Свяжитесь с нами
Живой чат с представителями Tektronix. С 9:00 до 17:00 CET
Позвоните нам
С 9:00 до 17:00 CET
Загрузить
Загрузить руководства, технические описания, программное обеспечение и т. д.:
Обратная связь
2470 Graphical SourceMeter SMU Instrument Datasheet
Дополнительные сведения
- Графические источники-измерители (SMU) серии 2400
- Поддержка приборов
- Explore more Software models
Читать на веб-сайте:
The 2470 High Voltage SourceMeter® Source Measure Unit (SMU) Instrument brings advanced Touch, Test, Invent® technology right to your fingertips. It combines an innovative graphical user interface (GUI) with capacitive touchscreen technology to make testing intuitive and minimize the learning curve to help engineers and scientists learn faster, work smarter, and invent easier. With its 1100 V and 10 fA capability, the 2470 is optimized for characterizing and testing high voltage, low leakage devices, materials, and modules, such as silicon carbide (SiC), gallium nitride (GaN), power MOSFETs, transient suppression devices, circuit protection devices, power modules, batteries, and much more. These new capabilities, combined with Keithley’s decades of expertise in developing high precision, high-accuracy SMU instruments, make the 2470 a “go-to instrument” for high-voltage source and low-current measurement applications in the lab and in the test rack.
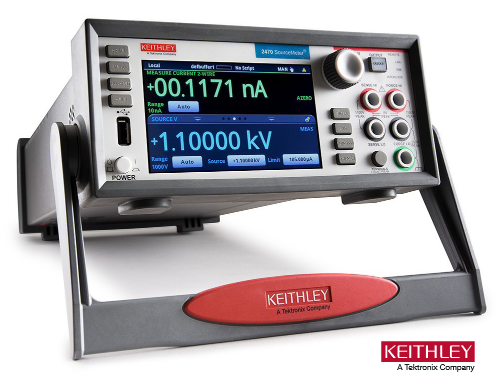
Key Features
- Wide coverage up to 1100 V / 1 A DC 20 W max.
- 10 fA measure resolution
- 0.012% basic measure accuracy with 6½-digit resolution
- Five-inch, high resolution capacitive touch screen GUI
- Source and sink (4-quadrant) operation
- SCPI and TSP® scripting programming modes
- TSP-Link for multi-channel I-V testing
- Front panel input banana jacks; rear panel high-voltage input triaxial connections
- Built-in context-sensitive help
- Front-panel USB 2.0 memory I/O port for transferring data, test scripts, and test configurations
Learn Faster; Work Smarter;Invent Easier
The 2470 features a five-inch, full-color, high resolution touchscreen that supports intuitive operation, helps operators become familiar with the instrument quickly, and optimizes overall speed and productivity. A simple icon-based menu structure reduces the number of steps required to configure a test by as much as 50 percent and eliminates the cumbersome multi-layer menu structures typically used on soft-key instruments. Built-in, contextsensitive help supports intuitive operation and minimizes the need to review a separate manual. These capabilities, combined with the 2470’s high versatility, simplify its operation in both basic and advanced measurement applications, regardless of the user’s previous experience in working with SMU instruments.

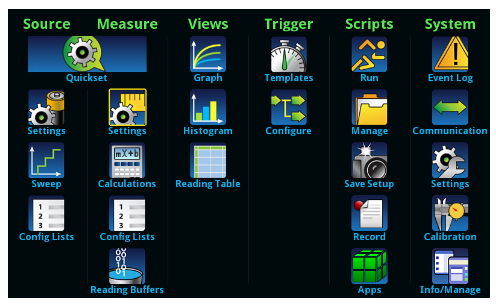
All-in-One SMU Instrument
The 2470, Keithley’s fourth generation of SourceMeter SMUs, leverages the proven capabilities of the original 2410 High Voltage SourceMeter SMU Instrument. SMU instruments offer a highly flexible, four-quadrant voltage and current source/load coupled with precision voltage and current measurements. This all-in-one instrument has the capabilities of a:
- Precision power supply with V and I readback
- True current source
- Digital multimeter (DCV, DCI, ohms, and power with 6½-digit resolution)
- Precision electronic load
- Trigger controller
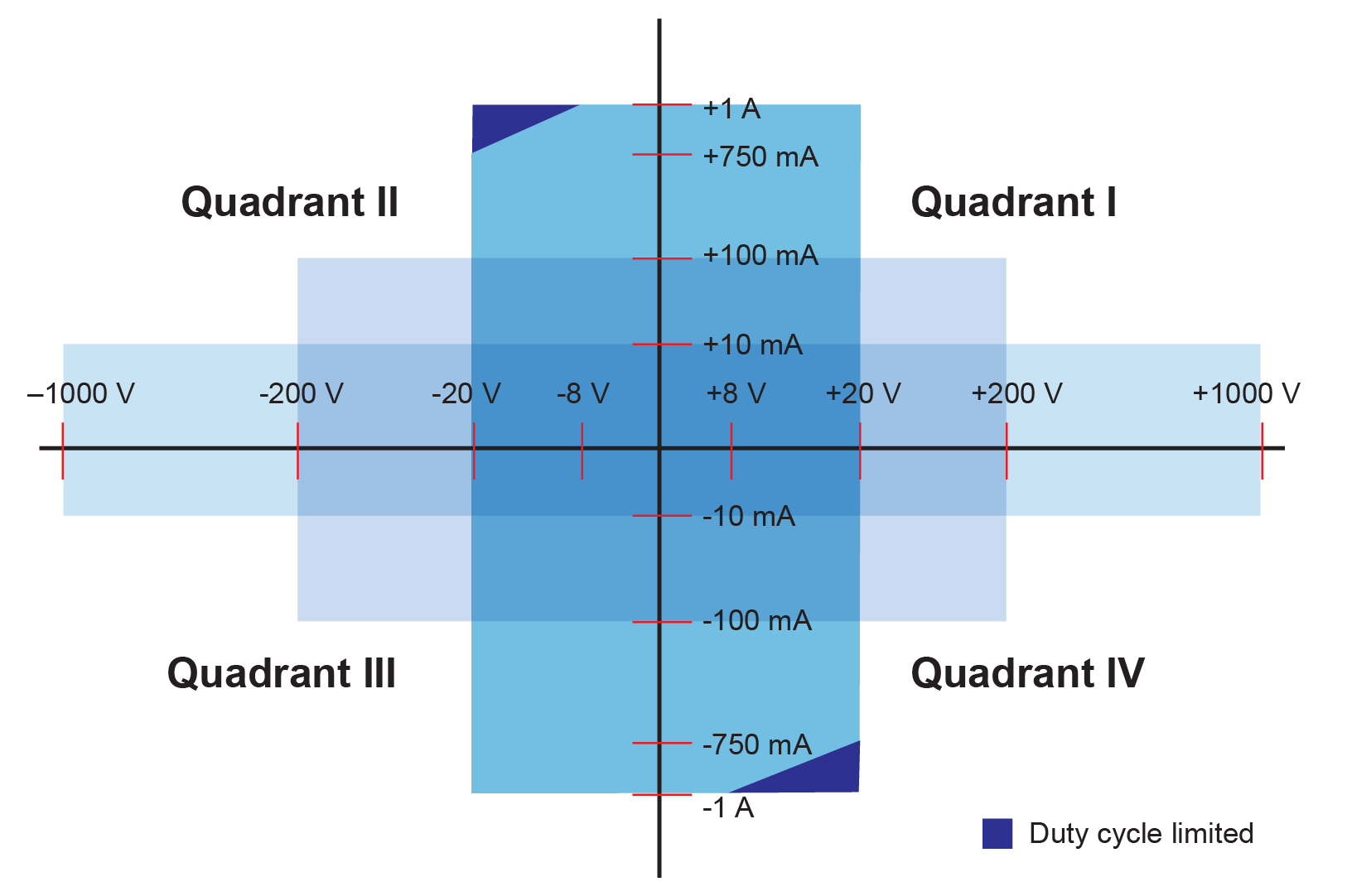
Ease of Use Beyond the Touchscreen
In addition to its five-inch color touchscreen, the 2470 front panel offers a variety of features that enhance its speed, user-friendliness, and learnability, including a USB 2.0 memory I/O port, a HELP key, a rotary navigation/control knob, a front/rear input terminal selector button, and banana jacks for basic bench applications. The USB 2.0 memory port simplifies storing test results and instrument configurations, uploading test scripts into the instrument, and installing system upgrades. All front-panel buttons are backlit to enhance visibility in low-light environments.

Four Quick Setup modes simplify instrument setup. With one touch, the instrument can be quickly configured for various operating modes without the need to configure the instrument indirectly for this operation.
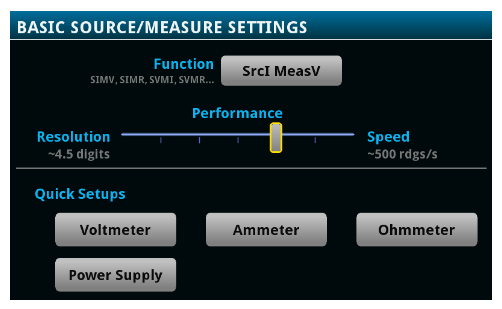
Comprehensive Built-in Connectivity
Rear panel access to rear-input connectors, remote control interfaces (GPIB, USB 2.0, and LXI/Ethernet), a D-sub 9-pin digital I/O port (for internal/external trigger signals and handler control), instrument interlock connector, and TSP-Link® connectors make it simple to configure multiple instrument test solutions and eliminate the need to invest in additional adapter accessories.
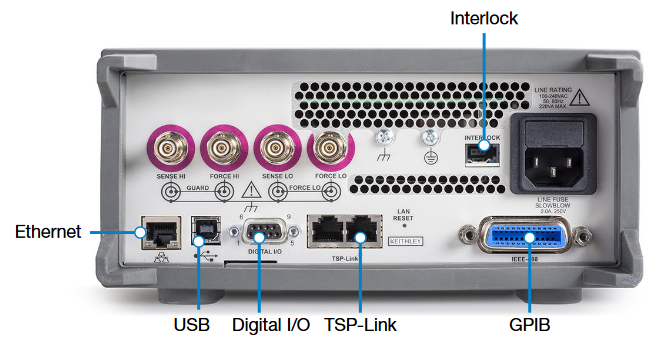
Convert Raw Data to Information
A full graphical plotting window converts raw data and displays it immediately as useful information, such as semiconductor I-V curves and waveforms. Using the 2470’s Sheet view, test data can also be displayed in tabular form. The instrument supports exporting data to a spreadsheet for further analysis, dramatically improving productivity for research, benchtop testing, device qualification, and debugging.

TriggerFlow® Building Blocks for Instrument Control and Execution
The 2470 incorporates Keithley’s TriggerFlow triggering system, which provides user control of instrument execution. TriggerFlow diagrams are created in much the same way that flow charts are developed, using four building blocks:
- Wait – Waits for an event to occur before the flow continues
- Branch – Branches when a condition has been satisfied
- Action – Initiates an action in the instrument, for example, measure, source, delay, set digital I/O, etc.
- Notify – Notifies other equipment that an event has occurred

A TriggerFlow model using a combination of these building blocks can be created from the front panel or by sending remote commands. With the TriggerFlow system, users can build triggering models from very simple to complex with up to 63 block levels. The 2470 also includes basic triggering functions, including immediate, timer, and manual triggering.
Unmatched System Integration and Programming Flexibility
When a 2470 is configured into a multi-channel I-V test system, its embedded Test Script Processor (TSP®) allows it to run test scripts, so users can create powerful measurement applications with significantly-reduced development times. TSP technology also offers channel expansion without a mainframe. Keithley’s TSP-Link® channel expansion bus can connect multiple 2470s and other TSP instruments, including Keithley’s other graphical SourceMeter instruments (2450, 2460, 2461), Keithley’s DMM7510, DMM6500, and DAQ6510 graphical multimeters, Series 2600B System SourceMeter SMU instruments, and Series 3700A Switch/Multimeter systems, in a master-subordinate configuration that operates as one integrated system. The TSP-Link expansion bus supports up to 32 units per GPIB or IP address, making it easy to scale a system to fit an application’s particular requirements.
Parallel Test Capability
The TSP technology in the 2470 supports testing multiple devices in parallel to meet the needs of device research, advanced semiconductor lab applications, and even high throughput production test. This parallel testing capability allows each instrument in the system to run its own complete test sequence, creating a fully multi-threaded test environment. The number of tests that can be run in parallel on a graphical SourceMeter can be as high as the number of instruments in the system.
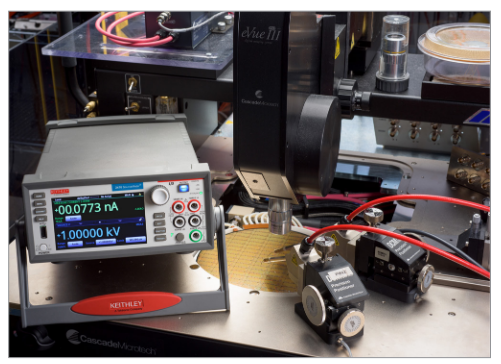

Typical Applications
Ideal for current/voltage characterization and functional test of a wide range of today’s modern electronics and devices, including:
- Devices
- – Power semiconductors and materials: SiC,GaN, power MOSFETs, power diodes
- – IGBT
- – Thyristors, SCRs
- – Transient suppression devices
- – Circuit protection devices: TVS, MOVs,fuses, etc.
- – Connectors, switches, relays
- – Power management modules
- – Batteries
- Tests
- – I-V characterization
- – Forward voltage
- – Breakdown voltage
- – Leakage current
- – Isolation
- – Hi-Pot
- – Dielectric withstanding
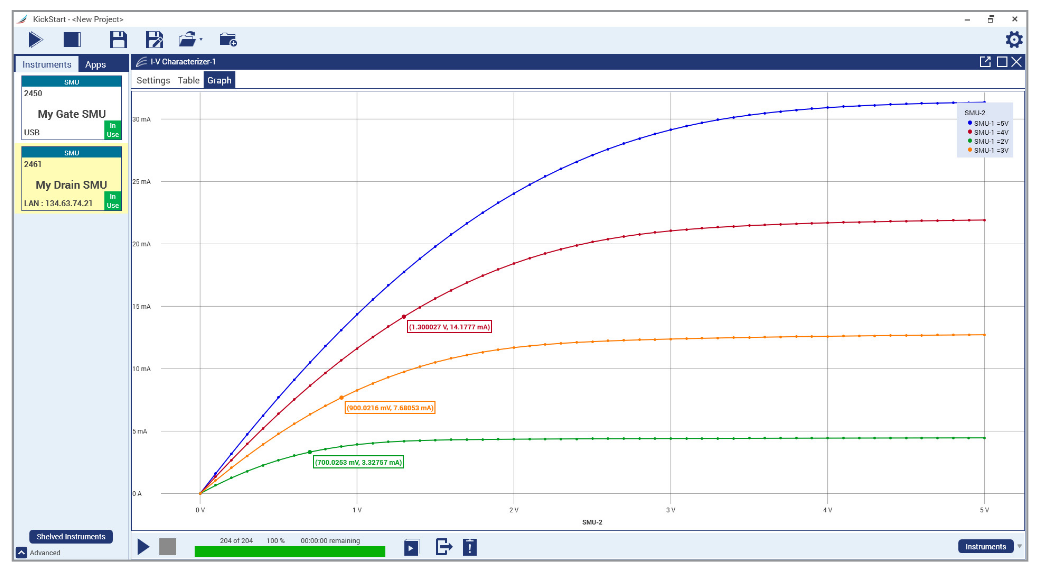
Instrument Control Start-up Software
KickStart instrument control/start-up software enables users to start making measurements in minutes withoutprogramming. In most cases, users merely need to make some quick measurements, graph the data, and store the data to disk for later analysis in software environments such as Excel. KickStart offers:
- Configure and control up to four SMU instruments for DC or Pulsed I-V test in either the same app, same project, or a combination of the two.
- Create tests by mixing any of these SMU instruments:2400 Graphical Series, 2400 Standard Series (DC only), 2600B Series, 2651A, 2657A, and 6430 SourceMeter®SMU (DC only) instruments.
- Differentiate SMU instrument channels and their measurement data using labels that are relevant to your device or module.
- Native X-Y graphing, panning, and zooming; screenshot capturing of graphs.
- Spreadsheet/tabular viewing of data; export data for further analysis.
- Annotating of tests; save test setups.
- GPIB, USB 2.0, Ethernet compliance.
Optional Apps Tailored for your Characterization Needs
The 2470 is an excellent tool to define nearly any DC test you choose for characterizing materials, electronic devices and modules. For more specific needs, Keithley offers oninstrument software apps that alter the 2470’s behavior, fitting your instrument to your needs. These apps can be installed directly to your 2470 by connecting to Keithley’s KickStart instrument control software and opening the relevant app in KickStart.
I-V Tracer App
Curve tracing analysis is a critical task for many users in the semiconductor development supply chain. Engineers and technicians both hold the traditional curve tracer as the simplest, fastest method for generating characteristic I-V curves on a device. They are heavily used by engineers in failure analysis and incoming inspection to qualify parts, identify counterfeit devices, and to quickly identify the location of a failure on damaged devices. SMUs have typically been limited to predefined sweeps with longer set up times than curve tracers — until I-V Tracer.
Keithley’s I-V Tracer app leverages the touchscreen and front-panel knob of the 2470 to allow precise, live control over the SMU output while viewing I-V results of 2 terminal devices. At each individual output level current and voltage are measured and plotted. The small footprint of the SMU enables portable bench top use, reserving high power (kW) traditional curve tracers for special cases. The power envelope of the 2470 allows it to comfortably operate in the low power range of traditional curve tracers like the Tektronix 576 and Tektronix 370A, while offering enhanced low current measurements.

Once installed, I-V Tracer exists on the SMU itself, meaning I-V tracer can be used wherever your SMU can go, without a continuous remote connection. It can also integrate with KickStart to enable simple data collection and comparison on the PC, simplifying the preparation of reports used in failure analysis or teaching labs at colleges and universities.
I-V Tracer capabilities with the 2470:
- Use the full power envelope of the 2470 (max 1000 V or 1 A)
- 1000 V range allows careful tracing into reverse breakdown behavior
- Trace by sourcing voltage or current, positive or negative
- 2 or 4-wire sense
- Compare mode for verifying against a reference device
- Reading table view to see exact measurements
- Easily copy curves and settings to your PC with KickStart
Simplified Programming with Ready-to-Use Instrument Drivers
For those who prefer to create their own customized application software, native National Instruments LabVIEW® drivers, and IVI-C and IVICOM drivers are available at tek.com/keithley
Voltage Specifications1, 2,
Source | Measure3 | |||||
Range4 | Resolution | Accuracy5 23 °C ± 5 °C, 1 Year ±(% setting + volts) |
Noise (RMS)<10 Hz | Resolution | Input Resistance | Accuracy 23 °C ± 5 °C, 1 Year ±(% reading + volts) |
200.0000 mV | 5 µV | 0.015% + 200 µV | 2 µV | 100 nV | > 10 GΩ | 0.012% + 200 µV |
2.000000 V | 50 µV | 0.020% + 300 µV | 10 µV | 1 µV | > 10 GΩ | 0.012% + 300 µV |
20.00000 V | 500 µV | 0.015% + 2.4 mV | 100 µV | 10 µV | > 10 GΩ | 0.015% + 1 mV |
200.0000 V | 5 mV | 0.015% + 24 mV | 1 mV | 100 µV | > 10 GΩ | 0.015% + 10 mV |
1000.000 V | 50 mV | 0.02% + 100 mV | 20 mV | 10 mV | > 10 GΩ | 0.015% + 50 mV |
Temperature Coefficient 20 V and 1000 V ranges: ± (0.15 × accuracy specification)/°C, 0 °C to 18 °C and 28 °C to 50 °C
200 mV and 2 V ranges: ±(0.30 x accuracy specification)/°C, 0 °C to 18 °C and 28 °C to 50 °C
Current Specifications1, 2
Source | Measure3 | |||||
Range4 | Resolution | Accuracy523 °C ± 5 °C, 1 Year ±(% setting + amps) |
Noise (RMS)<10 Hz | Resolution | Voltage Burden | Accuracy23 °C ± 5 °C, 1 Year ±(% reading + amps) |
10.00000 nA6 | 500 fA | 0.100% + 200 pA | 500 fA | 10 fA | <100 µV | 0.10% + 250 pA |
100.0000 nA6 | 5 pA | 0.060% + 250 pA | 500 fA | 100 fA | <100 µV | 0.060% + 300 pA |
1.000000 μA | 50 pA | 0.025% + 400 pA | 5 pA | 1 pA | < 100 µV | 0.025% + 300 pA |
10.00000 μA | 500 pA | 0.025% + 1.5 nA | 40 pA | 10 pA | <100 µV | 0.025% + 700 pA |
100.0000 μA | 5 nA | 0.020% + 15 nA | 400 pA | 100 pA | <100 µV | 0.02% + 6 nA |
1.000000 mA | 50 nA | 0.020% + 150 nA | 5 nA | 1 nA | <100 µV | 0.02% + 60 nA |
10.00000 mA | 500 nA | 0.020% + 1.5 μA | 40 nA | 10 nA | <100 µV | 0.02% + 600 nA |
100.0000 mA | 5 μA | 0.025% + 15 μA | 100 nA | 100 nA | <100 µV | 0.025% + 6 μA |
1.000000 A | 50 μA | 0.067% + 900 μA | 10 μA | 1 μA | <100 µV | 0.03% + 500 μA |
Temperature Coefficient ± (0.15 × accuracy specification)/°C, 0 °C to 18 °C and 28 °C to 50 °C
Notes
1. Speed = 1 PLC.
2. All specifications are guaranteed with output ON.
3. Accuracies apply to 2-wire and 4-wire modes when properly zeroed. For the 200 mV and 1 A ranges, the voltage burden may exceed the specification in 2-wire mode.
4. Maximum display and programming ranges are 5% overrange for voltage, except for the 1000 V range, which is 10% overrange (1100 V), and 5% overrange for current (for example,1.05 A on the 1 A range).
5. For sink mode, 1 µA to 100 mA range, accuracy is ±(0.5% + offset × 3). For 1 A range, accuracy ± (0.15% x accuracy specification))/°C on 20 V and 1000 V ranges ±(1.5% + offset × 3) .
6. Rear-panel triaxial connections only
Resistance Measurement Accuracy (Local Or Remote Sense)7, 8, 9
Range | Default Resolution10 | Default Test Current | Normal Accuracy 23 °C ± 5 °C, 1 Year ± (% reading + ohms) |
Enhanced Accuracy11 23 °C ± 5 °C, 1 Year ± (% reading + ohms) |
< 2.000000 Ω12 | 1 µΩ | User-defined | Source IACC+ Meas VACC | Meas IACC + Meas VACC |
20.00000 Ω | 10 µΩ | 100 mA | 0.098% + 0.003 Ω | 0.073% + 0.001 Ω |
200.0000 Ω | 100 µΩ | 10 mA | 0.077% + 0.03 Ω | 0.053% + 0.01 Ω |
2.000000 kΩ | 1 mΩ | 1 mA | 0.066% + 0.3 Ω | 0.045% + 0.1 Ω |
20.00000 kΩ | 10 mΩ | 100 µA | 0.063% + 3 Ω | 0.043% + 1 Ω |
200.0000 kΩ | 100 mΩ | 10 µA | 0.065% + 30 Ω | 0.046% + 10 Ω |
2.000000 MΩ | 1 Ω | 1 µA | 0.11% + 300 Ω | 0.049% + 100 Ω |
20.00000 MΩ | 10 Ω | 1 µA | 0.11% + 1 kΩ | 0.052% + 500 Ω |
200.0000 MΩ 13 | 100 Ω | 100 nA | 0.655% + 10 kΩ | 0.349% + 5 kΩ |
>200.0000 MΩ12, 13 | - | User-defined | Source IACC+ Meas VACC | Meas IACC+ Meas VACC |
Temperature Coefficient | ± (0.15 × accuracy specification)/°C 0 °C to 18 °C and 28 °C to 50 °C |
Source Current, Measure Resistance Mode | Total uncertainty = I source accuracy + V measure accuracy (4-wire remote sense) |
Source Voltage, Measure Resistance Mode | Total uncertainty = V source accuracy + I measure accuracy (4-wire remote sense) |
Guard Output Impedance | ≥ 300 Ω typical |
Notes
7. Speed = 1 PLC.
8. All specifications are guaranteed with output ON.
9. Accuracies apply to 2-wire and 4-wire modes when properly zeroed.
10. Measure resolution 6.5 digits.
11. Source readback enabled; offset compensation on.
12. Source current, measure resistance or source voltage, measure resistance only.
13. Rear-panel triaxial connections only.
Supplemental Specifications
Overrange | 105% of range for 200 mV to 200 V, source and measure ranges; 110% of range for 1000 V, source and measure ranges | ||||||||||||
Regulation | |||||||||||||
Voltage | Line: 0.01% of range Load: 0.01% of range + 100 µV |
||||||||||||
Current | Line: 0.01% of range Load: 0.01% of range + 100 pA |
||||||||||||
Source Limits | |||||||||||||
Voltage Source Current Limit | Bipolar current limit set with a single value Minimum value is 10% of range |
||||||||||||
Current Source Voltage Limit | Bipolar voltage limit set with a single value Minimum value is 10% of range |
||||||||||||
Voltage Limit/Current Limit Accuracy | Add 0.3% of range and ±0.02% of reading to base specification | ||||||||||||
Overshoot | |||||||||||||
Voltage Source | <0.1% typical Step size = Full scale, resistive load, 20 V range, 10 mA current limit |
||||||||||||
Current Source | <0.1% typical Step size = Full scale, resistive load of 10 kΩ, 1 mA range, 20 V voltage limit |
||||||||||||
Range Change Overshoot | Overshoot into a fully resistive 100 kΩ load, 10 Hz to 20 MHz bandwidth, adjacent ranges: 250 mV typical | ||||||||||||
Output Settling Time | Time required to reach 0.1% of final value after command is processed and output slew: 20 V range,100 mA current limit: < 200 µs typical | ||||||||||||
Maximum Slew Rate14 | 0.2 V/µs, 200 V range, 100 mA limit into a 2 kΩ load (typical) 0.5 V/µs, 1000 V range, 10 mA limit into a 100 kΩ load (typical) |
||||||||||||
Overvoltage Protection | User-selectable values, 10% tolerance; factory default = none | ||||||||||||
Voltage Source Noise | 10 Hz to 20 MHz (RMS): 4 mV typical into a resistive load | ||||||||||||
Common Mode Voltage | 250 V DC | ||||||||||||
Common Mode Isolation | > 1 GΩ, < 1000 pF | ||||||||||||
Noise Rejection (typical) |
* Except lowest two current ranges ~90dB. |
||||||||||||
Load Impedance | |||||||||||||
Normal Mode | 20 nF typical |
||||||||||||
High-Capacitance Mode | Stable into 1 μF typical (specification only valid for ranges ≥100 μA) | ||||||||||||
Maximum Voltage Drop Between Force and Sense Terminals | 5 V | ||||||||||||
Maximum Sense Lead Resistance | 1 MΩ for rated accuracy | ||||||||||||
Sense Input Impedance | > 10 GΩ | ||||||||||||
Guard Offset Voltage | < 300 µV typical |
Notes
14. High capacitance mode off.
System Measurement Speeds15
Reading rates (readings per second) typical for 60 Hz (50 Hz), script (TSP) programmed
NPLC | Trigger Origin | Measure to Memory | Measure to GPIB | Measure to USB | Measure to LAN | Source Measure Sweep to Memory | Source measure sweep to GPIB | Source Measure Sweep to USB | Source Measure Sweep to LAN |
0.01 | Internal | 3150 (2800) | 2760 (2570) | 2825 (2570) | 2740 (2530) | 1710 (1620) | 1620 (1540) | 1630 (1540) | 1620 (1540) |
0.01 | External | 2170 (2050) | 2120 (2003) | 2170 (2010) | 2100 (1990) | 1670 (1590) | 1580 (1500) | 1590 (1510) | 1580 (1510) |
0.10 | Interna | 540 (460) | 530 (450) | 530 (450) | 530 (450) | 470 (410) | 460 (400) | 470 (400) | 470 (400) |
0.10 | External | 500 (430) | 490 (420) | 500 (425) | 480 (420) | 450 (400) | 460 (390) | 460 (390) | 410 (350) |
1.00 | Internal | 59 (49 | 58 (49) | 59 (49) | 59 (49) | 58 (48) | 58 (48) | 58 (48) | 57 (48) |
1.00 | External | 58 (48) | 57 (48) | 58 (48) | 58 (48) | 57 (48) | 57 (48) | 57 (48) | 55 (48) |
Reading rates (readings per second) typical for 60 Hz (50 Hz), SCPI programmed16
NPLC | Trigger Origin | Measure to Memory | Measure to GPIB | Measure to USB | Measure to LAN | Source Measure Sweep to memory | Source Measure Sweep to GPIB | Source Measure Sweep to USB | Source Measure Sweep to LAN |
0.01 | Internal | 3040 (2800) | 3000 (2760) | 3000 (2760) | 3010 (2710) | 1710 (1630) | 1610 (1544) | 1440 (1380) | 1690 (1590) |
0.01 | External | 2320 (2165) | 2290 (2140) | 2340 (2150) | 2290 (2130) | 1680 (1590) | 1560 (1525) | 1410 (1360) | 1660 (1560) |
0.10 | Internal | 540 (460) | 540 (450) | 540 (460) | 540 (450) | 540 (410) | 470 (410) | 450 (390) | 470 (410) |
0.10 | External | 510 (440) | 510 (430) | 510 (440) | 510 (430) | 470 (400) | 470 (400) | 450 (390) | 470 (400) |
1.00 | Internal | 59 (49) | 59 (49) | 59 (49) | 59 (49) | 58 (48) | 58 (48) | 57 (48) | 58 (48) |
1.00 | External | 58 (49) | 58 (49) | 58 (49) | 58 (49) | 58 (49) | 58 (48) | 57 (47) | 58 (48) |
Notes
15. Reading rates applicable for voltage or current measurements, autozero off, autorange off, filter off, binary reading format, and source readback off.
16. SCPI programming mode.
General Characteristics (default mode unless specified)
Factory Default Standard Power-Up | SCPI Mode | ||||||||||||||||
Source Output Modes | Fixed DC Level, Memory/Configuration List (mixed function), Stair (linear and log). | ||||||||||||||||
Memory Buffer | >5,000,000 readings with selected measured values and timestamp. | ||||||||||||||||
Real-Time Clock | Lithium battery backup (3 yr. + battery life). | ||||||||||||||||
Remote Interfaces |
|
||||||||||||||||
Digital I/O Interface: |
|
||||||||||||||||
Programmability | SCPI or TSP command sets. | ||||||||||||||||
TSP Mode | Embedded Test Script Processor (TSP) accessible from any host interface. | ||||||||||||||||
IP Configuration | Static or DHCP. | ||||||||||||||||
Expansion Interface | The TSP-Link expansion interface allows TSP enabled instruments to trigger and communicate with each other. | ||||||||||||||||
LXI Compliance | 1.5 LXI Device Specification 2016. | ||||||||||||||||
Display | 5 inch capacitive touch, color TFT WVGA (800×480) with LED backlight. | ||||||||||||||||
Input Signal Connections | Front: Banana. Rear: High-voltage triaxia. | ||||||||||||||||
Interlock | Active High Input. | ||||||||||||||||
Cooling | Forced air, variable speed. | ||||||||||||||||
Over Temperature Protection | Internally sensed temperature overload puts unit in standby mode. | ||||||||||||||||
Power Supply | 100 V to 240 V RMS, 50–60 Hz (automatically detected at power up). | ||||||||||||||||
VA Rating | 190 volt-amps max. | ||||||||||||||||
Altitude | Maximum 2000 meters above sea level. | ||||||||||||||||
EMC | Conforms to European Union EMC Directive. | ||||||||||||||||
Safety | NRTL listed to UL61010-1 and UL61010-2-30. Conforms with European Union Low Voltage Directive. | ||||||||||||||||
Vibration | MIL-PRF-28800F Class 3 Random. | ||||||||||||||||
Warm-Up | 1 hour to rated accuracies. | ||||||||||||||||
Dimensions | With bumpers and handle: 106 mm high × 255 mm wide × 425 mm deep (4.18 in × 10.05 in × 16.75 in). Without bumpers and handle: 88 mm high × 213 mm wide × 403 mm deep (3.46 in × 8.39 in × 15.87 in.) |
||||||||||||||||
Weight | With bumpers and handle: 4.54 kg (10 lb). Without bumpers and handle: 4.08 kg (9.0 lb). |
||||||||||||||||
Environment | Operating: 0 °C to 50 °C, 70% relative humidity up to 35 °C; derate 3% relative humidity/°C, 35 °C to 50 °C. Storage: -25 °C to 65 °C. Pollution Category: 2 |
SourceMeter® is a registered trademark of Keithley Instruments LLC. All other trademarks are the property of their respective owners.
Ordering Information
2470 | 1000 V, 1 A, 20 W SourceMeter SMU Instrument |
Supplied Accessories
8608 | High Performance Test Leads |
USB-B-1 | USB Cable, Type A to Type B, 1 m (3.3 ft) |
CS-1616-3 | Safety Interlock Mating Connector |
17469460X | TSP-Link/Ethernet Cable |
Documentation available at www.tek.com/keithley | |
2470 QuickStart Guide | |
TSP Toolkit Software (available at www.tek.com) | |
LabVIEW and IVI Drivers (available at www.tek.com/keithley) |
Available Accessories
Probe | |
8606 | High Performance Modular Probe Kit |
Cables, Connectors, Adapters | |
TRX-1100V-BAN | HV Triax to Banana Adapter. Converts the 4 triax connectors on the rear panel to 5 banana jacks |
TRX-1100V-* | 3-slot HV Low Noise Triax Cable (0.5 m, 1 m, 2 m, 3 m lengths available) |
TRX-1100V-CONN | 3-Slot HV Male Triax Cable Connector |
TRX-1100V-PCBCONN | 3-Slot HV Female Triax PC Board Mount Connector |
TRX-1100V-FFBARREL | 3-Slot 1100 V Triax FemaleE to Female Barrel Interconnect |
TRX-1100V-FMFTEE | 3-Slot 1100 V Triax Male to Dual Female Tee Adapter |
TRX-1100V-FFFTEE | 3-Slot 1100 V Triax Female to Dual Female Tee Adapter |
TRX-1100V-TBC | 3-Slot 1100 V Triax Female Bulkhead Connector |
CS-1616-3 | Safety Interlock Mating Connector |
Communication Interfaces and Cables | |
7007-1 | Shielded GPIB Cable, 1 m (3.3 ft) |
KPCI-488LPA | IEEE-488 Interface for PCI Bus |
KUSB-488B | IEEE-488 USB-to-GPIB Interface Adapter |
Rack Mount Kits | |
4299-8 | Single Fixed Rack Mount Kit |
4299-9 | Dual Fixed Rack Mount Kit |
Software Options | |
I-V Tracer | Graphical SMU Curve Tracer Software |
Kickstart | Instrument Control Software |
Available Services
2470-3Y-EW | 1 Year Factory Warranty extended to 3 years from date of shipment |
2470-5Y-EW | 1 Year Factory Warranty extended to 5 years from date of shipment |
C/2470-3Y-17025 | KeithleyCare® 3 Year ISO 17025 Calibration Plan |
C/2470-3Y-DATA | KeithleyCare 3 Year Calibration w/Data Plan |
C/2470-3Y-STD | KeithleyCare 3 Year Std. Calibration Plan |
C/2470-5Y-17025 | KeithleyCare 5 Year ISO 17025 Calibration Plan |
C/2470-5Y-DATA | KeithleyCare 5 Year Calibration w/Data Plan |
C/2470-5Y-STD | KeithleyCare 5 Year Std. Calibration Plan |
C/NEW DATA | Calibration Data for New Units |
C/NEW DATA ISO | ISO-17025 Calibration Data for New Units |
Warranty Information
Warranty Summary | This section summarizes the warranties of the 2470. For complete warranty information, refer to the Tektronix warranty page at www.tek.com/service/warranties/warranty-2. Any portion of the product that is not manufactured by Keithley is not covered by this warranty and Keithley will have no duty to enforce any other manufacturer's warranties. |
Hardware Warranty | Keithley Instruments, Inc. warrants the Keithley manufactured portion of the hardware for a period of one year from defects in materials or workmanship; provided that such defect has not been caused by use of the Keithley hardware which is not in accordance with the hardware instructions. The warranty does not apply upon any modification of Keithley hardware made by the customer or operation of the hardware outside the environmental specifications. |
Software Warranty | Keithley warrants for the Keithley produced portion of the software or firmware will conform in all material respects with the published specifications for a period of ninety (90) days; provided the software is used on the product for which it is intended in accordance with the software instructions. Keithley does not warrant that operation of the software will be uninterrupted or error-free, or that the software will be adequate for the customer's intended application. The warranty does not apply upon any modification of the software made by the customer. |