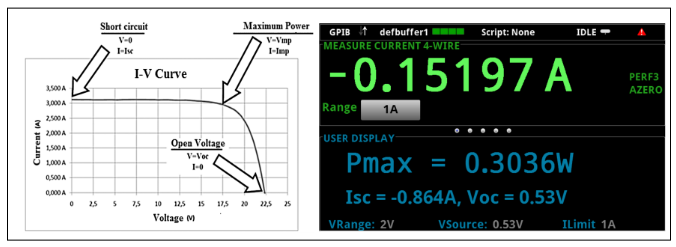
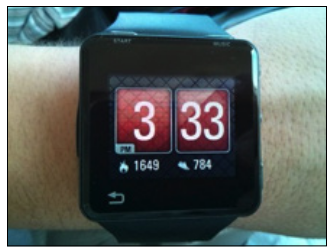
Early in the product development cycle, Karen tested each of the peripherals with her Keithley Model 2450 SourceMeter Instrument (Figure 15), and a low leakage guarded test fixture. The Model 2450 offered the low current measurement ranges she needed and the built-in low noise current triaxial cable connectors required to connect to the test fixture.

With her Model 2450, she recorded not only the current consumption, but also the rate of change of the current when enabling or disabling the candidate circuits. Everything seemed to matter. Even changing the current consumption too quickly forced the energy harvesters to operate at a lower efficiency. The Model 2450was even used to simulate the I-V characteristics of the solar cells to test the watch ultra-high efficiency power converters. All of this testing required a fast source capable of operating at high voltages as well as low currents. The Model 2450 was the only game in town up to the challenge.
Karen carefully inserted the watch in the test fixture. With the watch housing and wrist strap unavailable, the test fixture and triaxial cabling had to be used to guarantee good measurements of the device current consumption. For those who may not be familiar with the purpose of a test fixture, understand that surrounding the entire device with a Faraday shield will assure that your measured current will be from the watch itself, and not any spurious externally coupled interference current (see Figure 16).
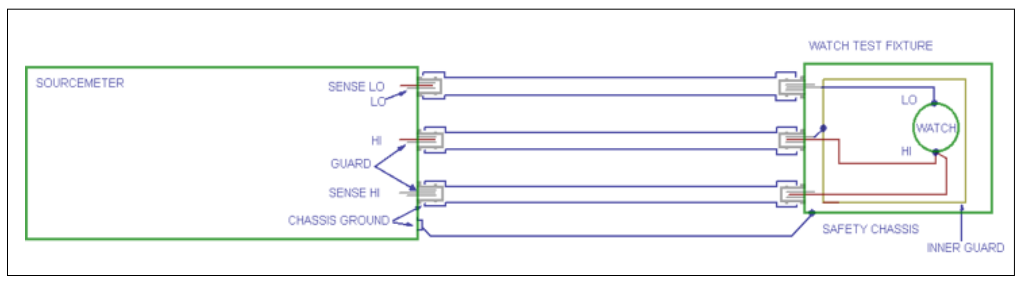
The fixture also allowed the engineers and auditors to interface to the watch using their computers, rather than using the watch buttons. This interface was developed to speed up the audit, which could now be performed anywhere.
Earlier in the week, Karen wrote some code (to be run natively on the Model 2450) to continuously monitor the watch load current, which was being powered by the Model 2450. The code would track all instances over the 1nA limit as well as the average current. This test setup (watch, 2450, test fixture, and remote interface) was duplicated for each of the design and audit engineers. Not only could the audit fail due to a misbehaving feature, it could also fail if the watch were to consume excessive current. Whenever this happened, Karen and her team would have to go back and inspect the specific hardware state causing the failure and find a solution. The Model 2450 was programmed to send a response back to a PC set up to notify the engineers whenever this event proved true. The audit results were unpredictable. The team had to repair just as many instances of excessive current consumption as broken feature implementations. The Model 2450 saved the team time in debugging compared to the power supplies and electronic loads that they previously used that did not have the low current performance needed for the application.
Conclusion
Although these examples are fictitious, test and measurement requirements like this are very real. In the same way that Dave and Karen used their SourceMeter instruments, such as the Keithley Model 2450, to help save time solving problems while reducing repair and rework, you may be able to apply some of the same principles at your work place. Remember, every project is different and every project encounters different obstacles. You have only your own knowledge and detective skills and the test instruments available to you to get the job done. You should also remember that the usefulness of the tool is directly related to your understanding of what the tool is capable of doing and how to use the rich set of today’s more complicated instruments safely. So, give yourself the same competitive advantage as Dave and Karen. Consider adding a SourceMeter instrument to your bench!
Find more valuable resources at TEK.COM
Copyright © Tektronix. All rights reserved. Tektronix products are covered by U.S. and foreign patents, issued and pending. Information in this publication supersedes that in all previously published material. Specification and price change privileges reserved. TEKTRONIX and TEK are registered trademarks of Tektronix, Inc. All other trade names referenced are the service marks, trademarks or registered trademarks of their respective companies.
1KW-60034-0 4.27.15