Testing Battery Cells, Modules and Packs with a Single Instrument
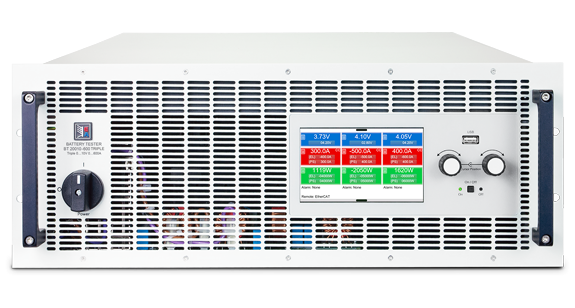
Battery technology continues to evolve, providing powerful energy solutions for various applications, from portable electronics to electric vehicles. However, ensuring the reliability and safety of batteries through testing is no easy feat. Battery test engineers encounter numerous challenges, such as the need for accurate data, adaptable test systems and space limitations in production facilities. To address these challenges, EA has introduced the EA-BT 20000 Triple Battery Tester, a groundbreaking all-in-one test system designed to revolutionize how engineers can conduct EV battery testing.
Here are some of the different areas we’ll explore:
- High-performance cell testing
- Safe module battery testing
- High voltage EV battery pack testing
- Building a battery test infrastructure
- Safety and automation in EV battery testing
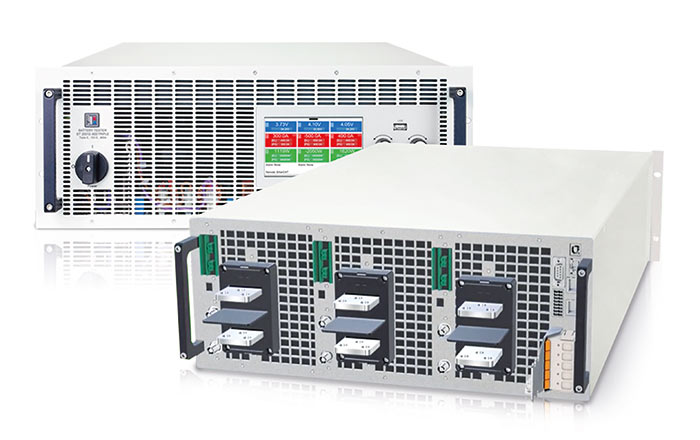
High-performance cell testing
Rapid response time is crucial when testing individual cells. Lithium-ion batteries are known for handling near-instantaneous load changes, making them suitable for quick power delivery applications. The EA-BT 20000 stands out by offering the capability to create 1 ms changes in the load current draw. This feature allows for precise measurement of a cell’s dynamic response to fast load changes, which is often essential in real-world applications.
Moreover, the EA-BT 20000 provides control full current, even at low voltages. It can handle voltages as low as 2 V, ensuring that individual cells are tested accurately, even in high-power battery packs.
Safe module battery testing
To ensure safe module testing, the EA-BT 20000 incorporates a pre-charge function. This feature safeguards both the DC programmable power supply and the battery being tested. Without pre-charging, connecting a battery to the tester could result in power discharge, potentially damaging capacitors and causing sparks. The EA-BT 20000 mitigates these risks by pre-charging capacitors to match the battery’s voltage, ensuring safe and controlled testing conditions.
Additionally, the battery testing equipment instrument features internal polarity detection, preventing incorrect connections to the battery. This added layer of protection safeguards against reversed polarity, which can have catastrophic consequences in a testing environment.
High voltage battery pack testing
The rise of electric vehicles has led to the development of high-voltage battery packs. While most electric vehicle batteries operate in the range of 350 V to 450 V, some high-performance models utilize voltages of 800 V or higher. These higher voltage batteries enable faster charging, reduce cable weight, and cut cable costs. The EA-BT 20000 is equipped for battery testing high-voltages effectively.
Not only can it output voltages up to 920 V, but it can also compensate for voltage drops in long cable runs, ensuring accurate testing even in complex electric power delivery systems.
Triple the throughput
One of the most impressive aspects of the EA-BT 20000 is its ability to triple testing throughput. Unlike traditional battery test equipment that can only handle one device at a time, the EA-BT 20000 can simultaneously test three devices. This increased throughput reduces production costs and enhances testing capacity, a significant advantage in high-demand production environments such as rising EV battery testing.
Watch the BT 20000 video for more information and 360° views.
Energy and space savings
Cost efficiency is a crucial consideration in any testing environment. The EA-BT 20000 boasts an impressive energy-saving feature by returning up to 96% of absorbed energy to the grid during battery discharging. This energy recycling can lead to substantial utility cost savings, particularly when testing kW capacity battery packs during extended production runs.
Furthermore, the EA-BT 20000 is designed with a high-power density, allowing it to deliver up to 30 kW of power per device if the channels are connected in parallel. This space-saving design is a boon for test labs and production facilities where every inch of space is valuable.
Building a battery test infrastructure
To meet the needs of large-scale energy storage battery systems, multiple EA-BT 20000 units can be combined into racks, generating up to 240 kW of testing capacity. These racks can be paralleled for increased load sharing and safety, with up to eight fully loaded test racks providing an impressive 1.92 MW of testing power.
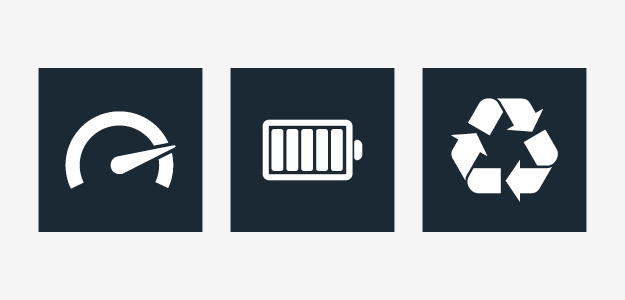
The BT 20000 has can do three high performance applications
Safety and automation in battery testing
Safety is paramount in battery testing, and the EA-BT 20000 offers multiple layers of protection. During battery testing, polarity detection, overvoltage protection, overcurrent protection, overpower protection, and overtemperature protection all work together to prevent damage to both the battery and the instrument. Warnings and alarms are generated if any parameter exceeds safe limits.
For automation, the EA-BT 20000 is equipped with various interfaces, including USB, Ethernet, EtherCAT, and CAN FD. This allows for seamless integration with both PCs and programmable logic controllers (PLCs). The instrument can be controlled using SCPI command control, LabView, and IVI drivers for PC control, while the ModBus command operation enables PLC control, offering flexibility for automated testing.
A comprehensive EV battery test solution
In conclusion, the EA-BT 20000 Triple Battery Tester is a remarkable advancement in battery testing technology. It offers a comprehensive DC programmable power solution for battery testing and simulation. It also provides a battery solution for recycling individual cells and high-power battery packs. With the ability to test voltages up to 920 V and currents up to 600 A/channel, this single instrument can handle many testing requirements. It increases throughput and saves energy and valuable lab and production floor space. The EA-BT 20000 is the all-in-one answer to the complex challenges faced by battery test engineers, promising a brighter and more efficient future for battery testing.
Learn more about battery cell testing in the complete App Note, Test Battery Cells, Modules and Packs with a Single Instrument. For more information on the EA-BT 20000 Triple Battery Tester, visit the BT 20000 webpage.
For all other inquires, please Contact Us for more information.