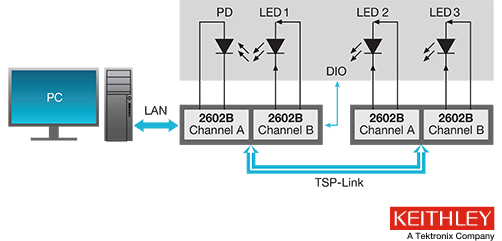
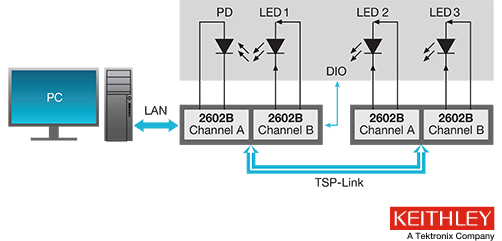
Through the use of laser diodes, 3D sensors can determine the distance and contour of objects based on the time it takes to detect the reflected light while also looking at factors such as the distortion of a reflected grid of light sources. This information is then used to construct 3D images in conjunction with a conventional camera.
This type of depth or 3D sensing technology has been around for some time for applications such as building 3D models for CAD designers, sensors for industrial controls, and more famously in Microsoft’s Kinect motion sensing input device for Xbox game consoles. Now, however, 3D sensing technology is going full-on mainstream as smartphone suppliers race to incorporate 3D sensors into their next generation of smartphones. Initially, 3D sensors are being added to the front-facing camera on handsets where they will be used for everything from facial recognition to unlock the phone, 3D selfies, augmented reality gaming, and likely much more.
The adoption of 3D sensing for smartphones is driving down size (it must fit in a handset) and cost while driving up performance. This is also enabling expanded use of 3D sensing in other end applications such as automotive and industrial robotics. While the volumes may not be as high as with smartphones for these follow-on applications, the amount of testing will be much greater due to the nature of the end application. For example, for the automotive industry, the application will be safety-based driver assist for collision avoidance, blind spot detection, parking assist, and driver drowsiness detection -- and eventually autonomous driving.
The laser diode that emits the 3D sensing light is one of the most critical elements of a 3D device that needs to be tested and verified. The light-current-voltage (LIV) characteristics of the diode need to be tested at multiple steps in the supply chain process. Testing LIV characteristics requires a precise current to be sourced through the diode and synchronized with light intensity and spectral measurements performed.
The Keithley Division here at Tektronix has been working with customers to test various types of light emitting diodes for more than 20 years. Building on this experience, our engineers have perfected the signal quality and speed requirements for this type of testing through innovations such as test script processor (TSP®) technology and pulsed current SourceMeter® Source Measure Unit (SMU) instruments. In fact, we’re so entrenched in this industry that customers don’t call the instruments an SMU or SourceMeter, they call them the “Keithley.”
Test set-up for diode-based devices used in 3D sensors.
Keithley test solutions are widely adopted for testing the laser diodes used in 3D sensing technology. Over the coming weeks, we will be taking a closer look at 3D sensing and what’s involved with testing laser diodes. You also might want to check out our 3D sensing application page for more details on using Keithley instruments to perform electrical testing on diode-based devices. If you’re working on projects involving diode-based optical devices and 3D sensing, it would be great to hear from you about the characterization, validation and other test challenges you’re facing – please post up in the comments below.