Contact us
Call us at
Available 6:00 AM – 5:00 PM (PST) Business Days
Download
Download Manuals, Datasheets, Software and more:
Feedback
Data Acquisition Systems (DAQ)
Switching, measuring, or integrating your data with ease
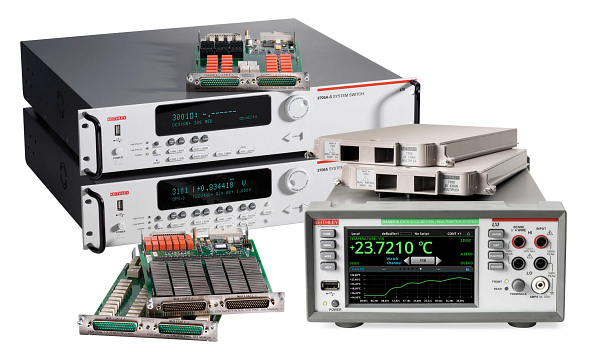
What is DAQ?
Data Acquisition (DAQ) is a process of gathering and analyzing data from various physical phenomena. It plays a crucial role in engineering, scientific research, and industrial settings, enabling real-time monitoring and control of parameters like temperature, pressure, and voltage. DAQ is essential for quality control, process optimization, and troubleshooting.
What is a DAQ System?
A DAQ (Data Acquisition) system is a comprehensive setup for measuring and collecting data from various sensors or transducers, crucial in fields like scientific research, industrial automation, and more. It typically includes sensors or transducersthat convert physical or electrical signals into measurable quantities, signal conditioning circuits for amplifying, filtering, or digitizing signals for enhanced quality and accuracy and a data acquisition device that samples and digitizes signals, preparing them for further analysis.
Find a DAQ System for Your Application
As a leader in test and measurement technology, Keithley provides DAQ systems that are not just high-performing but highly adaptable, meeting the needs of diverse industries from environmental monitoring to automotive testing.
Why Choose Keithley DAQ Systems?
Precision, Efficiency, and Innovation
High accuracy, high-speed scanning, flexible configuration, user-friendly software, and industry-leading support are all key aspects that make Keithley’s DAQ systems ideal for a wide range of applications and industries.DAQ System Enhanced Monitoring and Testing Applications
Keithley's DAQ systems are tailored for complex testing scenarios:
- Extensive Channel Support:
- Up to 576 channels for large-scale data acquisition.
- Precision Measurements:
- High-precision data capture using 61⁄2-digit and 71⁄2-digit DMMs.
- Versatile Applications:
- Ideal for aerospace, defense, and more, thanks to adaptable features
A Comprehensive Monitoring and Testing Solution
Keithley's DAQ systems are specifically designed to address a wide range of monitoring and testing applications, including:
- Environmental Monitoring: For precise monitoring of environmental conditions.
- Burn-in and Accelerated Life Testing: Identifying potential weaknesses in products, enhancing durability and performance.
- Failure Analysis: Investigating root causes of product failures to improve design and performance.
Specialized Automotive Testing Capabilities
Keithley's DAQ systems excel in automotive testing, equipped to handle various components:
- Airbag and Seat Belt Testing: Systems designed for testing airbag inflators and seat belt pre-tensioners, ensuring safety.
- Wiring Harness Analysis: Efficient testing solutions for automotive wiring harnesses.
How to Choose a Data Acquisition System
Selecting the right Data Acquisition (DAQ) system is crucial for obtaining precise and reliable measurements in various applications. The effectiveness of a DAQ system lies in its ability to accurately meet specific measurement requirements, which involves considering several key factors:
- Accuracy and Resolution: The core of DAQ system effectiveness is its accuracy, largely determined by the resolution of the analog-to-digital converter (ADC) and the stability of the reference voltage. Opt for systems with higher resolution ADCs and stable reference voltages for more precise measurements.
- Sampling Rate: Essential for applications involving rapidly changing signals, a higher sampling rate is crucial for high-speed data acquisition and dynamic control systems.
- Signal Conditioning: Look for robust signal conditioning capabilities, including amplifying, filtering, or digitizing signals from various sensors, to enhance their quality and accuracy. This is particularly important for adapting to different sensor types like thermocouples, strain gauges, and accelerometers.
- Software Compatibility and Functionality: Ensure the DAQ system comes with user-friendly software that offers effective data visualization tools and supports multiple programming languages. Compatibility with various operating systems like Windows, Linux, or Mac OS adds to the system’s versatility.
- Channel Count: Consider the number of channels the system can support. A higher channel count increases the system's flexibility and scalability in handling multiple signal types.
- Environmental Adaptability: Assess the system’s ability to operate under the specific environmental conditions of your application.
- Budget Constraints: Evaluate the overall cost, which includes the price of the system or device and any additional accessories or software required.
By carefully considering these aspects, you can choose a DAQ system that not only aligns with your specific needs but also ensures a balance between performance, versatility, and budget. This approach guarantees that the selected system can effectively and efficiently handle the required data acquisition tasks.
Dive Deeper Into Data Acquisition Systems
Key Insights Gained from DAQ Systems
DAQ systems are instrumental in capturing and recording data from various sensors, crucial for monitoring physical or electrical phenomena. These systems empower engineers with data-driven insights, allowing them to make more informed decisions in areas such as:
- Trends and Patterns Analysis: Engineers use DAQ systems to identify trends in parameters like temperature or pressure, enabling early detection of potential issues.
- Fault Detection and Diagnosis: By analyzing data from DAQ systems, engineers can pinpoint faults in systems, identifying malfunctioning components or sensors.
- Performance Optimization: DAQ data aids in identifying inefficiencies, guiding engineers to optimize system performance and increase productivity.
- Predictive Maintenance: Analyzing data trends helps in predicting maintenance needs, preventing system breakdowns.
- Quality Control: In manufacturing, DAQ systems are pivotal in ensuring product quality, detecting any deviations from required specifications.
Important DAQ Measurements
A data acquisition system is a vital tool used in various industries to collect and analyze data from different sources. It is designed to measure and record a wide range of physical and electrical parameters. The data acquisition system consists of sensors, signal conditioning, analog-to-digital converters, and a computer or data logger to process and store the acquired data.
Temperature
One of the most common parameters measured by a data acquisition system is temperature. Temperature sensors are used to monitor and control the temperature in various applications such as industrial processes, HVAC systems, and scientific experiments. The data acquisition system can measure temperature using different types of sensors, including thermocouples, resistance temperature detectors (RTDs), and thermistors.
Pressure
Data acquisition systems are also used to measure pressure in different applications. Pressure sensors are utilized to monitor and control pressure levels in industrial processes, automotive systems, and medical devices. The data acquisition system can measure pressure using sensors such as strain gauges, capacitive sensors, and piezoelectric sensors.
Voltage and Current
Another important parameter measured by a data acquisition system is voltage and current. These measurements are crucial in electrical and electronic systems to ensure proper functioning and safety. The data acquisition system can measure voltage and current using sensors such as voltage dividers, current transformers, and shunt resistors.
Flow
Data acquisition systems are commonly used to measure flow rates in various applications, including water management, oil and gas industries, and chemical processes. Flow sensors such as turbine flow meters, electromagnetic flow meters, and ultrasonic flow meters are used to measure the flow of liquids and gases. The data acquisition system collects and analyzes the flow data to monitor and control the flow rates.
Acceleration and Vibration
Data acquisition systems are also utilized to measure acceleration and vibration in different applications, including structural health monitoring, automotive testing, and aerospace industries. Accelerometers and vibration sensors are used to measure the acceleration and vibration levels. The data acquisition system captures and analyzes the data to assess the structural integrity and performance of the systems.
Humidity
Humidity measurement is essential in various industries, including HVAC systems, food processing, and pharmaceutical manufacturing. Data acquisition systems can measure humidity using sensors such as capacitive humidity sensors and resistive humidity sensors. The acquired data helps in maintaining optimal humidity levels for the desired applications.
Light and Sound
Data acquisition systems are used to measure light and sound levels in applications such as environmental monitoring, audio recording, and lighting control systems. Light sensors such as photodiodes and phototransistors are used to measure the intensity of light. Sound sensors such as microphones and piezoelectric sensors are used to measure sound levels. The data acquisition system captures and analyzes the data to monitor and control the light and sound levels.
Examples of DAQ Systems In Use
Use Case 1: Monitoring Environmental Conditions
Imagine an engineer working on a project to design a new building in a coastal area. One of the critical factors to consider is the impact of environmental conditions, such as wind speed and direction, on the structural integrity of the building. In the past, engineers had to rely on manual measurements and calculations, which were time-consuming and prone to errors.
With a DAQ system in place, the engineer can install sensors on the building to continuously monitor the environmental conditions. The sensors collect data on wind speed, direction, temperature, and humidity, among other parameters. This real-time data is then fed into the DAQ system, which processes and analyzes it, providing the engineer with accurate and up-to-date information.
By having access to this data, the engineer can make informed decisions regarding the design and construction of the building. They can identify potential risks and take necessary measures to ensure the safety and stability of the structure. The DAQ system not only saves time and effort but also enhances the overall quality and reliability of the project.
Use Case 2: Testing and Validation of Automotive Components
Another scenario where a DAQ system proves its importance is in the automotive industry. Engineers working on the development of new vehicle components, such as engines or suspension systems, need to conduct extensive testing and validation to ensure their performance and durability.
Traditionally, this involved setting up complex and expensive testing rigs, manually collecting data, and analyzing it. This process was not only time-consuming but also limited the amount of data that could be collected and analyzed simultaneously.
By implementing a DAQ system, engineers can automate the data collection process and gather a vast amount of data from multiple sensors simultaneously. For example, when testing an engine, sensors can be placed to measure parameters like temperature, pressure, and vibration. The DAQ system captures this data in real-time, allowing engineers to analyze the performance of the engine under different conditions.
This comprehensive data enables engineers to identify potential issues, optimize designs, and make data-driven decisions to improve the overall performance and reliability of automotive components. The use of a DAQ system not only accelerates the testing process but also enhances the quality and safety of the final product.
Use Case 3: Monitoring and Controlling Industrial Processes
In industrial settings, engineers often face the challenge of monitoring and controlling complex processes to ensure efficiency, productivity, and safety. A DAQ system plays a vital role in this regard by providing real-time data on various parameters, allowing engineers to monitor and control the processes effectively.
Consider a manufacturing plant where a chemical process is carried out. The engineer needs to monitor parameters like temperature, pressure, flow rate, and pH level to ensure the process is running smoothly and within the desired specifications. Without a DAQ system, this would require manual monitoring and frequent adjustments, leading to potential errors and inefficiencies.
By implementing a DAQ system, the engineer can automate the data collection process and receive real-time updates on the process parameters. If any parameter deviates from the desired range, the system can trigger alarms or even automatically adjust the process to maintain optimal conditions.
This level of automation and control not only improves the efficiency and productivity of industrial processes but also enhances safety by minimizing the risk of human error. The engineer can focus on analyzing the data and making informed decisions to optimize the process, leading to cost savings and improved overall performance.
FAQs: Data Acquisition (DAQ) Systems
What is the purpose of data acquisition?
What does a DAQ system measure?
A DAQ system can measure a wide range of physical or electrical phenomena, including:
- Temperature: Using thermocouples, RTDs (Resistance Temperature Detectors), and thermistors.
- Voltage: Measuring across components or power sources to monitor electrical systems.
- Current: Often measured with shunts or transformers to understand power flows.
- Pressure: Using pressure transducers or sensors to monitor fluid or gas pressure in pipelines or systems.
- Force and strain: Through strain gauges or load cells to assess structural integrity or mechanical performance.
- Sound: Captured via microphones to analyze noise levels or sound frequencies.
- Light intensity: Measured with photodiodes or light sensors for various applications, including environmental monitoring.
What are the types of data acquisition?
Data acquisition systems can be classified based on their functionality and the method of data collection:
- PC-based DAQ: Utilizes the processing power, display, and connectivity of personal computers with DAQ hardware for data collection and analysis.
- Standalone or portable DAQ: Independent systems that can operate without a PC, often used for field measurements or when portability is required.
- Networked DAQ: Systems connected over a network, allowing for remote monitoring and control across multiple locations.
- Modular DAQ: Systems that can be customized with different modules for various types of inputs and outputs to meet specific application requirements.
What is the DAQ process?
The DAQ process typically involves several key steps:
- Signal Conditioning: Modifying the raw signal from the sensor to make it suitable for digitization. This may include amplification, filtering, and isolation to ensure accurate measurements.
- Sampling: The act of measuring the signal at discrete intervals to convert the continuous analog signal into a series of digital values. The rate of sampling is crucial for accurately representing the signal.
- Analog-to-Digital Conversion (ADC): The conditioned analog signal is converted into a digital format by the ADC. The resolution of the ADC affects the precision of the measurement.
- Data Storage and Analysis: The digital data is then stored and analyzed using specialized software to understand the measured phenomena and make informed decisions.
- Feedback/Control: In many applications, the analyzed data can be used to make adjustments or control a process, creating a closed-loop system for automation and optimization.