Introduction
The most widely measured physical parameter is temperature. Whether in process industry applications or in laboratory settings, accurate temperature measurements are a critical part of success. Accurate temperature measurements are needed in medical applications, materials research in labs, electrical/electronic component studies, biology research, geological studies, and electrical product device thermal characterization.
There are many different types of sensors available to measure temperature. The three most common are resistance temperature detectors (RTDs), thermocouples (TCs), and thermistors. Each of them have specific operating parameters that may make it a better choice for some applications than others. Solid state sensors are also available for moderate temperature range applications and have the advantage of built-in signal conditioning and ease of interfacing – in some cases with direct digital serial interfaces. Due to the scope of this article, such sensors will not be covered in detail.
Selecting a Temperature Sensor
There are several considerations when selecting a temperature sensor. First, consider the type of application. What is the device to be measured? Is it ambient air temperature in a room or enclosure? An electronic component with plastic or metal packaging that may or may not have high voltages present? Or an ingot of glowing steel? Perhaps some part of an automobile engine such as an intake or exhaust port? Some of these considerations can drive the choice of sensor due to environmental and safety factors, cost budget per sensor, and distance from sensor to instrument.
The next consideration is the range of expected measured temperature. An automobile engine block, when fully warmed up, can generate temperatures of greater than 100°C. Most thermocouples can handle this temperature range, and the type K is the most general purpose thermocouple for such applications. On the other hand, a ceramic firing kiln can be many hundreds of degrees C. A type N would be good for the higher temperature, because of their stability and resistance to high temperature oxidation. On the other end of the scale, superconducting devices achieve superconductivity at very low temperatures, around several Kelvin (or just above absolute zero or – 273°C), so the sensor must be able to withstand the sub-freezing climate in which superconductors operate. Type E thermocouples with their high output (about 68uV/C) would be good, because they are well suited to low temperatures. Table 1 gives a summary of TCs and their ranges.
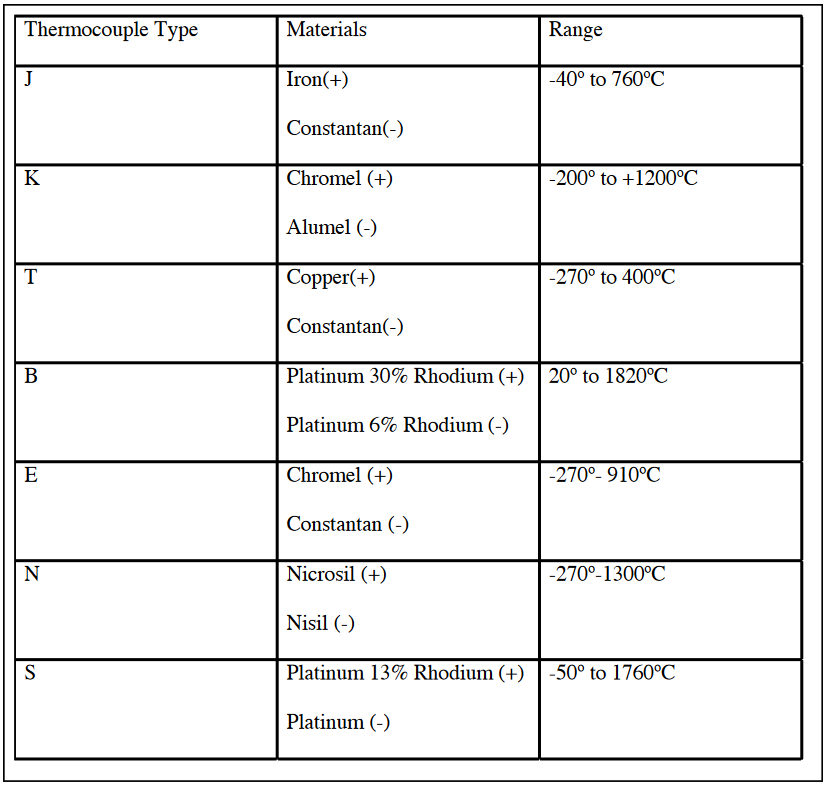
Another consideration is the available area for the sensor to be mounted to adequately sense the temperature to be measured. The device to be measured must have room enough to handle the selected sensor mounting. For example, an integrated circuit is a tiny electronic component, so the right sensor would depend on what parameter is to be measured, the IC package, or the lead frame or chip device itself. Most sensors come in a variety of shapes and sizes, and one is sure to fit the application. For the tiny electronic circuit of an IC, an electrically isolated RTD would probably be best because of the size, isolation, and accuracy of the RTD.
Thermocouples
By far the most commonly used temperature sensor is the thermocouple or TC. The key reasons are that thermocouples are low cost, extremely rugged, can be run long distances, are self powered, and there are many types of thermocouples available to cover a wide range of temperatures. Low cost speaks for itself in many applications. Ruggedness means they will last in many different environments, including outdoors and with exposure to harsh factory environments. Metal-sheathed TCs are available to help protect them in harsh or corrosive environments, or they can be run inside conduit piping. Different alloys allow different range and sensitivity of measurement. Some common types of TCs include J, K, T, E, R, S, B, and N, which refers to the type of material from which they are constructed (as in table 1). The type J, K, and T are the most common and are readily available in spools or pre-made forms. The ranges for all types of thermocouples can be found in NIST (National Institute of Standards and Technology) reference tables at www.nist.gov.
One important property of thermocouples is their non-linearity; that is, thermocouple output voltage is not linear with respect to temperature. Consequently, to convert output voltage to temperature accurately requires mathematical linearization.
Thermocouples consist of two dissimilar metals joined (either welded or twisted) together at one end and open at the other. They operate on the principle of the thermoelectric effect and can be thought of as the junction of two different metals producing a voltage when a thermal difference exists between the two metals (also known as the Seebeck Effect). The voltage signal at the open or output end is a function of the temperature at the closed end. As the temperature rises, the voltage signals increases.
Here’s what really happens. The open-end signal is a function of not only the closed-end temperature (the point of measurement) but also the temperature of the open end. Only by holding T2 at a standard temperature can the measured signal be considered a direct function of the change in T1. The open-end voltage, V1, is a function of not only the closed end temperature (the temperature at the point of measurement), but also the temperature at the open end (T2). The reason the voltage is developed is because different materials produce different voltage for the same temperature difference. This is the reason for the two different metals. If they were the same metals, then the voltage would be zero.
The industry standard for T2 is 0°C. Most tables and charts make the assumption that T2 is at 0°C. In industrial instrumentation, the difference between the actual temperature T2 and 0°C is usually corrected electronically within the instrument. This adjustment is known as cold junction compensation or ice-point reference.
Advantages
Thermocouples have many advantages over other types of temperature sensors. For one, they are self powered, requiring no external power supply. They are also extremely rugged and can withstand harsh environments. Thermocouples are also inexpensive compared to RTDs and thermistors and come in a wide variety of types with wide temperature ranges. (Refer to Table 1 for Thermocouple ranges.)
Disadvantages
Thermocouples are non linear and require cold-junction compensation (CJC) for linearization. Also, the voltage signals are low, typically in the tens to hundreds of microvolts, requiring careful techniques to eliminate noise and drift in low-voltage environments. Accuracies are typically in the range of 1-3% depending on wire alloy consistency and cold junction accuracies.
Common Errors
Avoiding some common mistakes when setting up and using thermocouples will yield better measurements. One common problem is that the CJC is not configured or compensated properly or at all. This leads to inaccurate or nonlinear temperature measurements.
Another mistake is not to use copper wire from the thermocouple connection to the measurement device. Normally the measurement devices (voltmeters, DMMs, etc.) have copper input terminals. Using another alloy (tin, aluminum, etc.) essentially introduces another thermocouple into the measurement. This is because any junction of dissimilar metals forms a thermocouple. On the measurement device side, the voltmeter being used may not be sensitive or accurate enough for thermocouple measurements. To avoid the problem, make sure the voltmeter is sensitive and accurate enough for the low-voltage signals (uV to mV) of the thermocouples. Some proper shielding would also prevent any external noise. Surround the sensitive circuit with a conductive shield and connect it to circuit or measurement LO for maximum effect.
RTDs
One of the most accurate temperature sensors is a resistance temperature detector, or RTD. In an RTD, the resistance of the device is proportional to temperature. The most common material for RTDs is platinum, with some RTDs being made from other metals such as nickel or copper. RTDs have a wide range of temperature measurement. Depending on how they are constructed, they can measure temperatures in the range of –270°C to +850°C.
RTDs require an external stimulus, usually a current source, to function properly. However, the current generates heat in the resistive element, which causes an error in the temperature measurements. The measurement error is calculated by the formula:
Delta T = P x S
where T is temperature, P is the I-squared power generated, and S is degrees C/milliwatt.
There are several techniques for measuring temperature with an RTD. The first is a two-wire method. This method works by forcing current through the RTD and measuring the resulting voltage. The benefit is that it is a simple method using only two wires, making it easy to connect and implement. The main drawback is that the lead resistance is part of the measurement, which can introduce some error into the measurement.
An improvement on the two-wire method is the three-wire method. Here again, a current is forced through the device and the resulting voltage is measured. However, a third wire provides compensation for the lead resistance. This requires either a three-wire compensating measurement unit or actually measuring the contribution from the third wire and subtracting it from the overall measurement.
A third technique is the four-wire method, which is generally found in calibration labs for reference probes. Similar to the other two methods, a current is forced through the RTD and the resulting voltage is measured. However, the current is forced on one set of wires, while the voltage is sensed on another set. This method completely compensates for the lead resistance. The voltage is sensed at the resistive element, not at the same point as the source current, which means that the lead resistance is completely out of the measurement path. In other words, the test lead resistance is not part of the actual voltage measurement.
As an example, consider the test lead resistance to be about 0.2Ohms and the RTD to have a resistance of 100 Ohms. In this example, the test-lead resistance is about 0.2% of the total resistance in the test circuit. With the four-wire method, the test lead resistance is not part of the measurement circuit and therefore only the resistance of the RTD is measured. This eliminates the 0.2% error for a much more accurate measurement.
Pros and Cons
RTDs have some advantages over other temperature sensors. For one, they are the most stable and most accurate of the different temperature measurement devices. RTDs, like thermocouples, are not linear. This means they also need some linearization, which is generally done by using correction factors.
One of the drawbacks is that RTDs are more expensive than thermistors and thermocouples. They also require a current source. They have a small delta R, which means there is a low resistance-totemperature change. For example, to change one degree Celsius, the RTD might change by 0.1Ohm.
When using RTDs, several common occurrences are often not taken into account, the biggest of which is self-heating. Self-heating of the RTD with the test current could result in measurement inaccuracy. If measuring low temperature (below 0°C), the heat generated from the RTD could derate the expected temperature. Also, if there is no compensation for the test leads, even more error can be introduced into the measurement. Using the four-wire method helps eliminate this type of error. Another common mistake is not selecting the proper RTD temperature range. Trying to measure outside of the RTD temperature range can result in greater errors or even sensor damage.
Thermistors
Another common temperature sensor is a thermistor. Like an RTD, a thermistor changes resistance as temperature changes. The thermistor offers higher sensitivity than RTDs, meaning that the thermistor resistance will change much more in response to temperature changes than an RTD.
Most thermistors have a negative temperature coefficient, meaning that the resistance decreases when the temperature increases. Thermistors are also less linear than RTDs and require a correction factor. The Steinhart-Hart equation, which describes the resistance change of a thermistor as related to temperature, is used to help approximate individual thermistor curves. (A good example of the calculation of the curves is at http://www.reed-electronics.com/tmworld/software/stinhart.zip.)
The equation is:
1/T = A + B x (lnR) + C x (lnR) squared
where:
T is degrees in Kelvin
R is the thermistor resistance
A, B, and C are curve fitting constants determined through a calibration process ln is the natural log function (log to the base e)
Pros and Cons
Thermistors have some advantages over other sensors. For one, they are simple to set up and operate using just a standard two-wire measurement method. They also have a fast response time. Because thermistors can be made very small, they can respond to temperature changes quickly.
On the down side, the non-linear properties of thermistors require linearization. They also have a limited temperature range and are not as rugged as TCs or RTDs. Because thermistors are semiconductors, they are more likely to have de-calibration issues at high temperatures. Thermistors also require a current source and like RTDs have self-heating characteristics.
Common Mistakes
Not allowing for self-heating and selecting a device with an inadequate temperature range are common mistakes made when using thermistors. However, there are a few ways to reduce self-heating. The typical test current is a constant DC current. Using a pulsed DC current helps reduce self-heating effects, because the current is applied for a short portion of the measurement cycle, thereby reducing the overall developed power in the thermistor.
Another common mistake is measuring temperature outside of the range of the thermistor. Always consider the range of temperature to be measured. Remember, the temperature range of the thermistor is about a few hundred degrees C. Some manufacturers even caution that extended exposure even below operating limits will cause the thermistor to drift out of tolerance.
Summary
There are several sensors from which to choose for measuring temperature. The thermocouple, RTD, and thermistor are three of the most common sensors used today. (Table 2 offers a comparison of these three sensor types.) Thermocouples are the most widely used sensors. They have the widest measurement range and are used for flame temperatures, gas/electric ovens, and heating systems. Thermistors are mainly used in human environment temperatures (from 0°C to 30°C), such as freezers and incubators, whereas RTDs are the most accurate and are used almost exclusively in calibration/standards applications. Each sensor has it own advantages and disadvantages. Selecting the appropriate sensor is important in obtaining accuracy and reliability of the temperature measurement.
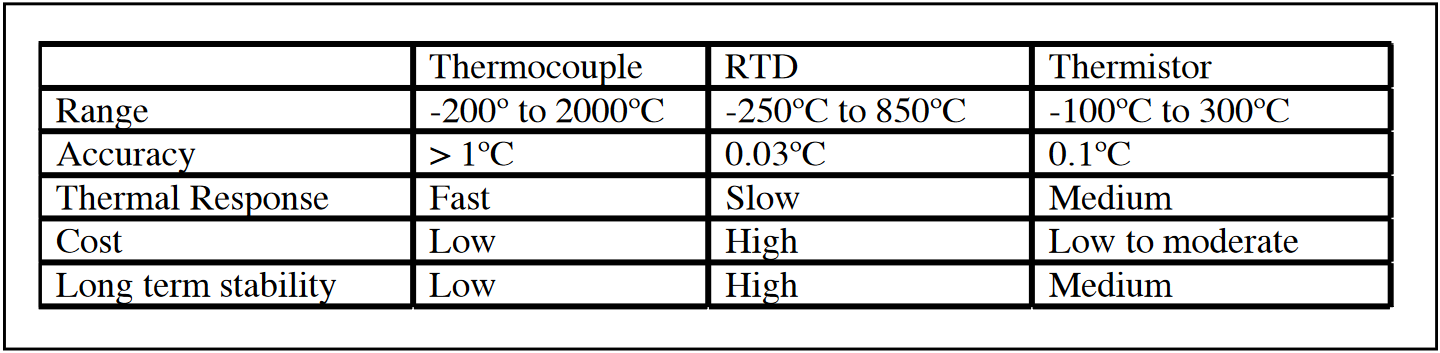
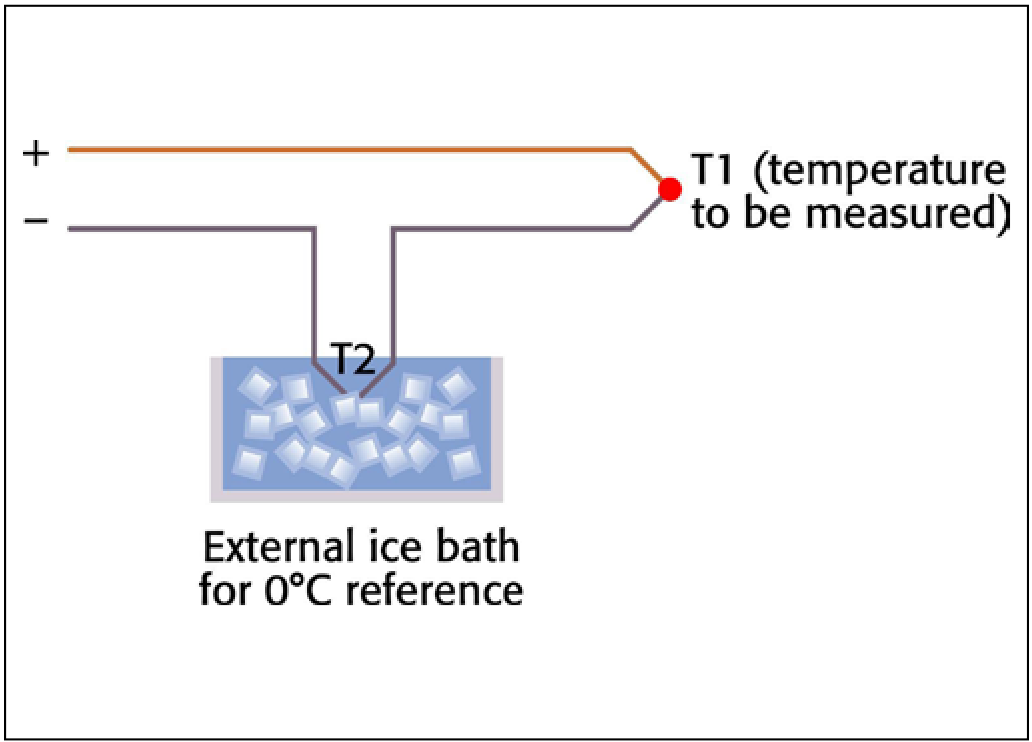
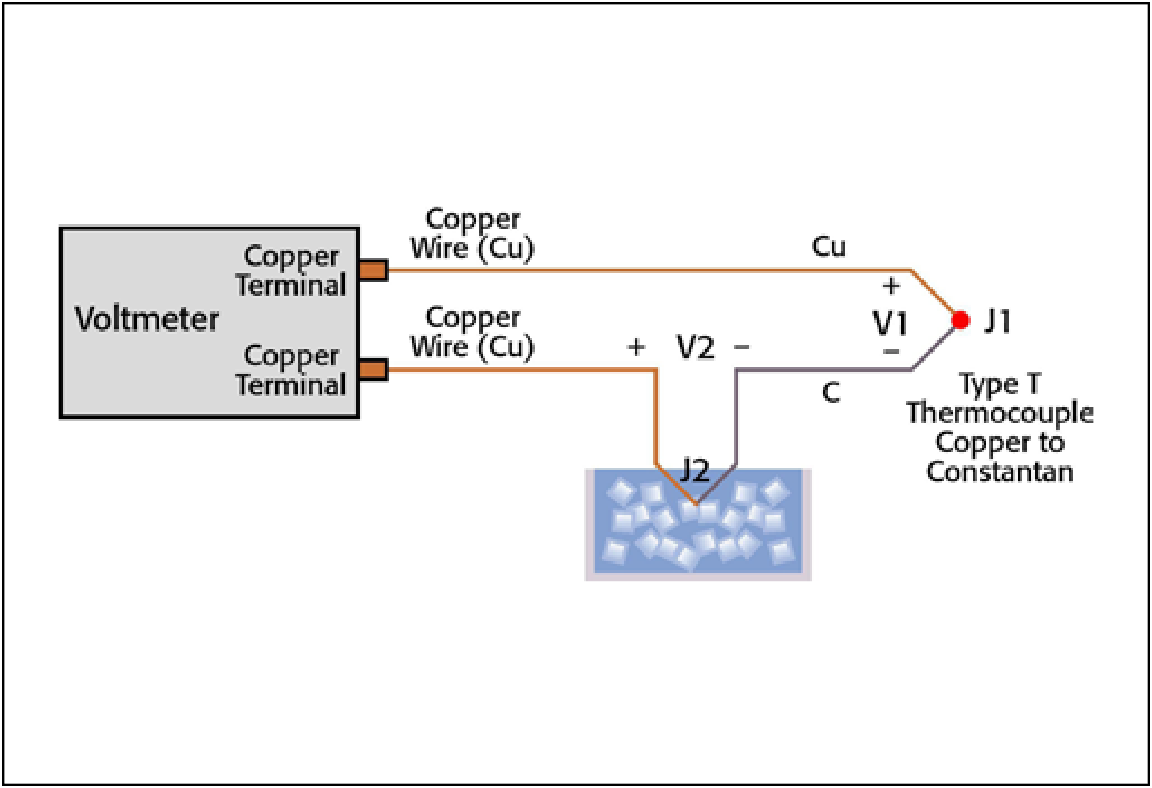
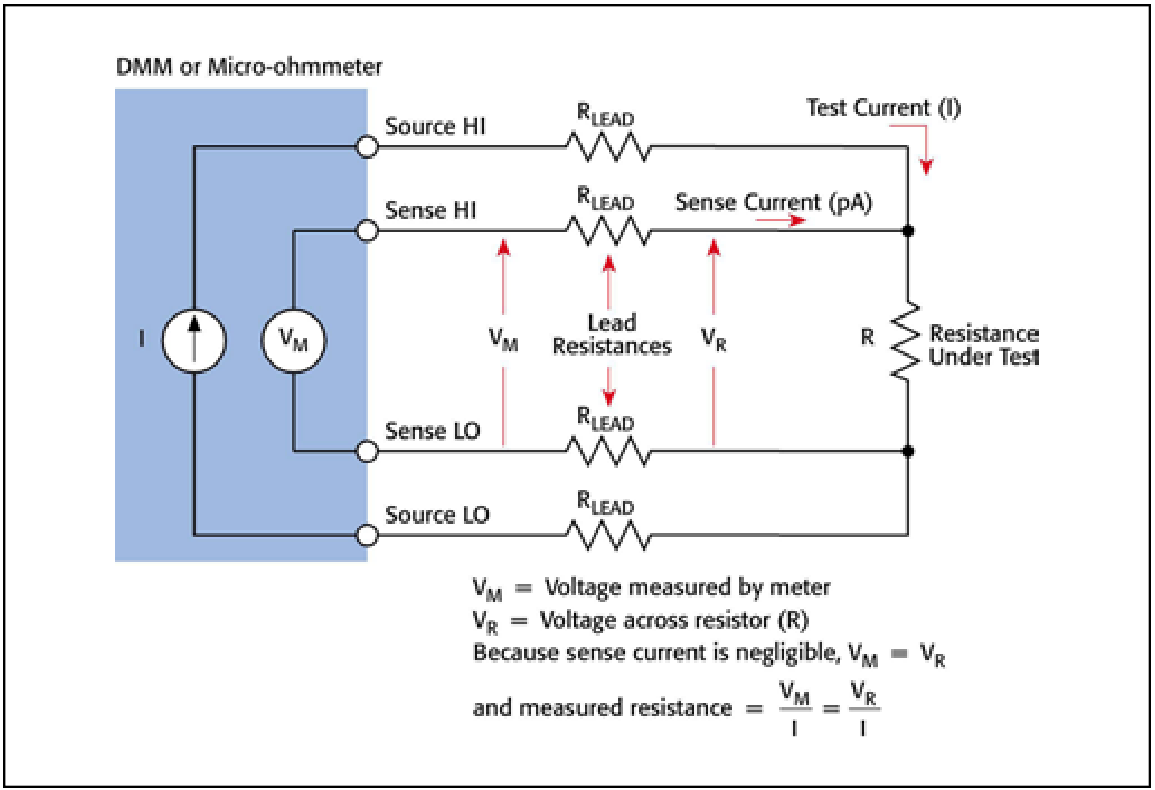