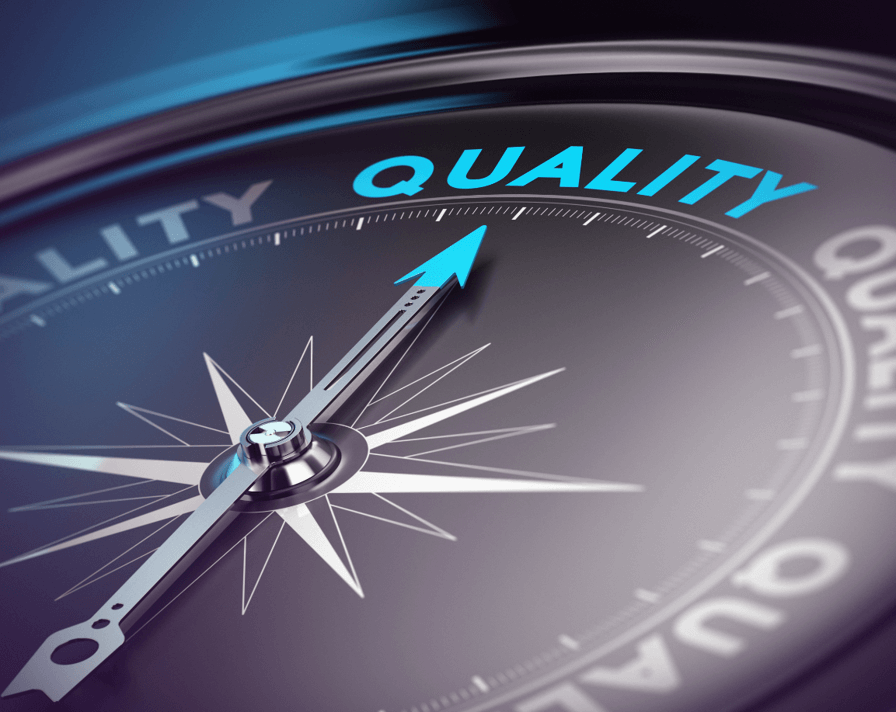
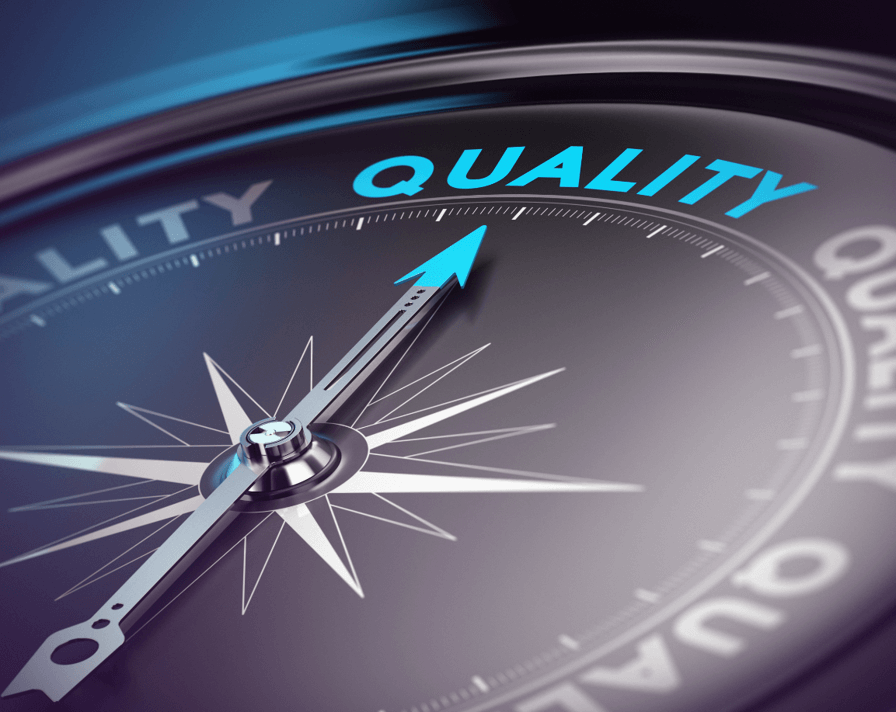
Equipment calibration is essential to improving a company’s bottom line by minimizing the risk of product defects and recalls and enhancing a reputation for consistent quality. In its most basic form, calibration is the measuring of an instrument against a standard. As instruments become more complicated, successfully identifying and applying best practices can reduce business expenses and improve organizational capabilities.
Calibration services are crucial because out-of-tolerance (OOT) instruments may give false information leading to unreliable products, customer dissatisfaction and increased warranty costs. In addition, OOT conditions may cause good products to fail tests, which ultimately results in unnecessary rework costs and production delays.
A decision to purchase a calibration service, therefore can be a smart one. That said, choosing a calibration provider based on price alone, may actually result in hidden costs and the potential for quality issues to affect your product or service. In fact, when “low-cost” calibration providers do not have the equipment or expertise to complete a comprehensive calibration, they may consider shortcuts, such as “functional tests only” of certain parameters, the use of calibration standards that do not fully meet the requirements outlined in the calibration procedure, or allow inexperienced or partially-qualified technicians to perform the work.
When Low-Cost Calibration Providers Cost You Money
- Engineering redesign – Measurements made with poorly calibrated equipment can result in financial losses due to product re-inspection, rework, sorting and scrap. New engineering designs that are tested and validated with suspect equipment due to low-quality calibrations can require months of re-designs, software modifications or rebuilding of prototypes. There is a significant cost of downtime as personnel time and resources are being expended on resolving the issues that will create scheduling challenges for all other production functions.
- Potential legal issues – If a product makes it into the marketplace that was calibrated poorly, there could be even higher consequences such as recalls, personal injury, lawsuits and consumer dissatisfaction. Significant damage to a company’s reputation could occur resulting in the loss of potential business opportunities, dwindling corporate profits, and eventually employee layoffs.
- Potential tragedy – Think accurate calibration is important? The best way to exemplify this is by sharing an extreme example such as aircraft failure in flight. In October of 2018 in Indonesia, Lion Air Flight 610 crashed shortly after takeoff. The suspected improper calibration of one of the Angle of Attack (AOA) sensors is believed to have caused erroneous data to be sent to the Maneuvering Characteristics Augmentation System (MCAS) system. This caused the MCAS to activate multiple alerts and repeatedly produced flight control issues with the aircraft that the pilots could not properly manage. The flight crashed into the Java Sea killing 189 passengers and crew.
- Monetary loss – While saving money with low-cost calibration sounds like financial gain, improper calibration has a cost. The cost of the calibration of a torque wrench, as example, that is used for the tightening of the wheels or other components on a business jet. The calibration of the torque wrench only costs around $50, but if the wrench is not calibrated properly, damage to the wheel or landing structure of the aircraft could quickly add up into the thousands of dollars.
- Using multiple calibration providers – Ideally, you would want to choose a calibration provider that has the capability to calibrate all or most of the equipment within your organization. Having a large number of calibration providers could lead to additional costs for shipping and extended turn-around times. In some cases, multiple calibration labs from the same company do not use the same standardized calibration procedures across their facilities.
Selecting the Right Calibration Partner
To ensure a calibration service provider is using defined, comprehensive calibration procedures, ask the following questions:
- Will you show me the calibration procedures you are using and the source of those procedures?
- Does your quality policy provide assurance that these procedures will be used consistently over time?
- How do technicians select calibration procedures?
- Are you able to provide full calibration data and accredited measurement uncertainties for all data points?
Quality calibrations require the use of comprehensive calibration procedures. These are often available from instrument manufacturers or other reputable sources. These procedures specify uncertainty levels for calibration standards used as well as pre-calibration steps to ensure proper equipment operation. They also define the required calibration points used to verify an instrument’s full range of operation.
Be sure not to let the hidden costs of low-cost calibration damage your organization!