Digital multimeters seem common, but specialized versions perform tests you might not imagine, thereby improving productivity and lowering costs.
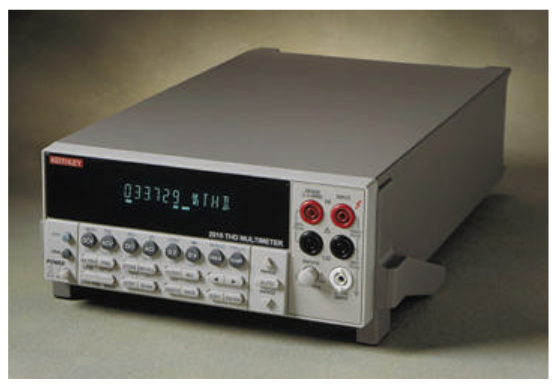
DMM Selection Factors
Digital multimeters (DMMs) have for years been a quality assurance test tool used by wireless device manufacturers. However, DMM performance has steadily improved and you can now get functions never imagined on these instruments. For example, you can now buy benchtop DMMs with basic one-year accuracy ranging from 0.0006% to 0.03%, resolution from 4-1/2 digits to 8-1/2 digits and sensitivity from 1nV to 10mV. For audio circuit and component testing, total harmonic distortion (THD) can be measured with some specialized DMMs.
While accuracy, resolution and sensitivity are important factors in DMM selection, you should look at speed, specialized functions and productivity enhancements for added value, especially if you do production testing Also, certain features can help overcome external noise problems that would otherwise nullify the underlying accuracy and sensitivity of a DMM. Major selection factors include measurement variables, range, accuracy, resolution, sensitivity, speed, filters, test current limiting in resistance measurements, 2-wire vs. 4-wire measurements, triggering, number of measurement channels and cost.
Ten Steps to DMM Selection
Selecting and configuring a DMM requires preliminary analysis in two broad areas - the device under test (DUT) and the test environment. The analysis can be conducted by asking yourself 10 key questions on measurement functions and performance requirements, and then evaluating how the DMM fits into your test environment. See Figure 2.
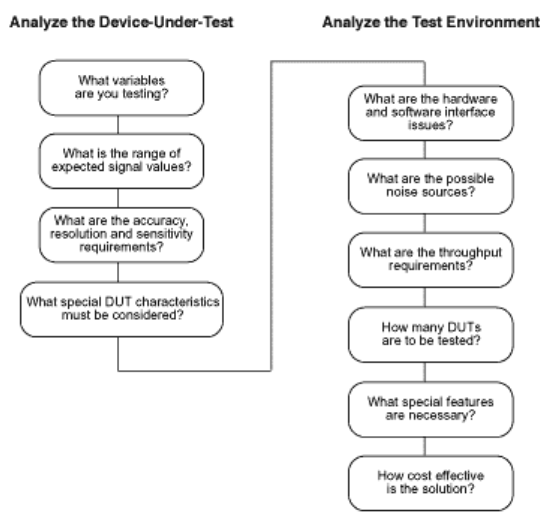
While going through the 10-step analysis in Figure 2, keep the following questions in mind: Does the DMM meet or exceed the requirements for your application? Is the DMM going to easily integrate with your test setup? Does it have a feature that no other DMM has to cut your test time? Answers to these questions are sometimes obvious in an instrument's data sheet, but at other times may require a careful reading of the fine print in instrument specifications.
1. What variables are you testing?
First, analyze the DUT and required measurements. What are the signal characteristics and what data need to be collected?
The typical five-function DMM measures DC and AC volts, DC and AC current and two-wire ohms. Additional functions in some DMMs may include true RMS measurements, four-wire ohms testing, temperature readings with a thermocouple (T/C) or resistance temperature detector (RTD), dB and dBm, frequency and period, audio signal distortion, capacitance, inductance, and checking diodes. Specific industries may want even more specialized functions.
For example, wireless device manufacturers have often been dissatisfied with paying for lab instrument features they might not need to do THD analysis. At the same time, they have wanted a DMM offering not only speed but compactness as well. In response to the former, THD meters were introduced. Keithley Instruments went a step further by producing its Model 2015 Total Harmonic Distortion Multimeter, a half-rack instrument combining audio band quality measurements with a full-function 6-1/2-digit DMM. It can measure THD over a wide band (20Hz25kHz), including the audio band. It accommodates a wide input range (0.1µV-750V RMS) and has low residual distortion (-94dB). Additionally, this instrument can compute THD+Noise and Signal-to-Noise plus Distortion (SINAD).
Specialized features such as these translate into higher throughput and productivity, especially when the instrument design addresses production testing issues. For instance, the Keithley THD Multimeter can execute a single sweep of frequencies and transmit both RMS voltage readings and THD readings to a computer in only 1.1 seconds. This allows high speed audio performance testing of high volume devices, such as a cellular phones. Thus, THD testing can be done without reducing the number of other tests performed or reducing the number of measurements in each test.
Audio distortion testing can reveal a variety of underlying problems on a production line. Some of the more important ones are:
- Wrong components installed
- Polarized components installed backwards
- Bad solder joints
- Speaker coils rubbing against the magnet
A typical test setup is shown in Figure 3.
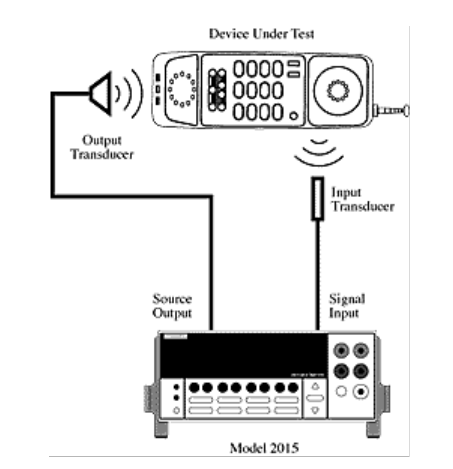
2. What is the range of expected signal values?
For more conventional testing, the DMM must have a wider measurement range than the expected minimum and maximum test signals. At the low end, pay attention to the DC noise specification. If the noise floor is higher than the signal to be measured, you have to slow down measurements to employ noise reduction techniques, or chose a DMM with a lower measurement range and noise. Speed and accuracy compromises are discussed later in this article. At the high end, the maximum allowable input might include specifications for a volt-hertz product limitation or a time limit on AC signals. Make sure these restrictions on AC measurements are acceptable.
Some DMMs have an overrange specification stated as a percentage of range, typically 120% on all but the top range. If this extra 20% allows you to use a fixed range instead of autoranging, faster measurements are possible.
For floating measurements, consider the DMM's common-mode voltage specification, the maximum voltage between the low input terminal and ground. For example, with 500V between high and low input terminals, and another 500V between low input and ground, the common-mode voltage specification must be at least 1000V.
3. The big three: accuracy, resolution and sensitivity
These three factors define DMM performance more than any others. DMM manufacturers typically have a family of instruments with family members having progressively higher performance specifications along with higher prices.
Accuracy is the degree of conformity of a measurement to a standard or true value. DMM accuracy is usually specified as a percent of reading plus a percent of range (or a number of counts of the least significant digit). It may also be specified in parts per million (ppm), where 1ppm is the equivalent of 0.0001%. Accuracy is also specified over a period of time (for example 24 hours, 90 days, or 1 year) and within a temperature window (typically 1°C or 5°C around room temperature, with deratings for temperatures outside those ranges). AC performance typically is specified over a range of frequencies. Additional derating factors may apply for high voltage or current levels. Study the specifications carefully to see if these factors must be considered at the signal levels of your test.
Resolution is the smallest portion of a signal that can be measured or displayed, for example, one digit out of 20,000 on a 4-1/2-digit display. The resolution of the display is the ratio of the smallest count to the maximum count - 1/20,000 or 0.005% for a 4-1/2-digit display. A 6-1/2-digit DMM provides a resolution of 1/2,000,000 or 0.00005%. On the 100mV range, that amounts to 50nV.
Sensitivity is the smallest change of the measured signal that can be detected. It depends on both resolution and the lowest measurement range of the instrument. For example, the sensitivity of a 5-1/2-digit DMM on the 200mV range is 1mV. (On a 200mV display reading 200,000, the last zero is the one microvolt digit.)
4. What DUT characteristics are important?
Is your DUT a high impedance device? Then a DMM may not be the best solution to test it. A sidebar article discusses instruments that may be more suitable for testing those devices. Is your DUT susceptible to selfheating from the test current on ohms ranges? If so, the ability to control test current on each range is important. Also, for contact resistance measurements, dry circuit testing may be necessary, which limits test voltage to prevent disturbance of oxidation on the contacts. Carefully review the DMM's specifications to make sure it has functions that support all your requirements.
5. What are the hardware and software interface issues?
Obviously, the DMM must work with the line voltage and frequency where you are conducting tests. However, if you standardize on an instrument model to be used in different countries, it should support other power standards. A universal power supply that automatically senses voltage and frequency will avoid problems that could arise if a DMM power switch must be manually set. You may also want a battery option for portable applications. Also check the power consumption (VA rating) - you may need additional cooling in equipment racks.
Is this a stand-alone application or does the DMM need data communication ports? For instance, in the case of a THD Multimeter, you will probably want to send numerical values for THD, THD+N and SINAD to a host computer over a GPIB bus or RS-232 connection for PASS/FAIL processing.
Another question: Is the DMM going to replace older test equipment? If so, it may need to fit into existing rack space.
How will the DUT be connected into the test system? Is there a test fixture? DMMs typically have banana jacks and a variety of test lead terminators, like alligator clips and spade lugs. Are those sufficient or will adapters be necessary? Are safety test leads and special probes available for high voltage signals?
Regarding software issues, what programming languages or drivers are supported? Will a new command set have to be learned? Some DMMs can emulate the command sets of other multimeters. This might eliminate the need to revise test programs and makes drop-in replacements that much easier.
6. What are the noise sources?
Common types of electrical noise that instruments must contend with in industrial environments are power line noise and random noise, like fluorescent lights and microprocessor clocks. Within a switching system, relay contact bounce and high voltage arcing might also be present. How susceptible is the DMM to these noise sources? A DMM's specifications for normal mode rejection ratio (NMRR) and common mode rejection ratio
(CMRR) indicate its noise susceptibility. Typical values for NMRR and CMRR are >60dB and >120dB respectively.
As discussed, configuring the DMM's signal integration period to be an integer multiple of power line cycles reduces power line noise. Digital filtering helps average out random noise from the measurements.
How much noise does the DMM emanate? This is especially critical when measuring low signal levels. Look for compliance to common EMI standards, including the European Union Directive 89/336/EEC, FCC part 15 class B and IEC 801-2.
7. What are the throughput requirements?
Measurement speed is important in many test situations, especially production environments since it is a major determinant of throughput. Speed is usually stated as readings per second for a set of operating conditions. These conditions may include:
- Measurement resolution - A 4-1/2-digit reading is acquired faster than a 7 -1/2-digit reading. Only use as much resolution as you need. Some DMMs have programmable resolutions, which allows tradeoffs between speed and accuracy.
- Integration period - This is the window of time a signal is sampled by the A/D converter. It is often expressed in number of power line cycles (NPLCs), where 1PLC for 60Hz is 16.67ms and 1PLC for 50Hz is 20ms. NPLCs that are integer multiples (1, 5, 10, etc.) can reduce the most common type of normal mode noise, that of 50/60Hz line pickup. The larger the value of N, the greater the line noise reduction but the longer the measurement takes.
- Digital filtering - This is the quantity of A/D conversions averaged for each reading. It could be up to 100 conversions. Filtering stabilizes noisy readings but slows down measurements. The flexibility of programmable filtering can help reach a compromise between speed and accuracy.
- Autozeroing - When this function is activated, the DMM measures internal voltages to maintain stability and accuracy as temperature changes over time. How often this is performed affects the reading rate. It may be possible to disable this function, or just perform an periodically, or program the DMM to do it during the test fixture's unload/load cycle. Such test program changes can increase throughput.
Besides reading rates, there are other speed specifications to be considered when deriving system throughput. Among them are range changing rate and autorange time. Since changing ranges increases testing time, it is advantageous to stay on a fixed range. Check the specifications to see if the resolution and accuracy of a single range is sufficient. For multiple tests on a DUT, the function changing rate might be a throughput concern.
Also, what is the trigger latency? Hardware triggers are typically faster than software triggers. Some DMMs have a special microprocessor just to handle triggers. This shortens trigger latency considerably.
Settling time (or response time) is another speed specification to be considered. For a measuring instrument, settling time is the time between an input signal change and indication of that change at a rated accuracy. Settling time is more an issue when testing high impedance devices.
8. How many DUTs are to be tested?
A device may have several test points or there may be several devices to test. In either case, using relays to switch the signals eliminates moving test leads. Switching is particularly useful in a production test environment where hundreds or thousands of devices must be tested each work shift.
The switching can take place inside the DMM if it has an optional relay card, which typically expands the number of measurement channels to 10 or 20. Otherwise, an external switching system mainframe may be required. Internal switching is usually limited to general purpose signals but external switching can handle most any type and level of signal that a DMM is capable of measuring. In any case, there is some signal degradation and additional settling time delays created by the relays or mainframe. Regardless of where the switch card resides, these factors affect low-level signals unless the type of relay card and system connections are chosen carefully. One advantage of using DMMs with internal switch card slots is simplified, less costly system integration.
9. Would additional DMM features be helpful?
To differentiate their product offerings, manufacturers regularly add new functions and features to DMMs. This especially benefits production test systems, where rack space is at a premium. Some features to look for include:
- Faster and simpler hardware triggering to reduce testing time.
- An internal buffer for storing data. It is faster to let a DMM store data and send the readings all at once rather than send single readings to the computer.
- Stored setups for function and range changing. This quickly sets up a DMM for different tests or different devices, and speeds up testing by minimizing external data bus traffic between a GPIB instrument and the PC controller.
- Measurement limit testing and digital I/O for simple binning of DUTs. For example, a DMM with two sets of limits and a strobe signal can sort resistors into tolerance bands without GPIB controller intervention.
10. How cost effective is the solution?
In addition to the purchase price, there are other factors to consider when determining cost of ownership. Start-up costs, including programming, system integration and training, might be a large factor. Are the software libraries and drivers included with the instrument sufficient to get the unit up and running or will additional software be required? However, there may be an opportunity to offset these cost items with a faster DMM that increases test throughput.
There also are longer-term costs for maintenance. These are associated with calibration intervals and necessary calibration equipment. Or will the DMM be sent to the manufacturer for calibrating? Will it be necessary to purchase spare units to reduce production line downtime? How long is the warranty? All of these factors affect cost of ownership.
One additional step
After completing this 10-step process to narrow your DMM choices to two or three models, one additional step is suggested. Call the applications department at the instrument manufacturers. Discuss your measurement needs with people who make product recommendations every day. They can verify your selection or point out a test parameter that might lead you in a different direction. In either case, after completing this evaluation of your requirements, you can make an informed and cost-effective purchasing decision.
When a DMM Is Not the Best Solution
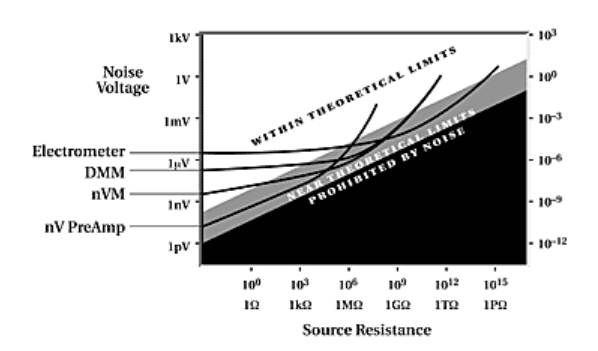
A wide range of accuracy, resolution, speed, and features are available in DMMs. If one of these meets all your test requirements, then it may well be the most cost-effective solution. Generally, DMMs are adequate if the source resistance is 1M ohm or less, or if the desired resolution is no better than 0.1mV (with low source resistance). For low-level signals or high source resistances, more specialized instruments are needed.
Nanovoltmeters are voltage-measuring instruments that are at least a decade more sensitive than DMMs. Standard deviations between sets of averaged readings can be as low as a few nanovolts.
Electrometers are DC multimeters with input resistance up to 1016 ohms and input current down to 1017 amperes. Due to its low input current, an electrometer is better than a DMM or nanovoltmeter for making measurements on a high impedance signal source. Electrometers can also measure charge and resistance.
Picoammeters are used when only current needs to be measured. Their current sensitivity is better than a DMM but not as good as an electrometer. Both electrometers and picoammeters have much lower input voltage burden than a DMM. This lower voltage drop across the ammeter inputs (typically 200mV compared to a DMM's 200mV) results in less error at low current levels.
Micro-ohmmeters are specifically designed for low-level resistance measurements. The typical micro-ohmmeter can resolve resistances as low as 10m ohms. Measurements are always performed using the 4-wire (Kelvin) technique.
Source-Measure Units (SMUs) or Force-Meter Units (FMUs) combine four instruments (DMM, voltage source, current source, and electrometer) in one stand -alone enclosure. These instruments provide better speed, sensitivity, and accuracy when sourcing voltage and measuring current or sourcing current and measuring voltage. They are well suited for low-current applications
SourceMeters combine the functions of a DMM and current/voltage source with sweep capabilities. This integration makes for simple operation and high throughput. They are designed for general-purpose, high speed applications typical of those found in production testing. They can be used as sources for moderate to low-level measurements.
When features described above are required, along with THD measurement functions, then a wireless manufacturer may have little choice but to use separate instruments in the test setup.