1. Introduction
PAM4 (4-level pulse amplitude modulation) is being adopted in many applications at data rates of 50 Gb/s and higher. By encoding two bits in each symbol, PAM4 signals use half the bandwidth of the logic-emulating NRZ (non-return to zero) modulation scheme to transmit at the same data rate.
Operating at half the bandwidth sidesteps the crippling effects of loss and inter-symbol interference caused by nonuniform channel frequency response, but the advantages of PAM4 come at a cost: the complexities of a four level system, 12 different symbol transitions, each with its own slew rate, and a drop in SNR (signal to noise ratio) of at least a factor of three, 9.5 dB for electrical voltage and 4.7 dB for optical power.
The dramatic SNR drop is addressed in most cases by the introduction of forward error correction. FEC provides the performance margin necessary to raise the maximum permitted raw BER (bit error ratio) from 1E-12 to 2.4E-4. At such high BERs, real time oscilloscopes are capable of measuring BER without approximation or extrapolation terrain that used to be reserved for expensive and inflexible BERTs (BER testers).
This paper presents techniques for analyzing 50+ Gb/s optical and electrical PAM4 signals. Drawing primarily from the latest emerging technologies, 50/100/200/400 GbE (gigabit Ethernet, IEEE 802.3bs and 802.3cd) and OIF-CEI 4.0 (Optical Internetworking Forum-Common Electrical Interface), we’ll look at signal analysis from the perspectives of compliance and debug testing for both components and systems.
In the next section we give a brief summary of PAM4 standards and their topologies. Section 3 discusses test configurations for debugging optical and electrical signals. In Section 4, we work through the key PAM4 optical and electrical compliance tests and conclude in Section 5 with a summary of the test equipment features and requirements that you need to debug PAM4 transceivers and perform standards compliance tests.
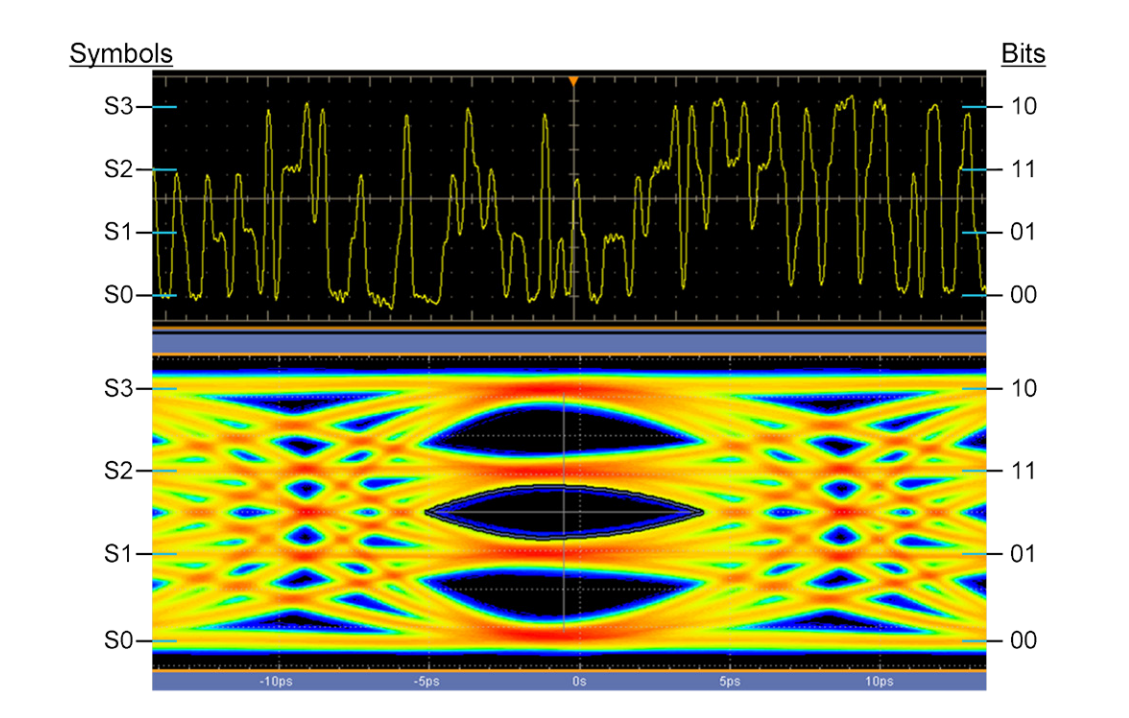
2. Current PAM4 Technologies
Figure 1 shows a PAM4 waveform and eye diagram. The four PAM4 symbols are the power or voltage levels of the signal. The symbols are usually referred to from lowest level to highest as S0, S1, S2, S3 and for electrical signals can also be described as -1, -1/3, 1/3, 1, the latter indicates the desired even spacing of the four amplitude levels. The three eye diagrams are called low, middle, and upper.
Since each PAM4 symbol carries two bits, one symbol error can result in either one or two bit errors. Gray coding helps SER (symbol error ratio) converge to BER by encoding the bit pairs 11 in S2 and 10 in S3, but we shouldn’t assume that SER and BER are equal.
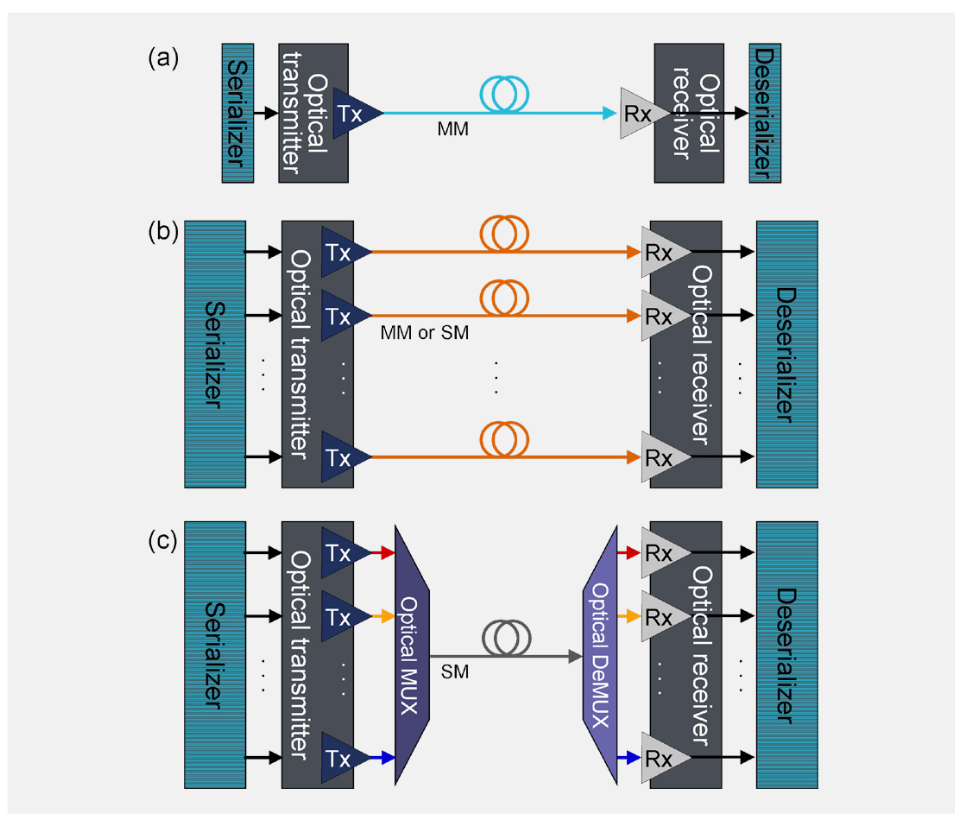
PAM4 signaling is being deployed in both single and multichannel systems. A single 26 GBd PAM4 signal can be transmitted on either a SM (single mode) or MM (multi mode) fiber, Figure 2a. MM (multi-mode) fibers are limited to one wavelength each and have limited reach of about 100 m due to modal dispersion. To achieve higher data rates, several optical PAM4 signals can be transmitted, each on its own SM or MM fiber, Figure 2b. Alternatively, WDM (wavelength division multiplexed) systems combine separate optical PAM4 signals, each with its own wavelength, onto a single SM fiber, Figure 2c.
The properties of the PAM4 IEEE 802.3bs and 802.3cd (GbE), OIF-CEI 4.0, and 64 GFC configurations are summarized in Table 1. These optical and electrical standards cover applications for optical signal transmission across fibers and electrical chip-to-chip, chip-to-optical module, and module-tochip transmission across PCB (printed circuit board) including the necessary connectors.
Notice the BER requirements in the right hand column. The pre-FEC BER requirement, BER ≤ 2.4E-4 for optical signaling should assure that the corrected, post-FEC BER is less than 1E-13. FLR (frame loss ratio) is the ratio of validated 64 octet frames to the total number of frames received; FLR is a postFEC requirement.
For electrical signaling, the OIF-CEI (Optical InternetworkingCommon Electrical Interface) requirements of pre-FEC BER ≤ 1E-6 for VSR (very short reach) and MR (medium reach) signals and 1E-4 for LR (long reach) signals are designed to assure post-FEC BER ≤ 1E-15. Since FEC cannot correct long burst errors, OIF-CEI limits the maximum allowed burst error lengths per 1E20 symbols: for VSR the maximum burst error length is 15 PAM4 symbols, for MR it’s 94 symbols, and for LR it’s 126 symbols.
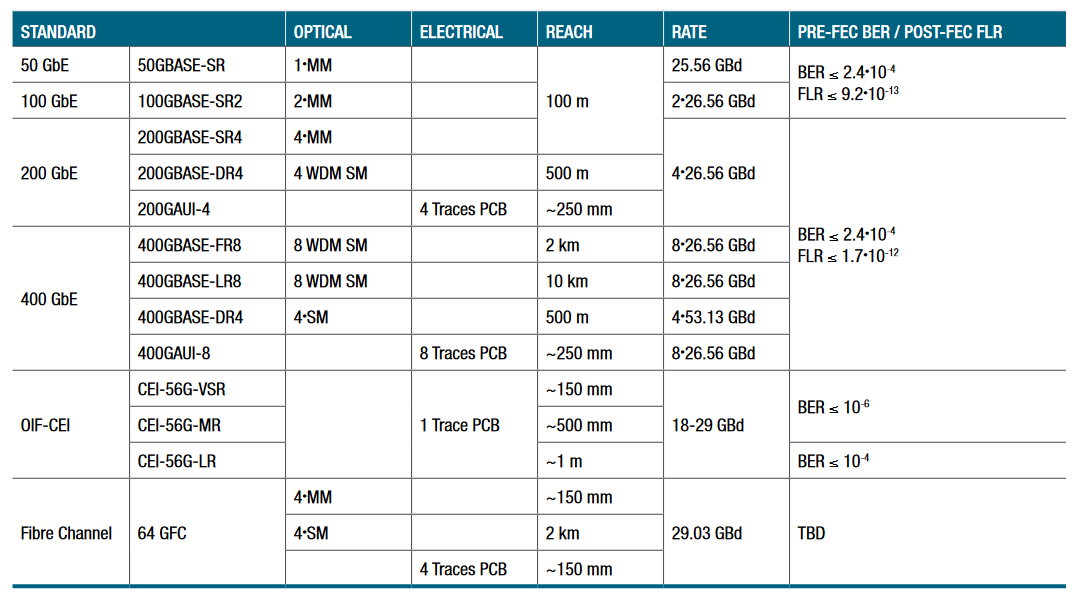

3. Debugging PAM4 Systems and Transceivers
Testing a transceiver for compliance to the specified requirements of a technology standard should assure that any signal that it transmits will be interoperable with any combination of other compliant channels and transceivers. Diagnostic or debug testing, on the other hand, uncovers the flaws that cause transceivers to malfunction or fail a compliance test.
One key difference between compliance testing and diagnostic testing is that compliance tests challenge the signal in a representative environment with a stressful test pattern, all channels turned on to generate maximum crosstalk, and the signal transmitted through a compliance test fiber or channel. In diagnostic testing it’s helpful to start with simple conditions to get everything working before introducing increasingly stressful patterns, channels, and crosstalk first separately and then together until we find the problem.
3.1 TEST SETUP AND CONCEPTS
Figure 3 shows typical setups for transmitter testing. In Figure 3a an optical signal is transmitted through a fiber that generates CD (chromatic dispersion) and is then analyzed by an oscilloscope equipped with a precision O/E (optical to electrical) converter. The resulting voltage waveform must be an accurate image of the optical power waveform.
In Figure 3b, an electrical signal is transmitted through a compliance test board that introduces ISI (inter-symbol interference) and loss to challenge transmitter equalization. A test fixture is usually required to deliver the electrical signal to the oscilloscope. If you provide the relevant S-parameters, the oscilloscope can embed the desired effects of the compliance test board and/or de-embed the undesired effects of the text fixture.
Compliance tests should be performed in a representative crosstalk environment with every lane enabled and transmitting. To prevent correlation between the test channel and crosstalk aggressors, every channel should either transmit a different pattern, transmit the same patterns but displaced by at least 31 UI from each other, or operate at slightly different baud rates. All the transmitters should operate with the same equalizer settings.
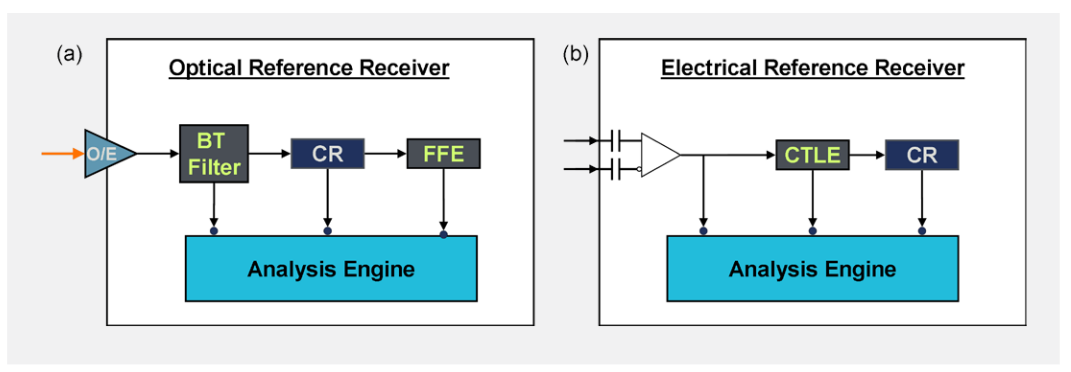
3.2 THE ROLE OF REFERENCE RECEIVERS IN DEBUG TESTING AND COMPLIANCE MEASUREMENTS
The oscilloscope serves as both test instrument and reference receiver in the transmitter test configurations shown in Figure 3. The ability of high performance real time oscilloscopes to replicate the performance of almost any receiver without additional hardware makes them flexible enough to perform a huge variety of debug tests as well as the most complex compliance measurements—provided that the scope has a low noise floor, appropriate bandwidth for the application, sufficient memory depth, and for optical measurements, a linear, low noise O/E convertor.
The capabilities and response of reference receivers are prescribed by each standard to meet minimally compliant performance requirements. For example, the reference receiver for 400 GbE optical signal testing, Figure 4a, includes a 4th Order Bessel Thomson Filter with -3 dB bandwidth at half the baud rate, a CR (clock recovery) circuit with a 4 MHz bandwidth and 20 dB/decade roll off, and a 5 tap FFE (feedforward equalizer) with taps spaced by one symbol period.
The electrical reference receiver, Figure 4b, includes CR as well as a three pole, two zero CTLE (continuous time linear equalizer) with adjustable gain in ½ dB steps. The front-end filter for the electrical reference receiver is not currently as well defined as the Bessel Thomson filter specified for the optical reference receiver. For analysis of 26 GBd PAM4 signals, we recommend 33 GHz oscilloscope bandwidth with smooth rolloff to 50 GHz. The bandwidth for 53 GBd is still being defined as this paper goes to press.
While the standards prescribe the reference receiver’s minimal performance, they do not prescribe how actual receivers should achieve that performance. Actual PAM4 transceiver and SerDes implementations often use proprietary analog or DSP (digital signal processing) techniques that surpass the minimally compliant filtering, CR, and equalization requirements of reference receivers.
By using a real time oscilloscope, you can experiment with different receiver designs.
For example, recovering a data-rate clock from an impaired PAM4 signal is more difficult than CR from an NRZ signal. The clock is recovered from the timing of signal transitions; the cleaner the transition, the more seamless the CR. While every NRZ transition swings between the minimum and maximum power or voltage levels, just 1/6 of PAM4 transitions swing between S0 and S3; half of PAM4 signal transitions span just 1/3 of the peak-to-peak levels. Using built-in algorithms through a straightforward user interface, you can easily configure PLL (phase-locked loop) or DSP-based CR designs and find ways to recover clocks from even highly impaired signals. You can then view the signal with the extracted clock or export the waveforms for offline analysis.
Similarly, you can experiment with different equalization schemes, analyze signals before and after equalization, determine the best eye-opening gain for your CTLE, the best taps for your FFE, and determine whether DFE (decision feedback equalization) is suitable for your design.
DFE is largely being replaced in electrical receivers by CTLE or both CTLE and receiver FFE. DFE was one of the innovations that enabled NRZ designs to achieve multi-gigabit data rates, but it is subject to burst errors. The Reed Solomon FEC schemes used in most PAM4 applications can accommodate burst errors of 30 bits without a problem, but with a pre-FEC BER of 1E-6, FEC failure can be problematic. On the other hand, with four "decisions" to "feedback," PAM4 DFE has potential. Choosing whether or not to use DFE in a receiver requires careful analysis.
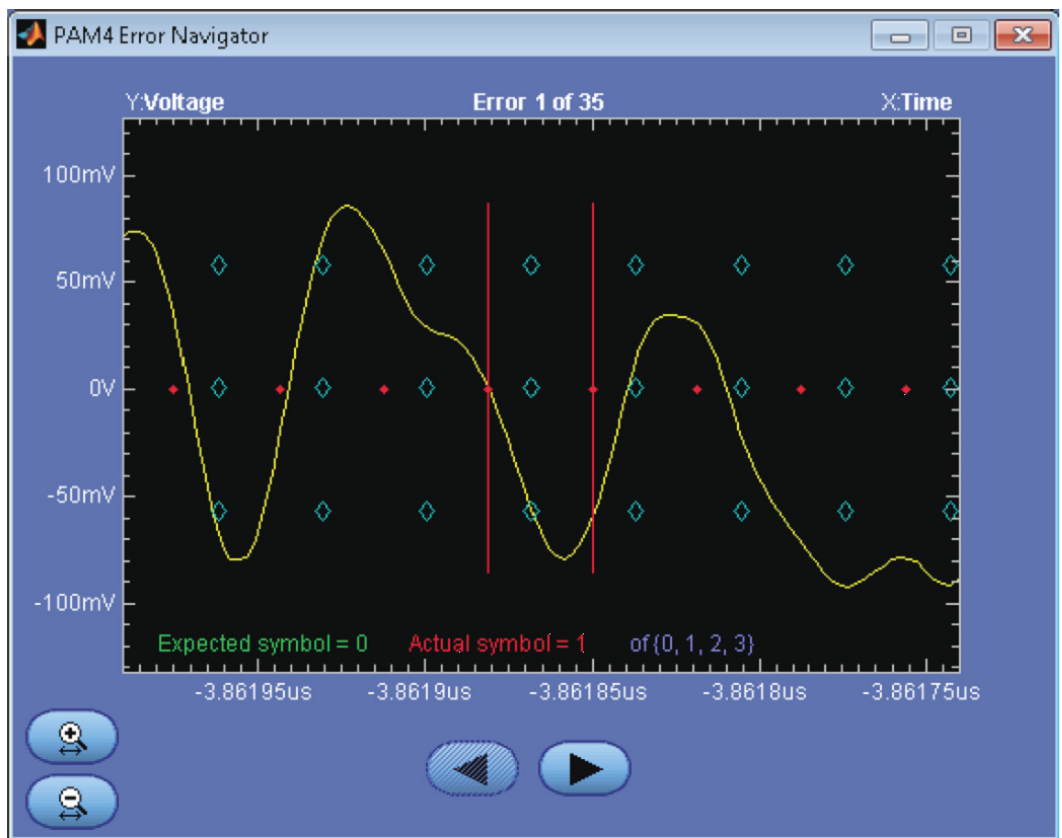
3.3 ERROR NAVIGATION
Unlike the single value error measurements performed by a BERT, error navigation, Figure 5, helps you identify problems by analyzing the locations of symbol errors within test patterns. You can examine the sequence of symbols preceding the error along with the recovered clock, symbol detector slicer thresholds, and the actual symbol. Here are a few examples:
- CD (chromatic dispersion) and ISI (inter-symbol interference) cause symbol errors that reoccur at the same point in repeating test patterns and tend to occur in similar symbol sequences.
- Crosstalk causes errors when aggressors introduce amplitude fluctuations at roughly the same time-delay of symbol errors.
- Drift in recovered clocks causes burst errors that occur at the same points in repeating test patterns.
- A receiver with insufficient AC-coupling bandwidth will experience baseline wander that can lead to burst errors that also occur at the same points in repeating test patterns.
- PJ (periodic jitter) and PN (periodic noise) cause errors that are correlated to their frequencies, but uncorrelated to the test pattern. PJ shuffles signal transitions horizontally across the sampling point and PN shifts signals above or below the sampling point causing errors.
3.4 TEST PATTERNS
The five test patterns in Table 2 are used for compliance testing but also serve most diagnostic test needs. PRBSnQ (pseudo-random binary sequence n quaternary) patterns are derived from the corresponding binary PRBSn patterns. The quaternary version, PRBSnQ, is derived by Gray coding bits from repetitions of the binary PRBSn pattern into the MSB (most significant bit) and LSB (least significant bit) of PAM4 symbols. Just as a PRBSn pattern consists of 2n-1 bits, the PRBSnQ consists of 2n-1 PAM4 symbols.
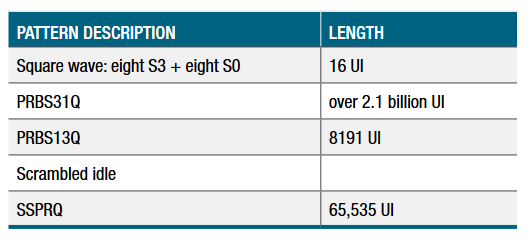
The simplest of the standard test patterns, the square wave composed of alternating runs of 8 consecutive S3 and S0 symbols is used in tests that concentrate on the power or voltage levels of the signal rails. PRBS13Q is used in most transmitter tests and PRBS31Q is used in most receiver tests. Since PRBS13Q consists of just 8191 symbols, it’s short enough for several repetitions of the waveform to be captured by an oscilloscope. With many repetitions, exhaustive signal analysis can be performed: signal impairments that are correlated or uncorrelated to the pattern can be separated, random jitter and noise can be measured, periodic jitter and noise can be identified and distinguished from crosstalk, and so on. PRBS31Q, on the other hand, has over two billion symbols; while a single repetition can’t be captured by an oscilloscope with even the deepest memory available. PRBS31Q provides a huge variety of symbol sequences to challenge the receiver’s ability to recover a clock, equalize the signal, and identify symbols.The fifth test pattern, SSPRQ (short stress pattern random quaternary), is formulated to be short enough (65,535UI) for oscilloscopes to make their most accurate measurements. It is composed of four particularly stressful sub-sequences from PRBS31. SSPRQ is used for both transmitter and receiver testing.
4. Analyzing PAM4 Signals
Table 3 lists typical signal requirements for the key PAM4 tests described below. The wide range of requirements covers all of the applications listed in Table 1. Longer reach optical and electrical tests have more stringent requirements than shorter reaches.
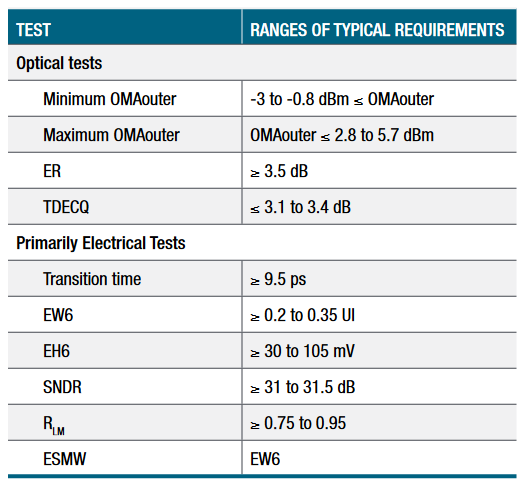
Techniques for analyzing PAM4 signals use more complications versions of the test developed for NRZ and introduces some new tests. For example, TDECQ (transmitter and dispersion eye closure quaternary) is a test specifically for optical PAM4 signals. It encompasses many signal quality metrics— transmitter noise, attenuation, dispersion, and equalization—all centered around launch power and serves as an excellent signal quality figure of merit.
The key compliance tests for electrical signals include the eye height, eye width, and signal to noise and distortion ratio. The linearity tests, level separation mismatch ratio and eye symmetry mask width are required of electrical signals but can also help gauge the quality of optical signals.
As mentioned above, all tests should be performed with specified reference receivers and crosstalk channels turned on and transmitting signals that are uncorrelated to the pattern of the test signal.
4.1 PAM4 VERSIONS OF OMA AND ER
The OMA (optical modulation amplitude) requirement assures a properly modulated signal and the ER (extinction ratio) requirement ensures that the signal isn’t obscured by CW (constant wave) light power.
The PAM4 versions of the OMA and ER measurements are essentially the same as their NRZ counterparts. The PAM4 version of OMA is called OMAouter because it’s built from the power levels of just the "outer" eye diagram. It’s the difference between the average S3 and S0 levels of the PAM4 signal:

The extinction ratio is the ratio of the average S3 power to the average S0 power:

The power levels are measured on either the PRBS13Q or SSPRQ test pattern. P3 is the power averaged over the center two unit intervals of a run of seven consecutive S3 symbols and P0 is averaged over the center two unit intervals of a run of six consecutive S0 symbols.
For WDM systems, either the signal under test must be isolated from the other signals by a suitable optical filter or the total optical power of all other signals must be less than -30 dBm.
4.2 TDECQ TRANSMITTER AND DISPERSION EYE CLOSURE QUATERNARY
The most complicated optical compliance test is TDECQ, it measure of the additional signal power necessary for the test signal to achieve the SER of an ideal signal. While complicated, it is also a fully automated oscilloscope measurement. While we can let the scope do the work, it’s important to understand what TDECQ conveys. In this section, we give a complete conceptual description of TDECQ without getting mired in the algorithmic details which are readily available in the standards.
TDECQ replaces the mask tests and TDP (transmitter dispersion penalty) measurements required of NRZ signals at lower data rates. Mask tests provide an intuitive view of signal quality. TDP, on the other hand, is highly correlated to BER but is a difficult measurement that requires expensive hardware.
Using the setup shown in Figure 3a, the SSPRQ pattern is transmitted and measured in a single oscilloscope acquisition without averaging. Each lane is tested separately but with all other lanes operating. The optical splitter and variable reflector should be tuned so that the test signal experiences the specified level of return loss. The polarization rotator should be set to generate maximum RIN (relative intensity noise). The optical filter should isolate the test signal from any others on the fiber by at least 20 dB.
The transmitter being tested has its own jitter, noise, crosstalk, nonlinearities, etc, and is measured on a device with a noise floor, sS. The long spool of optical fiber further degrades the test signal with chromatic dispersion. Since the signal might have one or more closed eyes, the reference receiver includes a 5-tap FFE. Since an FFE is a type of FIR (finite impulse response) filter, FFE aliasing is limited by subjecting the test signal to a fourth order Bessel Thomson filter with -3 dB bandwidth at half the baud rate.
Like TDP, TDECQ compares the test signal to an “ideal signal.” TDECQ and TDP both measure the additional signal power that would be necessary for the test signal to achieve the SER of an ideal signal. An equivalent way to say this is that they measure the amount of power depleted by the imperfections of the test signal combined with the effects of the test fiber.
The key difference between TDECQ and TDP is that the ideal signal used for TDP is a real, hardware, golden transmitter, but for TDECQ the ideal signal is simulated. The simulated ideal signal starts with a perfect PAM4 eye. The ideal eye is matched to the test signal eye through the requirement that it have the same value of OMAouter that the test signal has after it’s been conditioned by the reference receiver.
Simulated Gaussian noise, sIdeal, is added to the ideal signal waveform until its SER matches the specified target SER, 4.8E-4 (notice that the target SER is twice the maximum allowed pre-FEC BER). Similarly, simulated Gaussian noise, sG, is added to the measured waveform until its SER also matches the target SER. TDECQ is the ratio of the noise that must be added to the ideal signal to the noise that must be added to the real signal, keeping in mind that the noise on the measured signal also includes the oscilloscope noise floor, sS:
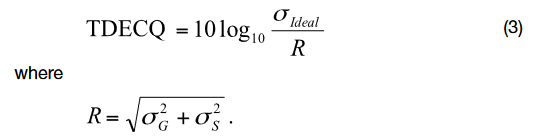
Since the ideal signal starts with no noise or jitter of any kind and the added noise is purely Gaussian, sIdeal can be calculated directly,

where Qt = 3.414, the Q-scale value for the target SER.
Determining TDECQ is an iterative numerical minimization process that involves trying different levels of sG. The 5 FFE taps must be optimized for every value of sG. The PAM4 symbols are decoded with three slicers as shown in Figure 6. The time-delay position of the slicers is set to minimize SER. The slice threshold power levels are also optimized for SER but are not allowed to vary more than 1% from equal vertical distribution.
When the 5 FFE taps and three slicer time-delays and thresholds are all optimized, SER is calculated for that value of sG. The process is iterated until a value for sG is found that yields the target SER. The final values of sG, sS, and sIdeal are then used to calculate TDECQ, Eq (3).
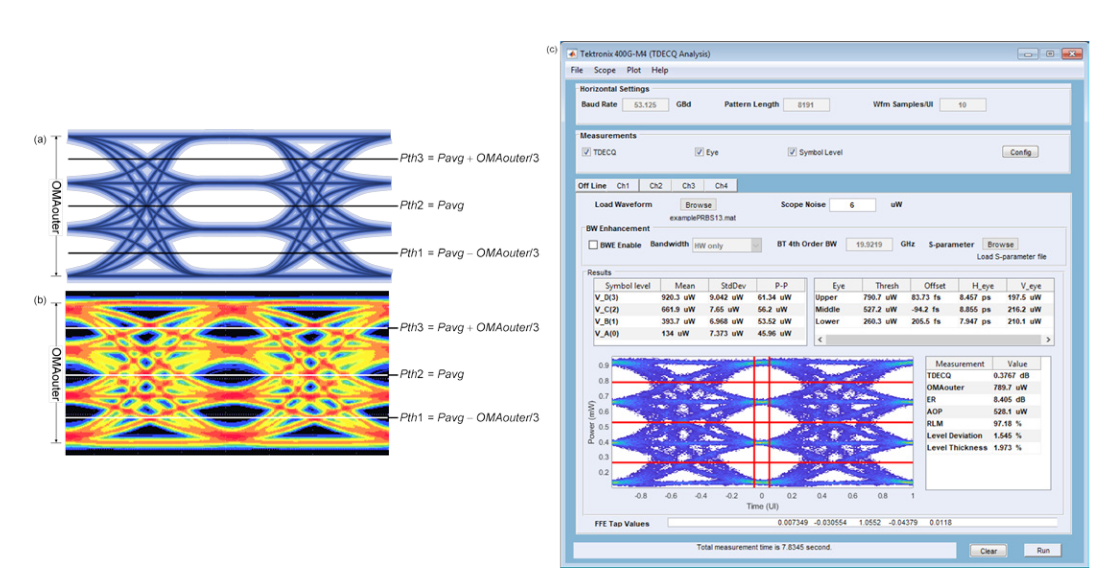
The interplay of the added noise and the FFE taps makes it sound complicated, but we can restate the problem in terms of four simultaneous requirements:
- The 5 FFE taps must be tuned to minimize SER.
- The sum of the five taps must be one.
- The time-delay and thresholds of the symbol decoding slicers are set to minimize SER.
- The noise added to the signal, sG, must degrade the signal to precisely the specified SER.
When all four conditions are met simultaneously, we get optimized values for the 5 FFE taps, R, the slicer timedelay and threshold level, and most importantly, TDECQ. Minimization of Equation (3) in several variables subject to two constraints is a fairly common problem in numerical analysis.
TDECQ indicates a transmitter’s power or OMAouter margin.Typically, TDECQ must be less than 3.1 to 3.4 dB, depending on the application.
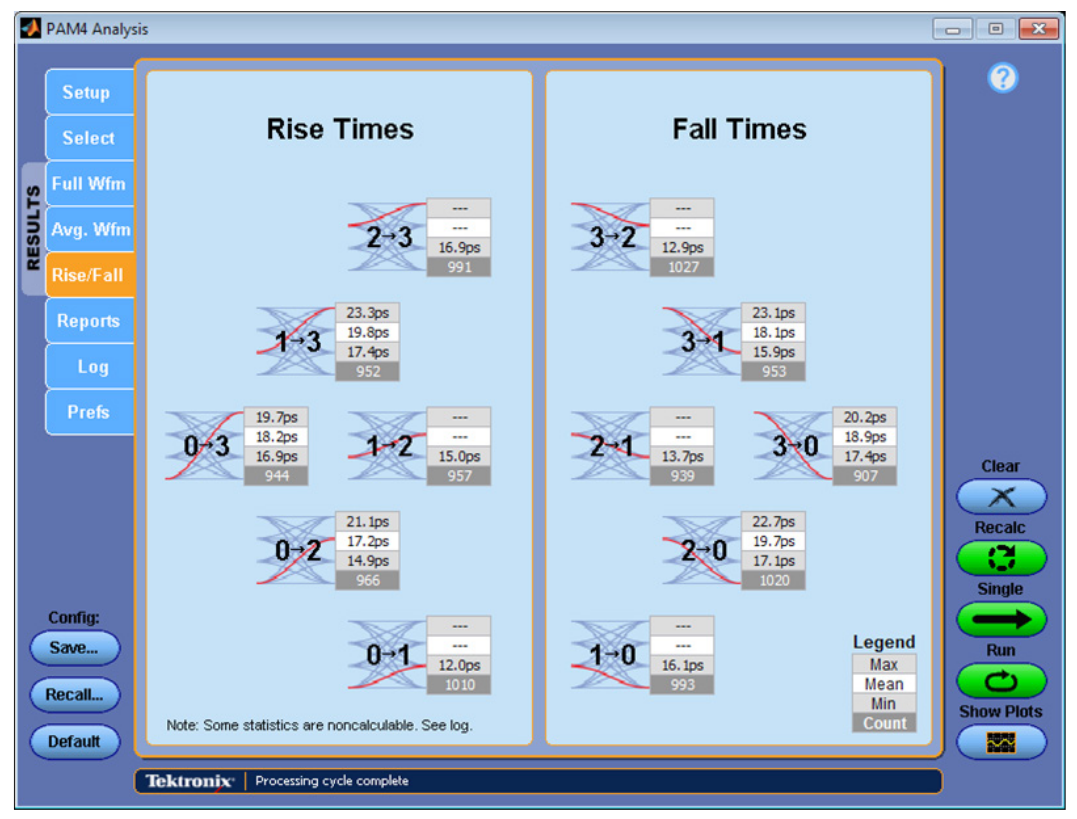
4.3 TRANSITION TIME
The first PAM4 technologies require that symbol decoders sample all three eyes at a common time-delay, tcenter, usually defined at the midpoint of the middle eye (though some optical applications already accommodate eye timing skew by permitting the time-delay positions of the three slicers to vary). For the three eye diagrams to align, the rise/fall times for transitions like 0-1, 0-2, 0-3 should be nearly the same, but the slew rates for these transitions should follow the ratio 1:2:3. Variation of rise and fall times, Figure 7, indicates nonlinearities in the three eyes: Eye compression is the variation of the vertical symbol levels and eye timing skew is the timing variation of the eye centers.
Transition times are required to be longer than specified minimum values to reduce high frequency content that can aggravate crosstalk. Typically trise/fall ≥ 9.5 ps for 26 GBd.
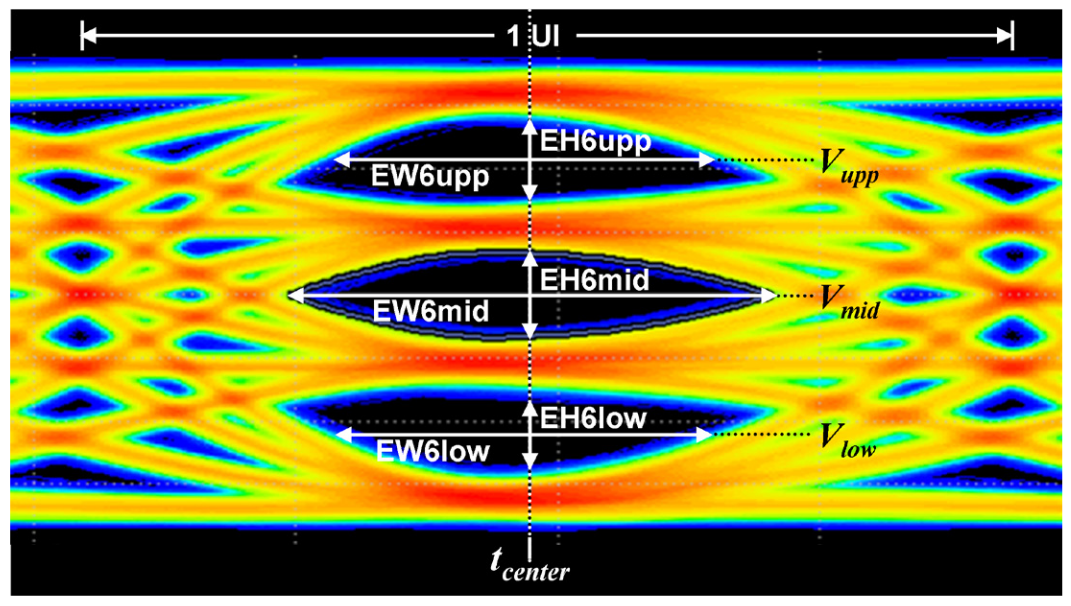
4.4 EH AND EW—EYE HEIGHT AND EYE WIDTH
EH6 (eye height defined with respect to SER = 1E-6) and EW6 (eye width at SER = 1E-6) are primarily requirements of electrical signals but provide excellent quantitative measures for optical signal quality too.
EH6 and EW6 are measured the same way for each of the three PAM4 eye diagrams as they were for the single NRZ eye diagram except that they are extracted from SER-contours rather than BER-contours.
The sampling time is defined to be the same for all three eyes, tcenter, and is given by the center of the longest line that reaches across the SER = 1E-6 contour of the middle eye, Figure 8.Similarly, the three voltage slicer thresholds, Vlow, Vmid, and Vupp, are given by the midpoints of EH6low, EH6mid, and EH6upp.
Since the system SER is limited by the smallest eye opening, the weakest link in the chain, the standards specify minimum acceptable values for the smallest of the three eye widths and heights:

After reference receiver equalization, satisfactory transmitters should be capable of about EW6 ≥ 0.2 UI and EH6 ≥ 30 mV depending on application.
4.5 SNDR—SIGNAL TO NOISE AND DISTORTION RATIO
Signal-to-noise-and-distortion ratio (SNDR) is a signal quality figure of merit that compares electrical signal strength to the combination of random noise and harmonic distortion.
Since SNDR is an automated oscilloscope measurement we give a complete conceptual description in this section so that you’ll understand what you’re measuring and how it should be interpreted. The algorithmic details are in the standard.
SNDR is measured at the transmitter output and accounts for transmitter noise and distortion but is independent of insertion loss and ISI (inter-symbol interference). Unlike TDECQ, SNDR does not account for the noise floor of the oscilloscope.
We derive SNDR from a linear fit to the measured waveform. The fit is performed on a waveform acquisition of at least one PRBS13Q repetition. Let the measured waveform be y(k), where k runs from 1 to the product of the number of samples per symbol and the length of the test pattern. The pulse response, p(k), is extracted from the combination of the measured waveform and the ideal symbol levels of the PRBS13Q pattern. The pulse response is then used to derive a linear fit to the waveform, f(k). The signal strength is the maximum value of the pulse response, pmax = max{p(k); for all k}.
The sample-by-sample fit error is e(k) = f(k) – y(k), the deviation of the fit and the measurement. The distortion, se , is given by the root mean square of the fit error, e(k):

SNDR is given by

In most cases SNDR must be larger than 31 dB.
The signal noise is measured at each of the four symbol levels on low slope runs of at least six consecutive PAM4 signals. The average of the four measurements gives sn.
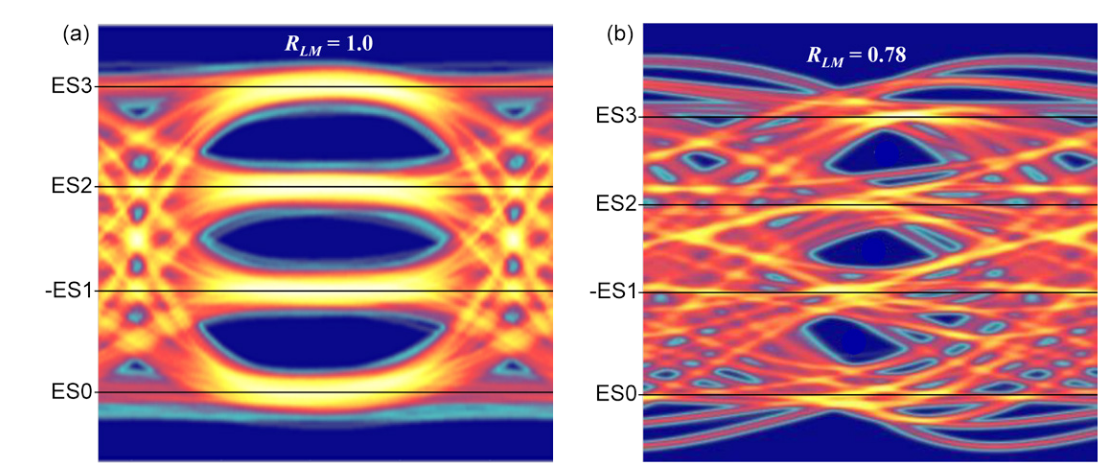
4.6 LEVEL SEPARATION MISMATCH RATIO - RLM
The level separation mismatch ratio is a requirement for electrical PAM4 signals that indicates the vertical linearity of the signal. It measures amplitude compression in a parameter, RLM that runs from zero to one. In the extreme cases, RLM = 1 indicates that the three eyes are equally spaced and RLM = 0 indicates that at lease one of the three eyes has collapsed.
To measure RLM , measure the mean levels of the three symbol levels, V0, V1, V2, and V3. Determine the midrange voltage,

The mean symbol voltages are mapped into normalized effective symbols, Figure 9: V0 ES0 = -1 and V3 ES3 = +1 with ES1 and ES2 given by

The level separation mismatch ratio is

A signal that is linear in voltage would have equally spaced symbol levels: (-1, -1/3, +1/3, +1) = (ES0, -ES1, ES2, ES3) and RLM = 1.0. The standards typically set minimum requirements on RLM in the range from 0.75 to 0.95 depending on application.
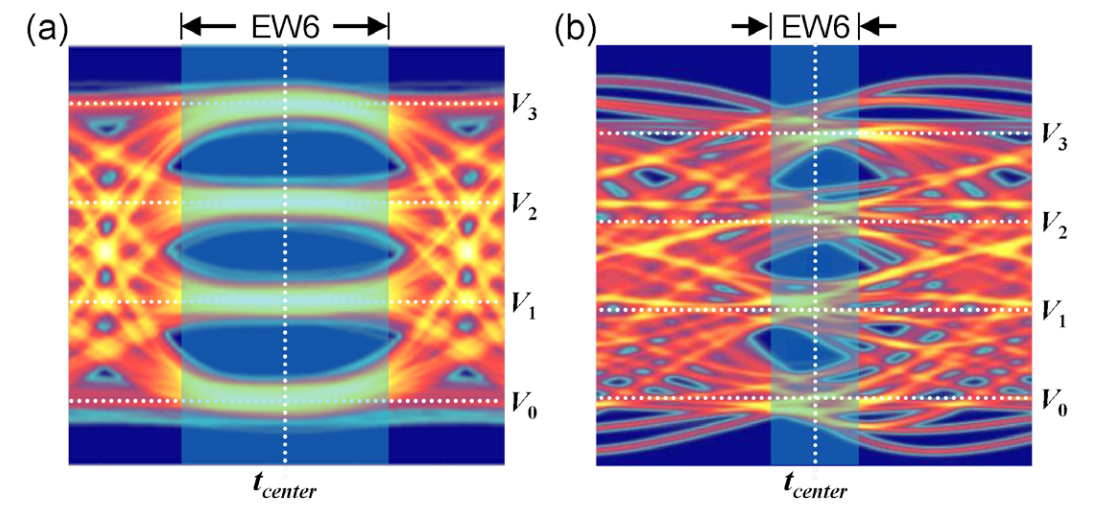
4.7 ESMW - EYE SYMMETRY MASK WIDTH
The ESMW (eye symmetry mask width) test is unlike mask tests performed on NRZ eye diagrams. The ESMW mask, Figure 10, is a vertical stripe with width given by the minimum EW6 requirement centered on the midpoint of the middle eye, tcenter. A signal passes if the horizontal eye openings of all three eyes extend at least to the mask.
The ESMW test is especially effective with signals whose three PAM4 eye diagrams aren’t aligned vertically; the eyes in Figure 10b have inter-eye timing skew. All three eyes could be wide open and have ideal level separation mismatch ratio, RLM = 1, but if they aren’t aligned in time, then a compliant receiver that samples all three eyes simultaneously won’t be able to achieve the minimum required SER.
5. Critical Test Equipment Requirements
To perform accurate debug and compliance tests of optical transceivers you need a high performance, wide bandwidth oscilloscope equipped with an optical to electrical, O/E, convertor with great linearity and sensitivity and an extremely low noise floor.
The Tektronix DPO70000SX ATI real time oscilloscopes deliver industry leading jitter and noise floors with bandwidth options up to 70 GHz. The key component for making the industry’s lowest-noise optical PAM4 measurements are the Tektronix DPO7OE1 and DPO7OE2 optical probes. The DPO7OE1 O/E convertor is a 33 GHz, broad wavelength optical probe with the industry’s lowest optical noise floor: 6.9 µW RMS. The all new DPO7OE2 O/E convertor is the industry’s first optical probe with sufficient bandwidth, 59 GHz, to analyze 53G signals.
Their well earned reputation for combining low noise and wide bandwidth at reasonable prices has made equivalent time sampling scopes a common choice for 28+ GBd PAM4 compliance testing. But with industry leading phase and magnitude linearity plus O/E noise floors that compete with their equivalent-time siblings, the Tektronix DPO70000SX Performance Oscilloscope combined with DPO7OE1 or DPO7OE2 optical probes, Figure 11, provide an alternative with unparalleled flexibility:
- Define receiver filters and set the effective bandwidth, Figure 12. Each standard specifies a filter to assure that the oscilloscope faithfully reproduces the signals as they appear on receiver inputs. You can choose a wide variety of filters through the analysis user interface or design and implement your own in software or MathCad.
- Emulate a wide variety of clock recovery designs, Figure 12. Experiment with different PLL (phase-locked loop) and DSP-based CR algorithms to find schemes that can recover and lock to a data-rate clock in the high ISI and low SNR PAM4 environment. Export the reconstructed clock waveform to a reference channel for viewing or store it for further analysis.
- Experiment with different equalization schemes, Figure 12. Vary the number of FFE and DFE taps, automatically optimize CTLE gain, FFE taps, and DFE taps, or use the interface to create your own equalizer.
- Isolate PAM4 events of interest with visual triggering.
- Use the Error Navigator to analyze PAM4 symbol errors, Figure 13. Four level signals pose problems for physical error detectors. With the Error Navigator, symbol errors can be located, identified, and compared to the ideal transmitted symbols, recovered clock, and slicer thresholds.
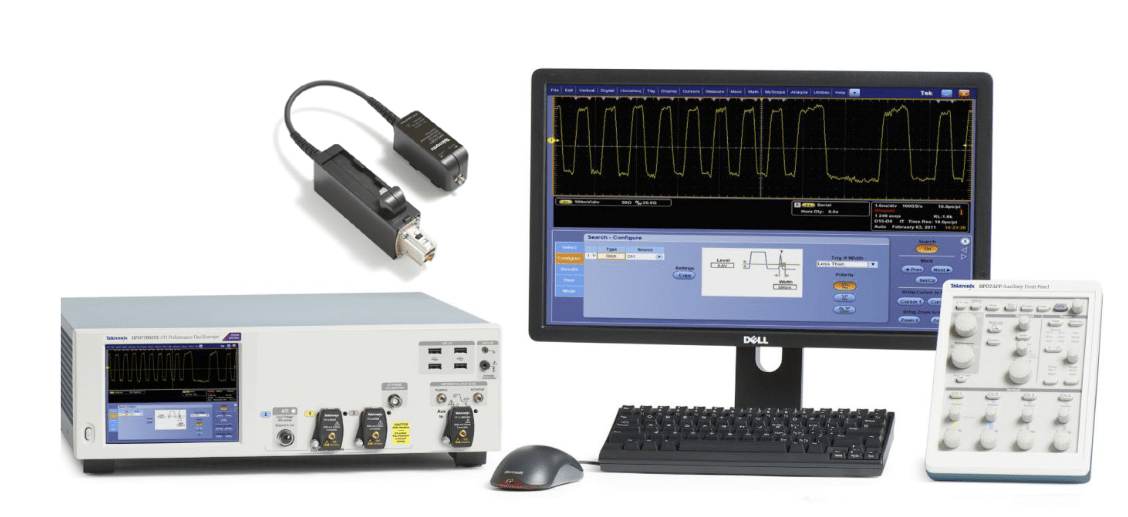
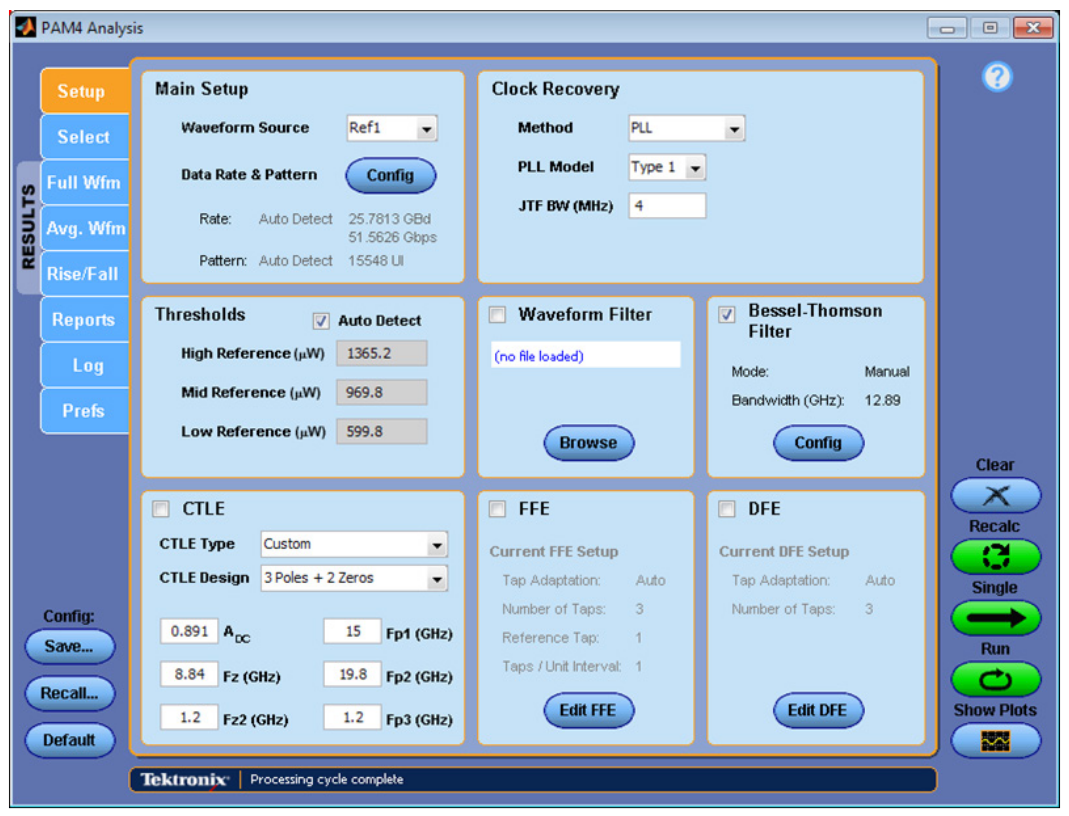

Since they use standard connections, the DPO7OE1 and DPO7OE2 optical probes can also serve as O/E convertors for other instruments, like the error detector of a BERT.
With a DPO70000SX ATI real time oscilloscope and DPO7OE1 or DPO7OE2 optical probes equipped with software options PAM4-O (PAM4 analysis software for optical systems), PAM4 (PAM4 analysis software for electrical systems), SDLA64 (Serial Data Link Analyzer channel de-embedding, embedding, and equalization), DJAN (DPOJET Noise Analysis), and DJA (DPOJET Eye and Jitter Analysis), you can measure every test discussed in this paper plus all of those listed in Table 4.
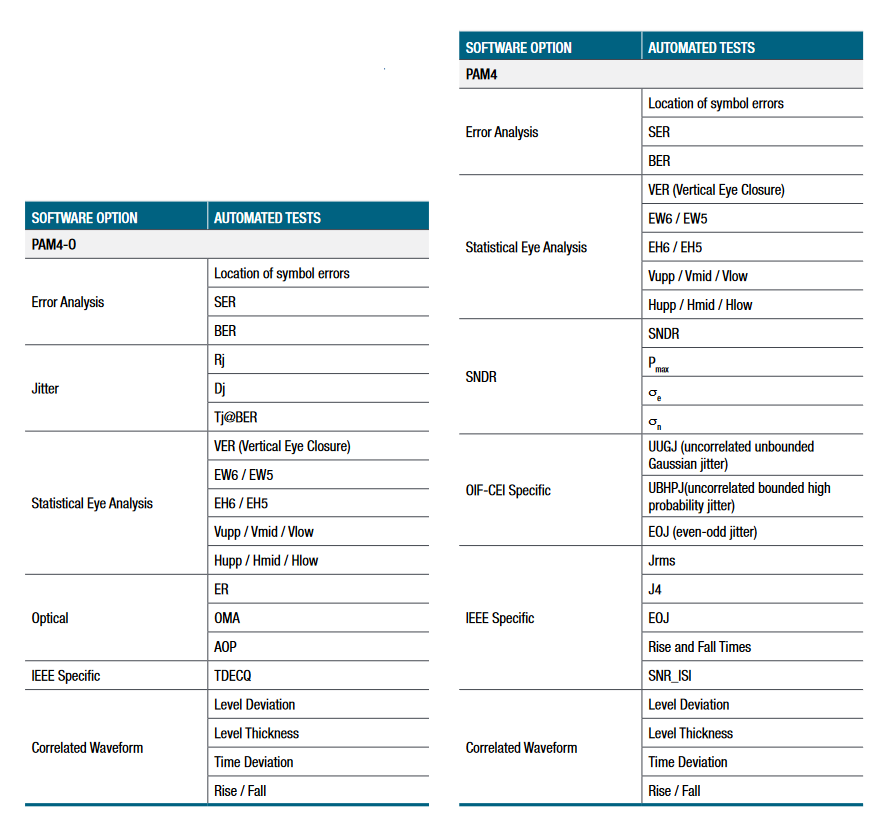